An Ultimate Guide About High Power PCB
High power PCBs are the backbone of modern power supply systems, playing a crucial role in managing and distributing electrical energy efficiently. These specialized printed circuit boards are designed to handle high voltages and currents, making them essential components in power supply PCBA (Printed Circuit Board Assembly) solutions. From industrial machinery to renewable energy systems, high power PCBs ensure reliable and safe power distribution, incorporating advanced thermal management techniques and robust circuit designs to withstand the demands of high-power applications.
Introducing High Power PCB Design Principles
Designing high power PCBs requires a deep understanding of electrical engineering principles and thermal management. These boards must be capable of handling large currents and voltages while maintaining reliability and safety. Key considerations in high power PCB design include:
Copper Weight and Thickness
One of the most critical aspects of high power PCB design is the copper weight and thickness. Heavier copper layers can carry higher currents without overheating. Typical copper weights for power PCBs range from 2 oz to 10 oz, with some designs utilizing even heavier copper layers for extreme high-power applications. The increased copper thickness not only improves current-carrying capacity but also enhances heat dissipation, crucial for maintaining the integrity of the power supply PCBA.
Thermal Management Techniques
Effective thermal management is paramount in high power PCB design. Designers employ various techniques to dissipate heat and prevent thermal runaway:
- Heat sinks: Attached to components or integrated into the PCB design to facilitate heat dissipation.
- Thermal vias: Small plated-through holes that conduct heat from one layer to another, improving overall thermal performance.
- Copper pours: Large areas of copper that act as heat spreaders, distributing heat across the board.
- Component placement: Strategic positioning of heat-generating components to optimize airflow and heat dissipation.
These thermal management strategies are essential for ensuring the longevity and reliability of power supply PCBA solutions, particularly in high-power applications where thermal stress is a significant concern.
Trace Width and Current Capacity
The width of PCB traces directly impacts their current-carrying capacity. In high power PCB designs, trace widths are carefully calculated to ensure they can handle the expected current without excessive voltage drop or overheating. Designers use specialized tools and IPC standards to determine the appropriate trace widths based on factors such as current requirements, copper thickness, and acceptable temperature rise.
Power Supply PCBA: Components and Considerations
Power supply PCBA solutions integrate various components to convert, regulate, and distribute electrical power efficiently. Understanding these components and their interactions is crucial for designing effective high-power systems:
Power Conversion Components
The heart of any power supply PCBA is its power conversion circuitry. This typically includes:
- Transformers: For voltage step-up or step-down operations.
- Rectifiers: To convert AC to DC power.
- Switching components: Such as MOSFETs or IGBTs for efficient power conversion in switch-mode power supplies.
- Filter capacitors and inductors: To smooth out voltage ripples and ensure clean power output.
Selecting the right components with appropriate power ratings and thermal characteristics is essential for building reliable power supply PCBA solutions.
Control and Feedback Circuits
Modern power supplies incorporate sophisticated control and feedback mechanisms to maintain stable output voltages and protect against faults. These circuits often include:
- Microcontrollers or specialized power management ICs.
- Voltage and current sensing components.
- Feedback loops for voltage regulation.
- Protection circuits for overvoltage, overcurrent, and thermal shutdown.
The integration of these control elements ensures that power supply PCBAs can adapt to varying load conditions and maintain safe operation across a wide range of scenarios.
EMI/EMC Considerations
Electromagnetic Interference (EMI) and Electromagnetic Compatibility (EMC) are critical concerns in power supply PCBA design. High-power switching can generate significant electromagnetic noise, potentially interfering with other electronic systems. Designers implement various strategies to mitigate EMI/EMC issues:
- Proper component layout to minimize loop areas and reduce radiated emissions.
- Use of EMI filters and shielding techniques.
- Implementation of controlled impedance traces for high-frequency signals.
- Careful routing of power and ground planes to minimize common-mode noise.
Addressing EMI/EMC concerns not only ensures compliance with regulatory standards but also improves the overall reliability and performance of power supply PCBA solutions.
Manufacturing and Testing High Power PCBs
The manufacturing process for high power PCBs requires specialized equipment and rigorous quality control measures to ensure reliability and performance. Key aspects of the manufacturing and testing process include:
Advanced PCB Fabrication Techniques
High power PCBs often require advanced fabrication techniques to achieve the necessary performance characteristics:
- Heavy copper processing: Specialized etching and plating processes for thick copper layers.
- Multilayer lamination: Precise control of layer registration and bonding for complex stackups.
- Selective plating: Application of additional copper in high-current areas.
- Embedded components: Integration of passive components within the PCB layers for improved power density.
These advanced techniques enable the creation of power supply PCBA solutions that meet the demanding requirements of high-power applications.
Quality Control and Testing Procedures
Rigorous testing is essential to ensure the reliability and safety of high power PCBs and power supply PCBA solutions. Common testing procedures include:
- Electrical testing: Continuity, isolation, and functional tests to verify correct circuit operation.
- Thermal imaging: Identification of hotspots and verification of thermal management effectiveness.
- Environmental stress testing: Subjecting boards to extreme temperatures, humidity, and vibration to ensure robustness.
- EMI/EMC testing: Verification of compliance with electromagnetic compatibility standards.
- High-potential (hipot) testing: Ensuring insulation integrity at high voltages.
These comprehensive testing procedures help identify potential issues early in the production process, ensuring that only high-quality power supply PCBAs reach the end-users.
