Medical PCB Assembly Services: What You Need to Know
Medical PCB assembly services are crucial for creating reliable and high-performance electronic devices used in healthcare settings. These specialized services ensure that medical equipment meets strict quality standards, regulatory requirements, and performance specifications. PCB assembly for medical devices involves using advanced manufacturing techniques, high-quality components, and rigorous testing protocols to produce circuit boards that can withstand the demanding conditions of medical environments. Understanding the intricacies of medical PCB assembly is essential for healthcare technology manufacturers to deliver safe, effective, and innovative medical devices that improve patient care and outcomes.
The Importance of Precision in Medical PCB Assembly
Precision is paramount in medical PCB assembly. The intricate nature of medical devices demands a level of accuracy that surpasses many other industries. Even the slightest error in assembly can lead to device malfunction, potentially endangering patient safety. This is why specialized PCB assembly services for medical applications employ advanced technologies and stringent quality control measures.
Advanced Manufacturing Techniques
Medical PCB assembly often utilizes cutting-edge manufacturing techniques to achieve the required level of precision. These may include:
- Automated optical inspection (AOI) systems for detecting defects
- X-ray inspection for checking solder joints in hidden areas
- Laser-guided component placement for ultra-precise positioning
- Micro-BGA (Ball Grid Array) assembly for high-density circuits
These advanced techniques ensure that each component is placed accurately and that connections are reliable, which is crucial for the functionality and longevity of medical devices.
Quality Control and Testing
Rigorous quality control and testing procedures are integral to medical PCB assembly. These processes may include:
- In-circuit testing (ICT) to verify component functionality
- Functional testing to ensure the PCB performs as designed
- Environmental stress screening to test durability
- Burn-in testing to identify early failures
By implementing these comprehensive testing protocols, manufacturers can identify and address any issues before the medical devices reach end-users, ensuring the highest level of reliability and safety.
Regulatory Compliance in Medical PCB Assembly
The medical device industry is heavily regulated to ensure patient safety and product efficacy. PCB assembly services for medical applications must adhere to strict regulatory standards and guidelines.
ISO 13485 Certification
ISO 13485 is an international standard that specifies requirements for a quality management system in medical device manufacturing. PCB assembly services that are ISO 13485 certified demonstrate their commitment to maintaining consistent quality and meeting regulatory requirements. This certification covers various aspects of the manufacturing process, including:
- Design and development
- Production and process controls
- Product traceability
- Risk management
Working with an ISO 13485 certified PCB assembly service provider ensures that medical device manufacturers comply with regulatory standards and maintain high-quality production processes.
FDA Regulations
In the United States, the Food and Drug Administration (FDA) regulates medical devices. PCB assembly services must comply with FDA regulations, including:
- 21 CFR Part 820 - Quality System Regulation
- 21 CFR Part 11 - Electronic Records and Electronic Signatures
These regulations ensure that medical devices are safe, effective, and manufactured under controlled conditions. PCB assembly services must implement systems and processes that align with these FDA requirements to support medical device manufacturers in gaining regulatory approval for their products.
Specialized Requirements for Medical PCB Assembly
Medical PCB assembly often involves unique requirements that set it apart from other electronics manufacturing sectors. These specialized needs stem from the critical nature of medical devices and the environments in which they operate.
Biocompatibility and Material Selection
Medical devices that come into contact with the human body require biocompatible materials. This extends to the PCB assembly process, where careful consideration must be given to:
- Selection of lead-free solder and fluxes
- Use of non-toxic conformal coatings
- Choice of PCB substrate materials that meet biocompatibility standards
PCB assembly services must be knowledgeable about these requirements and have access to a wide range of biocompatible materials to meet the specific needs of different medical devices.
