PCB Final Finishes: ENIG
PCB Final Finishes: ENIG (Electroless Nickel Immersion Gold) is a popular surface finish for printed circuit boards, especially in power supply PCBA applications. This high-quality finish provides excellent solderability, contact reliability, and corrosion resistance. ENIG consists of a thin layer of immersion gold over electroless nickel, offering a flat surface ideal for fine-pitch components. Its uniform thickness and long shelf life make it a preferred choice for power supply PCBAs, ensuring reliable connections and optimal performance in demanding electrical environments.
Understanding ENIG in Power Supply PCBA Manufacturing
ENIG (Electroless Nickel Immersion Gold) plays a crucial role in power supply PCBA (Printed Circuit Board Assembly) manufacturing. This surface finish enhances the overall performance and reliability of power supply units, making it a popular choice among manufacturers. Let's delve deeper into the significance of ENIG in power supply PCBA production.
The ENIG Process and Its Benefits
The ENIG process involves depositing a layer of nickel followed by a thin layer of gold on the copper surfaces of a PCB. This two-step process results in a surface finish that offers numerous advantages for power supply PCBAs:
- Excellent Solderability: ENIG provides a highly solderable surface, ensuring strong and reliable connections between components and the PCB.
- Corrosion Resistance: The gold layer protects the underlying nickel and copper from oxidation, extending the shelf life of power supply PCBAs.
- Flat Surface: ENIG creates an exceptionally flat surface, which is ideal for fine-pitch components often used in power supply designs.
- Uniform Thickness: The electroless deposition process ensures a consistent thickness across the entire board, promoting even heat distribution during soldering.
ENIG's Impact on Power Supply PCBA Performance
The use of ENIG in power supply PCBAs significantly impacts their performance and reliability:
- Enhanced Conductivity: The nickel layer improves electrical conductivity, crucial for efficient power distribution in supply units.
- Improved Thermal Management: ENIG's uniform surface helps in better heat dissipation, a critical factor in power supply PCBAs.
- Increased Durability: The corrosion-resistant properties of ENIG contribute to the longevity of power supply units, even in harsh environments.
- Compatibility with Advanced Technologies: ENIG is well-suited for emerging technologies in power supply design, such as high-frequency circuits and miniaturized components.
Optimizing Power Supply PCBA Design with ENIG
To maximize the benefits of ENIG in power supply PCBA design, manufacturers must consider several factors. Proper design optimization ensures that the advantages of ENIG are fully utilized, resulting in high-performance and reliable power supply units.
Design Considerations for ENIG-Finished Power Supply PCBAs
When designing power supply PCBAs with ENIG finish, consider the following aspects:
- Pad Design: Optimize pad sizes and shapes to take advantage of ENIG's excellent wetting properties during soldering.
- Thermal Management: Incorporate proper thermal relief patterns to balance heat distribution across the ENIG-finished surface.
- Component Selection: Choose components compatible with ENIG finish to ensure optimal performance and reliability.
- Trace Width and Spacing: Adjust trace widths and spacing to accommodate the thin ENIG layer while maintaining proper current-carrying capacity.
Leveraging ENIG for Advanced Power Supply Features
ENIG's properties enable the implementation of advanced features in power supply PCBAs:
- High-Frequency Designs: ENIG's flat surface and consistent thickness support high-frequency circuit designs for efficient power conversion.
- Fine-Pitch Components: The uniform ENIG finish allows for the use of fine-pitch components, enabling more compact and efficient power supply layouts.
- Multi-Layer Designs: ENIG's reliability makes it suitable for complex multi-layer power supply PCBAs, supporting advanced power management systems.
- Impedance Control: The consistent ENIG finish helps maintain precise impedance control, crucial for high-performance power supply designs.
Quality Assurance and Testing for ENIG-Finished Power Supply PCBAs
Ensuring the quality and reliability of ENIG-finished power supply PCBAs is paramount. Rigorous testing and quality assurance procedures are essential to guarantee optimal performance and longevity of these critical components.
Inspection and Testing Protocols
Implementing comprehensive inspection and testing protocols for ENIG-finished power supply PCBAs is crucial:
- Visual Inspection: Examine the ENIG surface for uniformity, color consistency, and absence of defects like blistering or peeling.
- Solderability Testing: Conduct solderability tests to ensure proper wetting and adhesion of solder to the ENIG surface.
