2 Layer PCB Stackup Guide for Power Applications
When it comes to power applications, a well-designed 2-layer PCB stackup is crucial for optimal performance and reliability, especially during the PCB Assembly process. The ideal stackup for power-focused designs typically consists of a top layer for power distribution and a bottom layer for ground planes. This configuration minimizes electromagnetic interference, reduces parasitic inductance, and enhances thermal management. By strategically placing copper pours and utilizing appropriate trace widths, designers can maximize current-carrying capacity while maintaining signal integrity during the PCB Assembly. Additionally, incorporating thermal vias and optimizing component placement further improves heat dissipation, ensuring the PCB can handle high power demands efficiently.
Key Considerations for 2 Layer PCB Stackup in Power Applications
Layer Allocation and Thickness
When designing a 2 layer PCB stackup for power applications, careful consideration of layer allocation and thickness is paramount. The top layer is typically dedicated to power distribution, while the bottom layer serves as a ground plane. This arrangement helps minimize electromagnetic interference and reduces parasitic inductance, which is crucial for maintaining signal integrity in high-power circuits.
Layer thickness plays a significant role in the PCB's current-carrying capacity and thermal management. For power applications, it's common to use thicker copper layers, such as 2 oz or 3 oz copper, to handle higher currents and improve heat dissipation. The increased copper thickness allows for wider traces and larger copper pours, which are essential for managing power distribution efficiently.
Copper Pour and Trace Design
Effective copper pour and trace design are crucial elements in optimizing a 2 layer PCB stackup for power applications. Large copper pours on both layers help to reduce resistance and improve current distribution across the board. On the power layer, strategic placement of copper pours ensures efficient power delivery to components, while on the ground layer, a solid ground plane provides a low-impedance return path for currents.
Trace width and spacing are critical factors in power PCB design. Wider traces are necessary to handle higher currents without excessive voltage drop or heating. It's essential to calculate the required trace width based on the expected current and acceptable temperature rise. Additionally, maintaining adequate spacing between traces helps prevent crosstalk and reduces the risk of voltage breakdown between high-power and low-power signals.
Thermal Management and Component Placement
Effective thermal management is a critical aspect of power PCB design, particularly in 2 layer configurations where heat dissipation options are more limited compared to multilayer boards. Strategic component placement plays a vital role in managing heat distribution across the PCB. High-power components should be placed with sufficient spacing to prevent thermal hotspots and allow for effective cooling.
Incorporating thermal vias is an effective technique for improving heat dissipation in 2 layer PCBs. These vias connect the top and bottom copper layers, creating a path for heat to spread more evenly across the board. Placing an array of thermal vias under power components significantly enhances their thermal performance. Additionally, using larger copper pads for power components and incorporating heat sinks where necessary can further improve the PCB's ability to manage high power loads.
Optimizing Power Integrity in 2 Layer PCB Designs
Decoupling and Bypass Capacitors
In power-focused 2-layer PCB designs, proper implementation of decoupling and bypass capacitors is crucial for maintaining power integrity, particularly during the PCB Assembly process. These capacitors help stabilize voltage levels, reduce noise, and provide localized charge storage for components with rapidly changing current demands. Placing decoupling capacitors close to power pins of ICs and other active components minimizes the loop area and reduces parasitic inductance, ensuring clean power delivery.
For optimal performance, it's recommended to use a combination of capacitor values. Smaller capacitors (e.g., 0.1 µF) handle high-frequency noise, while larger capacitors (e.g., 10 µF) provide bulk charge storage. The placement of these capacitors should be carefully considered to minimize the distance between the capacitor and the component it's supporting, thereby reducing the impedance of the power delivery network.
Power and Ground Plane Design
Effective power and ground plane design is essential for maintaining power integrity in 2 layer PCB stackups. The ground plane should be as continuous as possible to provide a low-impedance return path for currents and minimize ground bounce. Avoid creating large gaps or slots in the ground plane, as these can disrupt current flow and create areas of high impedance.
For the power plane, consider using a split plane design if multiple voltage domains are required. This approach involves dividing the power layer into separate regions for different voltage levels. When implementing split planes, it's crucial to maintain proper isolation between voltage domains and provide sufficient decoupling at the boundaries. Additionally, ensure that critical signal traces don't cross split plane boundaries to prevent signal integrity issues.
EMI Mitigation Techniques
Electromagnetic Interference (EMI) mitigation is a critical consideration in power PCB design, especially for 2 layer configurations where shielding options are limited. One effective technique is to implement guard traces around high-speed or sensitive signals. These traces, connected to the ground plane, help contain electromagnetic fields and reduce crosstalk between adjacent traces.
Another important EMI mitigation strategy is to minimize loop areas in both power and signal paths. Keeping signal traces close to their respective return paths (usually the ground plane) reduces the antenna effect and lowers electromagnetic emissions. For power circuits, placing decoupling capacitors close to ICs and routing power traces directly over the ground plane helps minimize loop areas and reduce EMI.
PCB Assembly Considerations for Power Applications
Component Selection and Placement
The PCB assembly process for power applications requires careful consideration of component selection and placement. Choose components rated for the expected current and voltage levels, with appropriate power dissipation capabilities. When selecting passive components like resistors and capacitors, opt for those with higher voltage ratings and lower ESR (Equivalent Series Resistance) to improve efficiency and reliability.
