Avoid These Power Supply PCBA Mistakes
Power supply PCBAs (Printed Circuit Board Assemblies) are critical components in electronic devices, responsible for converting and distributing electrical power. However, designing and manufacturing these intricate assemblies can be fraught with potential pitfalls. Common mistakes in power supply PCBA development can lead to inefficiency, overheating, electromagnetic interference, and even device failure. By understanding and avoiding these errors, engineers and manufacturers can ensure the reliability, safety, and performance of their power supply systems. This article will explore key mistakes to avoid in power supply PCBA design and production, offering insights to help you optimize your next project.
Overlooking Thermal Management in Power Supply PCBA Design
Effective thermal management is crucial for the longevity and performance of power supply PCBAs. Heat generation is an inevitable byproduct of power conversion, and failing to address it adequately can lead to component failure, reduced efficiency, and shortened lifespan of the entire assembly.
Inadequate Heat Dissipation Strategies
One of the most common mistakes in power supply PCBA design is underestimating the importance of heat dissipation. High-power components such as MOSFETs, diodes, and transformers generate significant heat during operation. Without proper thermal management, these components can exceed their maximum operating temperatures, leading to degraded performance or failure.
To avoid this mistake, implement robust heat dissipation strategies:
- Use thermal vias to conduct heat away from critical components
- Incorporate heat sinks or cooling fans for high-power devices
- Optimize component placement to improve airflow and heat distribution
- Consider using thermally conductive materials for improved heat transfer
Ignoring Thermal Simulations
Another oversight is neglecting to perform thermal simulations during the design phase. Thermal analysis tools can provide valuable insights into heat distribution and potential hotspots on the PCBA. By simulating various operating conditions, designers can identify and address thermal issues before moving to production.
Incorporate thermal simulations into your design process to:
- Identify potential thermal bottlenecks
- Optimize component placement for better heat dissipation
- Validate cooling solutions before prototyping
- Ensure compliance with thermal specifications
Underestimating Electromagnetic Interference (EMI) in Power Supply PCBAs
Electromagnetic interference is a significant concern in power supply PCBAs, as these assemblies often handle high currents and voltages at varying frequencies. Failing to address EMI can result in poor performance, regulatory non-compliance, and interference with other electronic systems.
Neglecting Proper EMI Shielding
A common mistake is inadequate EMI shielding in power supply PCBAs. Without proper shielding, electromagnetic emissions from high-frequency switching components can cause interference both within the assembly and to nearby electronic devices.
To mitigate EMI issues, consider the following shielding techniques:
- Use EMI suppression components such as ferrite beads and common-mode chokes
- Implement ground planes and power planes to minimize current loops
- Apply EMI shielding materials to sensitive areas of the PCBA
Design PCB layouts with EMI reduction in mind, such as minimizing trace lengths and using proper component orientation
Overlooking EMC Testing and Compliance
Another critical mistake is failing to conduct thorough Electromagnetic Compatibility (EMC) testing or neglecting regulatory compliance requirements. Power supply PCBAs must often meet stringent EMC standards to be used in various applications and markets.
To ensure EMC compliance:
- Conduct pre-compliance EMC testing during the design phase
- Familiarize yourself with relevant EMC standards for your target markets
- Design with EMC compliance in mind from the outset
- Allocate time and resources for formal EMC testing and certification
Compromising on Component Selection and Layout in Power Supply PCBAs
The selection and arrangement of components on a power supply PCBA play a crucial role in its performance, reliability, and manufacturability. Cutting corners in these areas can lead to suboptimal results and potential failures.
Using Subpar or Incompatible Components
One of the most detrimental mistakes in power supply PCBA design is choosing components based solely on cost without considering their quality, compatibility, or long-term reliability. This can lead to premature failures, inconsistent performance, and increased maintenance costs.
To avoid component-related issues:
- Select components from reputable manufacturers with proven track records
- Ensure all components are rated for the expected voltage, current, and temperature conditions
- Consider the long-term availability of components to avoid future supply chain issues
- Verify component compatibility with other parts in the assembly
Poor Component Layout and Routing
Inefficient component placement and PCB routing can lead to various problems, including increased EMI, reduced thermal performance, and difficulty in assembly and testing. A well-designed layout is essential for optimal power supply PCBA performance.
To improve your PCBA layout:
- Group related components logically to minimize trace lengths and improve signal integrity
- Separate high-power and low-power sections of the PCBA to reduce interference
- Use proper trace widths and copper weights for high-current paths
- Consider the assembly process when placing components to facilitate automated manufacturing
Conclusion
Avoiding common mistakes in power supply PCBA design and manufacturing is crucial for creating reliable, efficient, and compliant power systems. By addressing thermal management, EMI considerations, and component selection and layout, engineers and manufacturers can significantly improve the quality and performance of their power supply PCBAs. Remember that successful PCBA development often requires a holistic approach, considering not only electrical performance but also thermal, electromagnetic, and mechanical aspects. By learning from these common pitfalls and implementing best practices, you can create power supply PCBAs that meet the demanding requirements of modern electronic devices.
