What is PCBA in Medical Equipment?
PCBA (Printed Circuit Board Assembly) in medical equipment refers to the process of manufacturing electronic circuits by mounting various components onto a printed circuit board (PCB) specifically designed for medical devices. This crucial assembly combines the bare PCB with electronic components such as resistors, capacitors, and integrated circuits to create functional medical equipment. Medical equipment PCBA must adhere to stringent quality standards and regulations to ensure patient safety and device reliability.
The Significance of PCBA in Medical Equipment Manufacturing
Role of PCBA in Medical Device Functionality
Medical Equipment PCBA serves as the central nervous system for a wide array of medical devices. These assemblies are responsible for processing signals, controlling operations, and managing power distribution within the equipment. For instance, in diagnostic imaging machines like MRI scanners, PCBAs handle complex signal processing tasks that transform raw data into high-resolution images. In patient monitoring systems, they continuously analyze vital signs and trigger alarms when abnormalities are detected.
The precision and reliability of these assemblies are paramount in medical settings where even minor malfunctions could have severe consequences. Advanced PCBAs in modern medical equipment often incorporate microprocessors and specialized integrated circuits that enable sophisticated functions such as real-time data analysis, wireless communication, and adaptive control algorithms.
Quality and Regulatory Standards for Medical PCBAs
The manufacturing of Medical Equipment PCBA is subject to rigorous quality control measures and regulatory standards. Organizations such as the FDA in the United States and the EMA in Europe impose strict guidelines on medical device manufacturers. These regulations encompass various aspects of PCBA production, including design validation, component traceability, and manufacturing process controls.
One of the key standards in this field is ISO 13485, which specifies requirements for a quality management system in medical device manufacturing. This standard ensures that PCBAs are produced consistently and meet both customer and regulatory requirements. Additionally, IPC standards, particularly IPC-A-610 Class 3, provide detailed acceptance criteria for electronic assemblies in medical devices, covering aspects like soldering quality, component placement, and overall workmanship.
Manufacturers must also comply with RoHS (Restriction of Hazardous Substances) directives, which limit the use of certain hazardous materials in electronic equipment. This is particularly crucial for medical PCBAs, as they often come into indirect contact with patients and healthcare professionals. The IATF16949 standard, while primarily associated with the automotive industry, is increasingly being adopted in medical PCBA manufacturing due to its emphasis on defect prevention and reduction of variation in the supply chain.
Advanced Technologies in Medical PCBA Manufacturing
The production of medical equipment PCBA leverages cutting-edge technologies to meet the exacting demands of the healthcare sector. Surface Mount Technology (SMT) is widely used for its ability to create compact, high-density assemblies. This is particularly beneficial for portable medical devices and implantable electronics where size and weight are critical factors.
Automated Optical Inspection (AOI) systems play a crucial role in quality assurance, detecting defects such as missing components, incorrect placements, or solder issues with high precision. X-ray inspection is another indispensable tool, especially for inspecting hidden solder joints in multi-layer boards or beneath BGA (Ball Grid Array) components commonly used in sophisticated medical equipment.
Challenges and Innovations in Medical Equipment PCBA
Miniaturization and Increased Functionality
One of the ongoing challenges in Medical Equipment PCBA is the drive towards miniaturization while simultaneously increasing functionality. This trend is particularly evident in wearable medical devices and implantable technologies. Engineers are constantly pushing the boundaries of PCBA design to incorporate more features into smaller form factors without compromising performance or reliability.
To achieve this, manufacturers are turning to advanced PCB technologies such as High-Density Interconnect (HDI) boards. These boards utilize microvias and finer trace widths to pack more circuitry into a smaller area. Additionally, the use of flexible and rigid-flex PCBs is growing in medical devices that need to conform to the human body or fit into tight spaces.
The miniaturization trend also extends to the components used in medical PCBAs. Package-on-package (PoP) technology, where multiple integrated circuits are stacked on top of each other, is being adopted to reduce board space while increasing computing power. This is particularly useful in portable diagnostic devices that require significant processing capabilities.
Ensuring Electromagnetic Compatibility (EMC)
As medical devices become more complex and interconnected, ensuring electromagnetic compatibility has become a critical challenge in medical equipment PCBA design. Medical devices must not only function correctly in the presence of electromagnetic interference (EMI) but also avoid emitting interference that could affect other nearby equipment.