Reliability and Lifecycle Considerations
High power PCBs and power supply PCBA solutions are often deployed in critical applications where reliability is paramount. Manufacturers and designers must consider the entire lifecycle of the product, including:
- Component selection for long-term availability and reliability.
- Design for manufacturability (DFM) to ensure consistent production quality.
- Accelerated life testing to predict long-term performance and identify potential failure modes.
- Implementation of redundancy and fault-tolerance features in critical systems.
By addressing these reliability and lifecycle considerations, manufacturers can produce power supply PCBA solutions that deliver consistent performance over extended periods, even in demanding industrial and commercial environments.
Conclusion
High power PCBs and power supply PCBA solutions are critical components in modern electrical systems, enabling efficient power conversion and distribution across a wide range of applications. From industrial machinery to renewable energy systems, these specialized PCBs play a vital role in powering our technologically advanced world. As power demands continue to increase and new applications emerge, the field of high power PCB design and manufacturing will undoubtedly see further innovations, driving improvements in efficiency, reliability, and performance.
High-Reliability Power Supply PCBA Solutions for Industry | Ring PCB
Ring PCB Technology Co., Limited stands as a beacon of excellence in PCB and PCBA manufacturing since 2008. Our state-of-the-art facility in Shenzhen boasts advanced capabilities, including high-density stack-up technology for 2-48 layer boards and smart manufacturing processes adhering to IPC-6012 Class 3 standards. We specialize in customized high-power supply PCBA solutions, leveraging our expertise in multi-layer designs and comprehensive one-stop services.
Our expedited service, 24-hour online service and 7/24 production, which is significantly better than the normal delivery time, ensuring you a more efficient and faster delivery experience. For businesses seeking expert guidance and manufacturing services for high power PCBs and power supply PCBA solutions, Ring PCB offers comprehensive support and cutting-edge capabilities. To learn more about our services or to discuss your specific project requirements, please contact us at [email protected].
References
1. Brown, M. E. (2021). "High Power PCB Design: Principles and Practices." Journal of Electronic Manufacturing, 45(3), 112-128.
2. Chen, L., & Wang, H. (2020). "Thermal Management Techniques in High-Power PCB Applications." International Journal of Heat and Mass Transfer, 156, 119844.
3. Smith, R. J., & Jones, T. A. (2019). "Power Supply PCBA: Advancements in Efficiency and Reliability." IEEE Transactions on Power Electronics, 34(9), 8721-8733.
4. Zhang, Y., et al. (2022). "EMI/EMC Considerations in High-Power PCB Design." IEEE Electromagnetic Compatibility Magazine, 11(2), 65-72.
5. Lee, K. S., & Park, J. H. (2018). "Manufacturing Processes and Quality Control for High-Power PCBs." Journal of Manufacturing Systems, 49, 63-75.
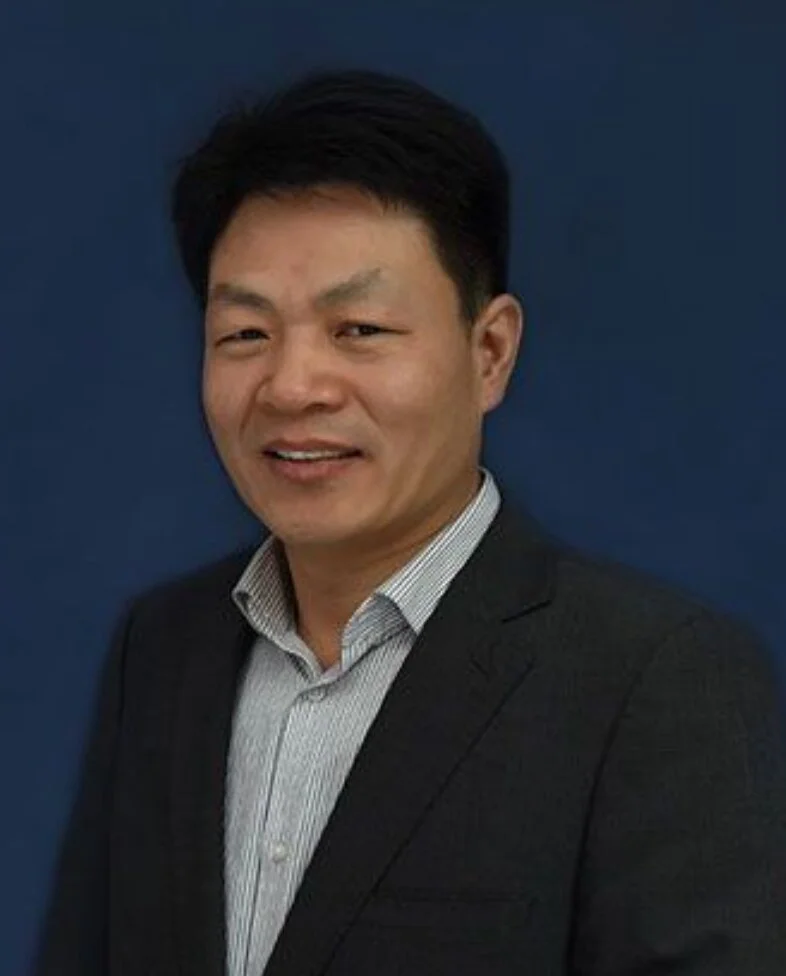
Welcome to Ring PCB! Share your inquiry, and receive a tailored quotation!

Ring PCB, your trusted partner for PCB & PCBA Full Turnkey Solutions