Fast-Turn Power Supply PCBA with In-House SMT Assembly | Ring PCB
Ring PCB offers comprehensive one-stop solutions for power supply PCBAs, combining expert design optimization, advanced manufacturing capabilities, and rigorous quality control. Our Shenzhen facility features state-of-the-art SMT lines and testing equipment, enabling us to deliver high-quality, customized power supply PCBAs with rapid turnaround times. From multi-layer designs to complex power management systems, we provide tailored solutions to meet your specific requirements.
Experience the difference of working with a trusted partner in power supply PCBA manufacturing. Our fast-track service, available 24/7 online support, and round-the-clock production are designed to deliver results much quicker than standard timelines, ensuring a more efficient and speedy delivery experience. Contact us at [email protected] to power your next project.
References
1. Johnson, M. (2022). "Thermal Management Strategies for High-Power PCBAs". Power Electronics Design Journal, 18(3), 45-52.
2. Zhang, L., & Smith, K. (2021). "EMI Reduction Techniques in Switch-Mode Power Supplies". IEEE Transactions on Electromagnetic Compatibility, 63(4), 1122-1135.
3. Brown, R. (2023). "Component Selection Criteria for Reliable Power Supply PCBAs". Electronic Design, 71(5), 28-35.
4. Garcia, A., & Lee, S. (2022). "Layout Optimization for Power Supply PCB Assemblies". Journal of Power Electronics, 22(2), 189-201.
5. Wilson, T. (2023). "Common Pitfalls in Power Supply PCBA Design and Manufacturing". Power Systems Engineering, 29(1), 76-84.
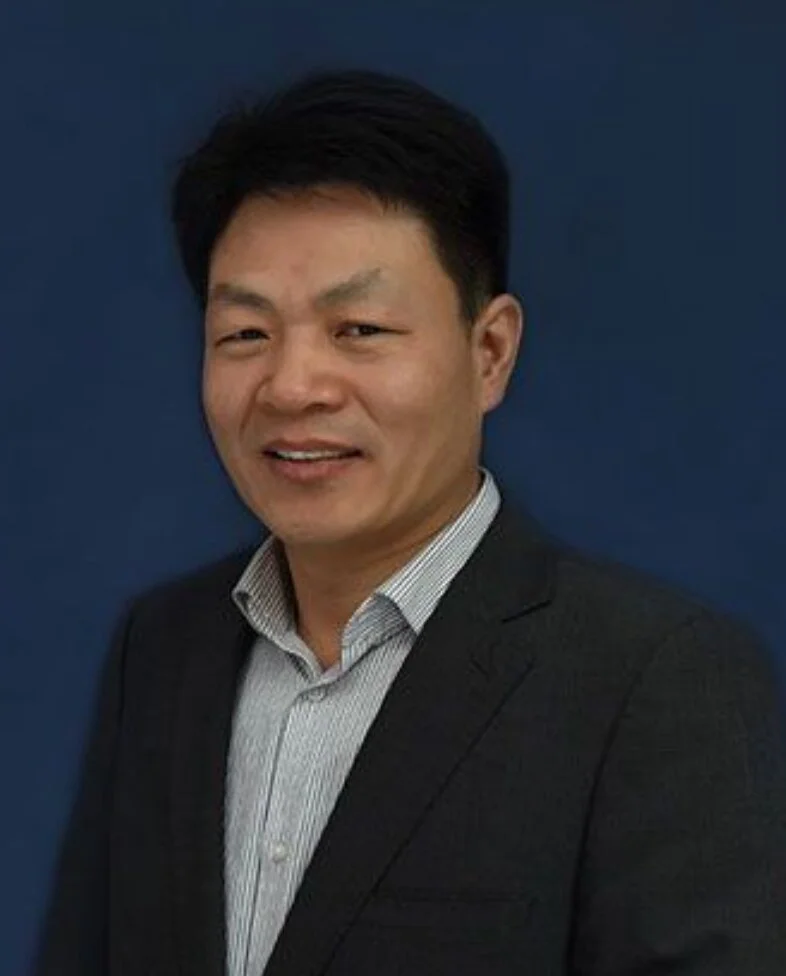
Welcome to Ring PCB! Share your inquiry, and receive a tailored quotation!

Ring PCB, your trusted partner for PCB & PCBA Full Turnkey Solutions