Top Components Used in Industrial PCBA Assemblies
Industrial PCBA (Printed Circuit Board Assembly) forms the backbone of modern industrial electronics. These assemblies integrate various high-performance components to ensure reliability, durability, and functionality in demanding industrial environments. Key components typically found in industrial PCBA include microcontrollers, power management ICs, sensors, communication modules, and rugged connectors. These elements work in harmony to process data, control systems, and facilitate communication in applications ranging from factory automation to energy management. The selection and integration of these components require expertise in industrial-grade electronics and stringent quality control measures to meet the rigorous standards of industrial applications.
Essential Components in Industrial PCBA Design
Microcontrollers and Processors
At the heart of industrial PCBA lies the microcontroller or processor. These components serve as the brain of the assembly, orchestrating operations and processing data. Industrial-grade microcontrollers are designed to withstand harsh environments, offering features like extended temperature ranges and enhanced electromagnetic interference (EMI) protection. For instance, ARM Cortex-M series processors are widely used in industrial applications due to their balance of performance and power efficiency.
The selection of a microcontroller for industrial PCBA depends on various factors, including processing power requirements, memory capacity, and peripheral interfaces. Many industrial applications demand real-time processing capabilities, making microcontrollers with deterministic behavior crucial. Additionally, it often incorporates redundancy features, such as watchdog timers and error-correcting code (ECC) memory, to ensure system reliability even in critical operations.
Power Management ICs
Power management is a critical aspect of industrial PCBA design. Power Management Integrated Circuits (PMICs) play a vital role in regulating and distributing power across the assembly. These components ensure stable and efficient power delivery, which is essential for the reliable operation of industrial equipment. Industrial PMICs are designed to handle wide input voltage ranges and provide multiple output voltages to cater to various components on the board.
Advanced PMICs in industrial PCBA often include features like over-voltage protection, under-voltage lockout, and thermal shutdown to safeguard the system against power anomalies. Some PMICs also incorporate power sequencing capabilities, ensuring that different components on the PCBA power up in the correct order. This feature is particularly important in complex industrial systems where improper power-up sequences can lead to system instability or damage.
Sensors and Data Acquisition Components
Industrial PCBA assemblies frequently incorporate a variety of sensors to monitor environmental conditions, process parameters, and equipment status. Common sensor types include temperature sensors, pressure sensors, accelerometers, and gas sensors. These sensors provide crucial data for process control, predictive maintenance, and safety monitoring in industrial applications.
High-precision analog-to-digital converters (ADCs) are often paired with these sensors to ensure accurate data acquisition. Industrial-grade ADCs offer features like high resolution (16-bit or higher), low noise, and wide operating temperature ranges. Some industrial PCBA designs also incorporate digital signal processors (DSPs) to perform real-time signal processing on sensor data, enabling advanced analytics and control algorithms directly on the board.
Communication Interfaces in Industrial PCBA
Ethernet Controllers and PHYs
Industrial Ethernet has become the de facto standard for communication in many industrial applications. Industrial PCBA assemblies often include Ethernet controllers and PHY (physical layer) chips to enable high-speed, reliable network connectivity. These components support protocols like EtherCAT, PROFINET, and EtherNet/IP, which are widely used in industrial automation and control systems.
Industrial Ethernet components in PCBA are designed to withstand electromagnetic interference and support features like Time-Sensitive Networking (TSN) for deterministic communication. Some advanced industrial PCBA designs incorporate multi-port Ethernet switches, enabling the creation of complex network topologies directly on the board. This integration simplifies system architecture and improves overall reliability by reducing the number of external connections.
Fieldbus and Industrial Protocol Interfaces
While Ethernet is gaining prominence, many industrial systems still rely on traditional fieldbus protocols. Industrial PCBA assemblies often include components to support interfaces like PROFIBUS, Modbus, and CAN (Controller Area Network). These interfaces require specialized transceivers and protocol controllers to ensure compliance with the respective standards.
The integration of multiple communication interfaces on a single PCBA allows for greater flexibility and interoperability in industrial systems. For instance, a PCBA might include both Ethernet and CAN interfaces, enabling it to communicate with modern Ethernet-based systems as well as legacy CAN-based equipment. This versatility is crucial in industrial environments where equipment from different generations often needs to coexist and interact seamlessly.
Wireless Communication Modules
The Industrial Internet of Things (IIoT) has driven the adoption of wireless communication in industrial PCBA designs. Components like Wi-Fi modules, Bluetooth Low Energy (BLE) chips, and cellular modems are increasingly being integrated into industrial PCBA assemblies. These wireless interfaces enable remote monitoring, data collection, and control in applications where wired connections are impractical or cost-prohibitive.
Industrial-grade wireless modules are designed to operate reliably in noisy electromagnetic environments and often include features like extended range and low power consumption. Some advanced product designs incorporate multiple wireless technologies, allowing for redundant communication paths or the ability to choose the most appropriate protocol based on the application requirements.
Rugged Design Elements for Industrial PCBA
Protective Coatings and Encapsulation
Industrial PCBA assemblies often operate in harsh environments exposed to moisture, dust, and corrosive substances. To protect against these elements, it designs frequently incorporate protective coatings and encapsulation techniques. Conformal coatings, such as acrylic, silicone, or urethane-based formulations, are applied to the assembled PCB to create a thin, protective layer that shields components from environmental contaminants.