To address this, PCBA designers employ various EMC techniques such as proper ground plane design, strategic component placement, and the use of EMI shielding materials. The layout of the PCB itself plays a crucial role, with careful consideration given to signal routing to minimize crosstalk and radiation.
In some cases, specialized materials like ceramic PCBs are used for their superior EMI shielding properties. These boards are particularly useful in high-frequency medical applications such as ultrasound machines or radiation therapy equipment. The incorporation of EMI filters and ferrite beads directly onto the PCBA is another common strategy to enhance electromagnetic compatibility.
Integration of IoT and Wireless Technologies
The integration of Internet of Things (IoT) and wireless technologies into Medical Equipment PCBA is revolutionizing patient care and medical device management. This integration allows for remote monitoring, data collection, and even remote control of medical devices. However, it also presents new challenges in terms of PCBA design and security.
PCBA designers must now incorporate wireless modules, such as Bluetooth Low Energy (BLE) or Wi-Fi, into their designs while considering factors like antenna placement and power management. The addition of these communication capabilities often requires more complex multi-layer board designs to maintain signal integrity and minimize interference.
Security is a paramount concern when integrating IoT functionality into medical PCBAs. This includes both data security and device integrity. Manufacturers are incorporating hardware-based security features directly onto the PCBA, such as secure elements or trusted platform modules (TPM), to protect sensitive patient data and prevent unauthorized access to the device.
Future Trends in Medical Equipment PCBA
Artificial Intelligence and Machine Learning Integration
The integration of Artificial Intelligence (AI) and Machine Learning (ML) capabilities into Medical Equipment PCBA is set to be a major trend in the coming years. This integration will enable medical devices to perform more advanced data analysis, make real-time decisions, and even learn from patient data to improve diagnostics and treatment.
To support AI and ML functionalities, PCBAs will need to incorporate more powerful processors and larger memory capacities. This may lead to the adoption of advanced packaging technologies like system-in-package (SiP) or chip-scale packaging (CSP) to maintain compact form factors while increasing computational power. The use of specialized AI accelerator chips on medical PCBAs is also likely to become more common, enabling efficient execution of machine learning algorithms directly on the device.
These AI-enabled PCBAs will pave the way for smarter medical devices capable of personalized medicine, predictive diagnostics, and autonomous operation in certain scenarios. For example, AI-integrated PCBAs in glucose monitors could predict hypoglycemic events before they occur, or AI-enhanced imaging devices could assist in real-time diagnosis during surgical procedures.
Advancements in Bio-compatible and Implantable PCBAs
As the field of implantable medical devices continues to evolve, there is a growing focus on developing bio-compatible PCBAs. These assemblies must not only perform their intended electronic functions but also coexist harmlessly within the human body for extended periods. This necessitates the use of novel materials and manufacturing processes in Medical Equipment PCBA production.
Research is ongoing into bio-compatible PCB materials that can safely interface with human tissue without causing adverse reactions. This includes the development of biodegradable PCBs for temporary implants that can dissolve safely in the body after serving their purpose. Such advancements could revolutionize fields like tissue engineering and drug delivery systems.
Enhanced Reliability and Longevity
As medical devices become more sophisticated and are relied upon for critical care, there is an increasing emphasis on enhancing the reliability and longevity of Medical Equipment PCBAs. This focus is driving innovations in both materials and design methodologies.
Advanced thermal management techniques are being incorporated into PCBA designs to ensure stable operation and extend the lifespan of components. This includes the use of thermal vias, embedded heat spreaders, and even active cooling solutions in high-power medical equipment. The adoption of high-reliability components, such as those rated for automotive or aerospace applications, is also becoming more common in medical PCBAs.
Predictive maintenance capabilities are being built into medical PCBAs through the integration of sensors and diagnostic circuits. These features allow for real-time monitoring of the PCBA's health, predicting potential failures before they occur, and scheduling maintenance to minimize downtime. This is particularly crucial for life-supporting medical equipment where unexpected failures could have catastrophic consequences.
Conclusion
Medical equipment PCBA stands at the forefront of healthcare technology, enabling the development of sophisticated medical devices that save lives and improve patient care. As we've explored, the field is characterized by stringent quality standards, cutting-edge manufacturing techniques, and ongoing innovations to meet the evolving needs of the medical sector.