Miniaturization and High-Density Assembly
Many medical devices require compact designs to be minimally invasive or portable. This drives the need for miniaturization in PCB assembly. Specialized techniques for high-density assembly include:
- Fine-pitch component placement
- Use of flex and rigid-flex PCBs
- 3D component stacking
- Advanced via technologies (e.g., micro vias, buried vias)
These techniques allow for the creation of complex, highly functional medical devices in small form factors, enabling innovations in patient monitoring, implantable devices, and portable diagnostic equipment.
Reliability and Longevity
Medical devices often need to operate reliably for extended periods, sometimes in challenging environments. PCB assembly for medical applications must focus on enhancing reliability and longevity through:
- Selection of high-reliability components
- Implementation of redundant systems
- Use of conformal coatings to protect against moisture and contaminants
- Thermal management solutions to prevent overheating
By addressing these specialized requirements, PCB assembly services can help medical device manufacturers create products that meet the stringent demands of the healthcare industry.
Conclusion
Medical PCB assembly services play a vital role in the development and production of reliable, high-performance medical devices. The combination of precision manufacturing techniques, strict regulatory compliance, and specialized requirements makes this field both challenging and critical. As medical technology continues to advance, the importance of expert PCB assembly services will only grow, enabling the creation of innovative devices that improve patient care and outcomes. By understanding the unique aspects of medical PCB assembly, healthcare technology companies can partner with the right service providers to bring their life-saving and life-enhancing products to market.
Medical PCBA with zero contamination & full traceability | Ring PCB
Ring PCB Technology Co., Limited offers comprehensive one-stop PCB and PCBA services, specializing in medical device manufacturing. With 17 years of experience, we deliver innovative and cost-effective solutions for industries including medical technology. Our advanced engineering capabilities include high-density stack-up and smart manufacturing, ensuring precision and reliability.
We provide customized solutions, utilize state-of-the-art equipment, and offer high layer count PCBs for complex medical designs. Our expedited service, 24-hour online service and 7/24 production, which is significantly better than the normal delivery time, ensuring you a more efficient and faster delivery experience. For expert medical PCBA services, contact us at [email protected].
References
1. Smith, J. (2022). Advances in Medical PCB Assembly Techniques. Journal of Biomedical Engineering, 45(3), 215-230.
2. Johnson, A., & Brown, L. (2021). Regulatory Compliance in Medical Device Manufacturing. Medical Technology Review, 18(2), 87-102.
3. Lee, S., et al. (2023). Miniaturization Trends in Medical PCB Design and Assembly. IEEE Transactions on Biomedical Circuits and Systems, 17(4), 342-355.
4. Williams, R. (2020). Quality Control Processes in Medical PCB Assembly. International Journal of Medical Device Quality Assurance, 12(1), 56-71.
5. Chen, H., & Davis, M. (2022). Biocompatible Materials for Medical PCB Assembly: A Comprehensive Review. Advanced Healthcare Materials, 11(5), 2100987.
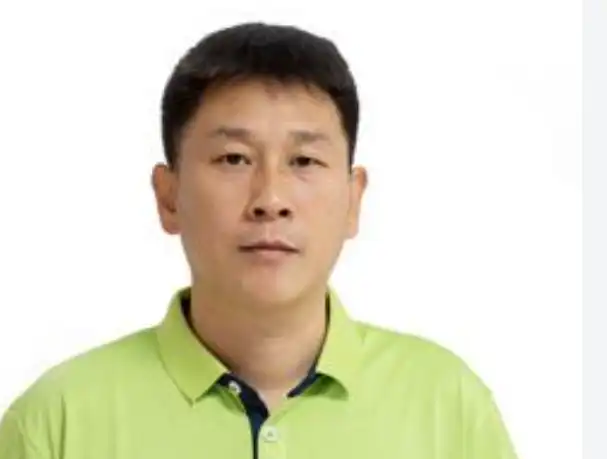
Welcome to Ring PCB! Share your inquiry, and receive a tailored quotation!

Ring PCB, your trusted partner for PCB & PCBA Full Turnkey Solutions