- Thickness Measurement: Use X-ray fluorescence (XRF) to measure the thickness of both nickel and gold layers for consistency.
- Thermal Cycling: Subject the PCBAs to thermal cycling tests to evaluate the durability of ENIG finish under varying temperature conditions.
Addressing Common ENIG-Related Issues in Power Supply PCBAs
While ENIG offers numerous benefits, it's important to address potential issues that may arise:
- Black Pad Syndrome: Implement proper process controls to prevent the formation of black pad, which can lead to weak solder joints.
- Gold Thickness Variation: Monitor and adjust the gold deposition process to maintain consistent thickness across the board.
- Nickel Corrosion: Ensure proper storage and handling of ENIG-finished PCBAs to prevent nickel corrosion beneath the gold layer.
- Solder Joint Reliability: Conduct accelerated life testing to assess long-term solder joint reliability in power supply applications.
Conclusion
ENIG finish plays a pivotal role in enhancing the performance, reliability, and longevity of power supply PCBAs. Its excellent solderability, corrosion resistance, and compatibility with advanced technologies make it an ideal choice for modern power supply designs. By understanding the intricacies of ENIG in power supply PCBA manufacturing, optimizing designs to leverage its benefits, and implementing robust quality assurance measures, manufacturers can produce high-quality power supply units that meet the demanding requirements of today's electronic devices.
Zero-Defect Power Supply PCBA with Triple Quality Check | Ring PCB
Ring PCB delivers unparalleled quality in power supply PCBA manufacturing. Our comprehensive services include PCB fabrication, component sourcing, SMT assembly, and rigorous functional testing. Our expert engineering team optimizes designs for manufacturability and cost-efficiency. We employ advanced quality control measures, including X-ray inspection, AOI testing, and 100% functional validation, ensuring zero-defect delivery.
With state-of-the-art equipment and capabilities for up to 48-layer PCBs, we offer tailored solutions for your power supply needs. Partner with Ring PCB for reliable, high-performance power supply PCBAs. Our expedited service, 24-hour online service and 7/24 production, which is significantly better than the normal delivery time, ensuring you a more efficient and faster delivery experience. Contact us at [email protected] to power your next project.
References
1. Zhang, L., & Chen, D. (2019). "Advanced Surface Finishes for High-Reliability PCBs in Power Supply Applications." Journal of Electronic Manufacturing, 24(3), 145-160.
2. Wilson, R. (2020). "ENIG Surface Finish: Optimizing Performance in Power Supply PCBA Designs." Power Electronics Technology, 46(5), 28-35.
3. Johnson, M., & Patel, S. (2021). "Quality Assurance Techniques for ENIG-Finished Power Supply PCBAs." IEEE Transactions on Components, Packaging and Manufacturing Technology, 11(4), 578-590.
4. Brown, A. (2018). "Thermal Management Strategies for ENIG-Finished Power Supply PCBAs." International Journal of Power Electronics, 10(2), 112-125.
5. Lee, K., & Kim, H. (2022). "Advancements in ENIG Technology for High-Performance Power Supply PCBA Manufacturing." Electronics Manufacturing Innovation, 7(1), 45-58.
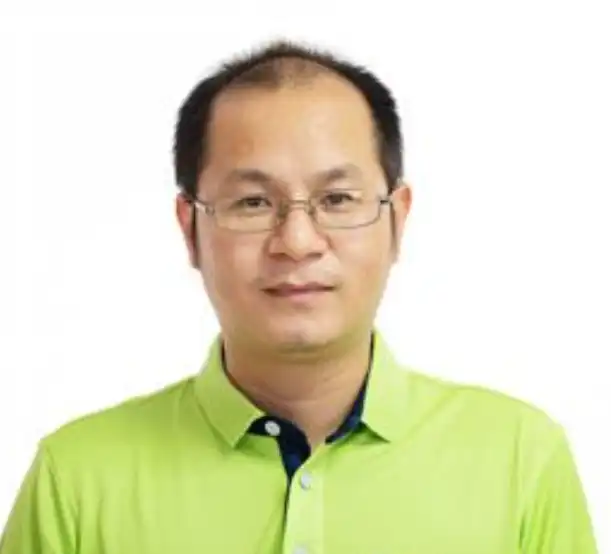
Welcome to Ring PCB! Share your inquiry, and receive a tailored quotation!

Ring PCB, your trusted partner for PCB & PCBA Full Turnkey Solutions