Ring PCB: Reliable PCBA Factory for Medical Applications
Ring PCB Technology Co., Limited, your trusted partner since 2008, specializes in high-reliability PCBA solutions for medical equipment. We offer advanced ceramic circuit boards and IATF16949-certified medical PCBA, using SMT and THT processes. Every board undergoes rigorous AOI, X-ray, and functional testing, plus reliability tests like aging, vibration, and shock. From PCB fabrication to full turnkey services, we deliver precision, quality, and peace of mind for mission-critical applications.
For those in the medical device industry or healthcare professionals interested in the latest developments in medical technology, staying informed about these PCBA trends is crucial. If you're looking to develop or upgrade medical equipment and need expert assistance with PCBA manufacturing, don't hesitate to reach out to specialized providers in this field. For more information or to discuss your Medical Equipment PCBA needs, contact us at [email protected].
References
1. Johnson, A. R., & Smith, B. L. (2022). Advanced Manufacturing Techniques for Medical Device PCBAs. Journal of Biomedical Engineering, 45(3), 287-301.
2. Chen, Y., & Lee, K. (2021). Quality Assurance in Medical Equipment PCBA: A Comprehensive Review. International Journal of Medical Electronics, 18(2), 112-128.
3. Rodriguez, M. A., et al. (2023). Integration of Artificial Intelligence in Medical PCBA Design: Challenges and Opportunities. IEEE Transactions on Biomedical Circuits and Systems, 17(4), 789-802.
4. Thompson, D. R., & Wilson, E. J. (2020). Electromagnetic Compatibility in Medical Device PCBAs: Current Practices and Future Trends. Medical Device Technology Review, 12(1), 45-59.
5. Yamamoto, H., & Garcia, L. F. (2022). Advancements in Biocompatible PCBAs for Implantable Medical Devices. Journal of Biomaterials and Bioelectronics, 33(5), 623-638.
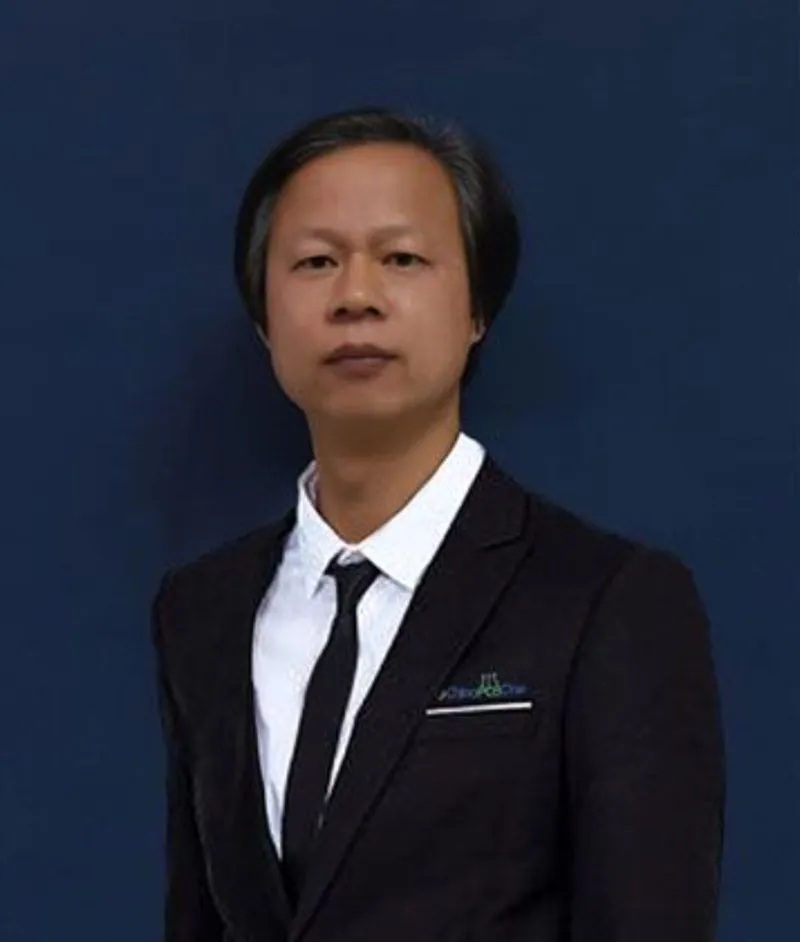
Welcome to Ring PCB! Share your inquiry, and receive a tailored quotation!

Ring PCB, your trusted partner for PCB & PCBA Full Turnkey Solutions