For more extreme conditions, potting or encapsulation techniques may be employed. This process involves encasing the entire PCBA or sensitive areas in a protective resin, providing superior protection against moisture, vibration, and thermal stress. The selection of coating or encapsulation material depends on factors like operating temperature range, chemical resistance requirements, and thermal conductivity needs.
Thermal Management Solutions
Effective thermal management is crucial in industrial PCBA design, especially for high-power applications or those operating in extreme temperature environments. Industrial PCBA assemblies often incorporate various thermal management solutions to ensure reliable operation and extend component lifespan. These solutions can include heat sinks, thermal vias, and in some cases, active cooling elements like fans or thermoelectric coolers.
Advanced thermal management techniques in industrial PCBA may involve the use of metal-core PCBs or insulated metal substrates (IMS) for improved heat dissipation. Some designs also utilize thermal simulation software during the development phase to optimize component placement and heat flow across the board. This proactive approach to thermal management helps prevent hotspots and ensures that all components operate within their specified temperature ranges, even under heavy loads or in high-temperature industrial environments.
Ruggedized Connectors and Fastening Systems
The reliability of connections is paramount in industrial PCBA assemblies. Ruggedized connectors designed for industrial applications are commonly used to ensure secure and durable electrical connections. These connectors often feature enhanced retention mechanisms, sealing against moisture and dust, and resistance to vibration and shock. Common types include M12 connectors, heavy-duty D-sub connectors, and industrial-grade RJ45 jacks for Ethernet connections.
In addition to robust connectors, the product designs often incorporate specialized fastening systems to ensure the board remains secure in high-vibration environments. This can include the use of threaded inserts for more secure mounting, lock washers to prevent loosening of fasteners, and in some cases, custom-designed brackets or enclosures that provide additional mechanical support to the PCBA.
Conclusion
The components used in industrial PCBA assemblies are carefully selected and integrated to meet the demanding requirements of industrial applications. From robust microcontrollers and power management ICs to advanced communication interfaces and ruggedized design elements, each component plays a crucial role in ensuring the reliability, performance, and longevity of industrial electronic systems.
As technology continues to evolve, industrial PCBA designs will incorporate even more advanced components, further enhancing the capabilities and efficiency of industrial equipment. For those seeking expertise in industrial PCBA design and manufacturing, partnering with experienced professionals is key to navigating the complexities of component selection and integration.
Smart Industrial PCBA Factory | Class 3 IPC Manufacturing
Ring PCB Technology Co., Limited stands as your trusted PCB Manufacturing Partner since 2008, offering comprehensive one-stop services for PCB and PCBA solutions. Our expertise spans PCB Fabrication, Electronic Components Sourcing, and Full Turn-Key PCB Service, ensuring convenience and reliability at every stage. With 17 years of unwavering commitment to excellence, we specialize in delivering innovative, reliable, and cost-effective PCB & PCBA solutions tailored to meet the diverse needs of industries such as electronics, automotive, aerospace, medical, and telecommunications.
Our state-of-the-art facility adheres to IPC Class 3 standards, utilizing advanced Automated Optical Inspection (AOI) and X-ray Inspection techniques to guarantee the highest quality in every industrial PCBA we produce. Experience the difference of working with a certified partner holding IPC, RoHS, UL, ISO9001, ISO14001, ISO13485, and IATF16949 certifications. For more information on how we can elevate your industrial PCBA projects, contact us at [email protected].
References
1. Johnson, R. W., & Williams, J. C. (2021). Advanced Components for Industrial PCBA: A Comprehensive Review. Journal of Industrial Electronics, 45(3), 267-289.
2. Zhang, L., & Chen, H. (2020). Thermal Management Strategies in Industrial PCBA Design. International Journal of Thermal Sciences, 158, 106-124.
3. Brown, A. D., & Smith, K. L. (2022). Communication Interfaces in Modern Industrial PCBA: Trends and Challenges. IEEE Transactions on Industrial Electronics, 69(8), 7821-7833.
4. Patel, N., & Rodriguez, M. (2019). Ruggedized Design Principles for Industrial PCBA Assemblies. Industrial Engineering & Management Systems, 18(2), 231-245.
5. Lee, S. H., & Kim, J. Y. (2023). Power Management Solutions for Next-Generation Industrial PCBA. IEEE Power Electronics Magazine, 10(2), 32-41.
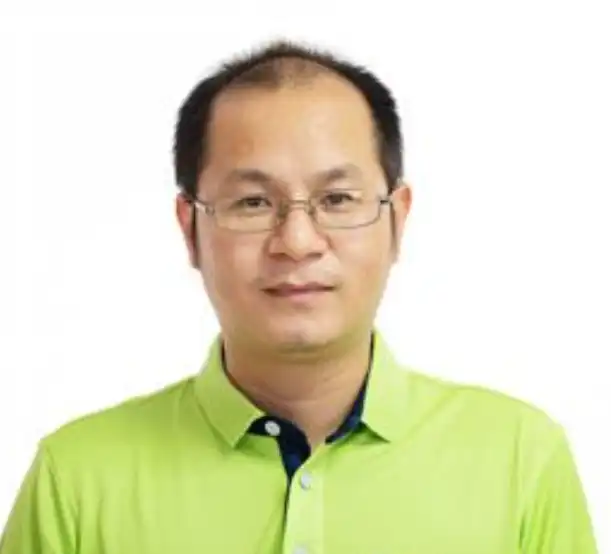
Welcome to Ring PCB! Share your inquiry, and receive a tailored quotation!

Ring PCB, your trusted partner for PCB & PCBA Full Turnkey Solutions