During the PCB assembly phase, component placement plays a crucial role in thermal management and electrical performance. Place high-power components with adequate spacing to allow for proper heat dissipation. Consider the direction of heat flow and position components to facilitate natural convection cooling. Additionally, keep sensitive components away from high-power areas to minimize electromagnetic interference and thermal stress.
Soldering and Thermal Considerations
The soldering process in PCB assembly for power applications requires special attention due to the higher thermal demands. Use of lead-free solder with appropriate melting points is essential for creating reliable connections capable of withstanding high currents and temperatures. For components with large thermal pads, such as power MOSFETs or voltage regulators, ensure proper solder coverage to maximize heat transfer to the PCB.
Thermal profiling during the reflow process is critical to prevent component damage and ensure proper solder joint formation. Power components often require longer dwell times at peak temperatures to ensure complete solder melting and proper wetting. However, care must be taken not to exceed the maximum temperature ratings of other components on the board. Implementing a staged reflow profile can help balance these requirements for optimal PCB assembly results.
Quality Control and Testing
Rigorous quality control and testing are essential steps in the PCB assembly process for power applications. Visual inspection using high-magnification microscopes can help identify solder joint defects, component misalignments, or other visible issues. X-ray inspection is particularly useful for checking solder connections under large power components or BGA devices.
Electrical testing is crucial to verify the functionality and performance of the assembled PCB. This includes continuity testing to check for short circuits or open connections, as well as functional testing under various load conditions. For power applications, thermal imaging during operation can help identify potential hotspots or areas of concern. Additionally, burn-in testing, where the PCB is operated under high-stress conditions for an extended period, can help identify any early-life failures or reliability issues before the product is deployed in the field.
Conclusion
Designing an optimized 2 layer PCB stackup for power applications requires careful consideration of various factors, including layer allocation, copper thickness, thermal management, and EMI mitigation. By implementing proper design techniques and following best practices in PCB assembly, engineers can create reliable and efficient power-focused PCBs. The key is to balance power distribution, signal integrity, and thermal performance within the constraints of a 2 layer design. As power requirements continue to evolve, staying updated with the latest PCB design and assembly techniques will be crucial for developing high-performance power electronics solutions.
Optimized 2-Layer Stack-Up for Power Loads | Ring PCB
Ring PCB Technology Co., Limited offers expert solutions for 2-layer PCB stack-ups optimized for power applications. With 17 years of experience, we provide comprehensive PCB and PCBA services, including fabrication, component sourcing, and full turn-key solutions. Our advanced capabilities in power PCB design, coupled with rigorous quality control measures, ensure reliable and efficient boards for your power-intensive projects. Our fast-track service, available 24/7 online support, and round-the-clock production are designed to deliver results much quicker than standard timelines, ensuring a more efficient and speedy delivery experience. For tailored solutions and superior PCB assembly services, contact us at [email protected].
References
1. Johnson, H. W., & Graham, M. (2003). High-speed digital design: a handbook of black magic. Prentice Hall PTR.
2. Montrose, M. I. (2000). Printed circuit board design techniques for EMC compliance: a handbook for designers. IEEE press.
3. Ritchey, L. W., & Zasio, J. J. (2003). Right the first time: a practical handbook on high-speed PCB and system design. Speeding Edge.
4. Brooks, D. (2003). Signal integrity issues and printed circuit board design. Prentice Hall Professional.
5. Bogatin, E. (2010). Signal and power integrity-simplified. Prentice Hall Press.
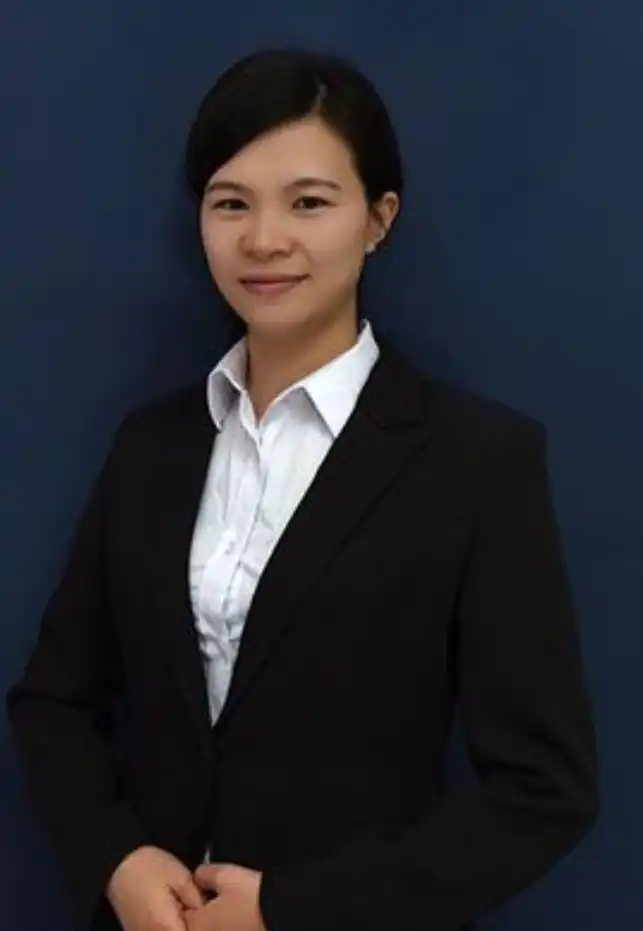
Welcome to Ring PCB! Share your inquiry, and receive a tailored quotation!

Ring PCB, your trusted partner for PCB & PCBA Full Turnkey Solutions