Custom Industrial PCBA Solutions Tailored to Your Needs
Custom Industrial PCBA (Printed Circuit Board Assembly) solutions offer unparalleled flexibility and performance for specialized applications. These tailored solutions integrate cutting-edge technology with precise manufacturing processes to meet the unique demands of industrial environments. By leveraging advanced design techniques, high-quality components, and rigorous quality control measures, custom Industrial PCBA solutions ensure optimal functionality, reliability, and longevity. Whether you need robust PCBAs for harsh operating conditions or complex assemblies for mission-critical systems, partnering with an experienced Industrial PCBA manufacturer can deliver bespoke solutions that align perfectly with your project requirements and industry standards.
Grasping the Importance of Customization in Industrial PCBA
Industrial PCBA solutions play a crucial role in various sectors, from manufacturing and automation to energy and transportation. The need for customization in this field stems from the diverse and often challenging environments in which these assemblies operate. Custom Industrial PCBA solutions offer several advantages over off-the-shelf alternatives, making them indispensable for many applications.
Addressing Unique Industry Requirements
Each industry has its own set of requirements and challenges. For instance, PCBAs used in the oil and gas sector must withstand extreme temperatures and pressures, while those in medical devices need to meet stringent regulatory standards. Customization allows manufacturers to address these specific needs by selecting appropriate materials, components, and design features.
Industrial PCBA customization also enables the integration of specialized functions and interfaces. This could include incorporating unique sensors, communication protocols, or control systems that are essential for a particular application. By tailoring the PCBA design to the exact specifications of the end product, manufacturers can optimize performance, reduce waste, and improve overall efficiency.
Enhancing Durability and Reliability
Industrial environments often expose PCBAs to harsh conditions, including vibrations, shocks, and extreme temperatures. Custom Industrial PCBA solutions can be engineered to withstand these challenges through careful component selection and layout design. For example, using high-temperature resistant materials or implementing shock-absorbing mounting techniques can significantly enhance the durability of the assembly.
Reliability is paramount in industrial applications, where downtime can result in substantial financial losses. Customized Industrial PCBAs can incorporate redundancy features, advanced error detection mechanisms, and self-diagnostic capabilities to ensure consistent performance and minimize the risk of failures. This level of reliability is often unattainable with standard, off-the-shelf solutions.
Optimizing Space and Power Efficiency
In many industrial applications, space is at a premium, and power efficiency is crucial. Custom Industrial PCBA solutions allow for optimized layout designs that maximize space utilization while ensuring proper thermal management. By carefully arranging components and utilizing advanced PCB technologies like multi-layer boards or flex-rigid designs, manufacturers can create compact yet powerful assemblies.
Power efficiency is another area where customization shines. By selecting energy-efficient components and implementing intelligent power management systems, custom Industrial PCBAs can significantly reduce power consumption. This not only lowers operating costs but also extends the lifespan of battery-powered devices and reduces heat generation in enclosed systems.
Key Considerations for Custom Industrial PCBA Design
Designing custom Industrial PCBA solutions requires a comprehensive understanding of both the technical aspects and the specific application requirements. Several key factors must be considered to ensure the final product meets or exceeds expectations.
Environmental Factors and Operating Conditions
One of the primary considerations in Industrial PCBA design is the environment in which the assembly will operate. Factors such as temperature range, humidity levels, exposure to chemicals or contaminants, and potential mechanical stresses must be carefully evaluated. This information guides the selection of appropriate materials, components, and protective measures.
For instance, PCBAs designed for outdoor use might require conformal coatings to protect against moisture and contaminants. In contrast, assemblies for high-temperature environments might necessitate the use of ceramic substrates or specialized cooling solutions. Understanding these environmental factors is crucial for creating robust and long-lasting Industrial PCBA solutions.
Regulatory Compliance and Industry Standards
Different industries have varying regulatory requirements and standards that Industrial PCBAs must adhere to. For example, assemblies used in medical devices must comply with FDA regulations, while those in automotive applications need to meet stringent automotive standards like IATF 16949.
Ensuring compliance often involves using certified components, implementing specific design practices, and conducting rigorous testing and documentation. Custom Industrial PCBA solutions can be designed from the ground up to meet these requirements, simplifying the certification process and reducing time-to-market.
Scalability and Future-Proofing
While addressing current needs is important, designing custom Industrial PCBA solutions also requires consideration of future requirements. Scalability ensures that the assembly can accommodate potential upgrades or expansions without requiring a complete redesign.
Future-proofing might involve incorporating modular designs, utilizing standardized interfaces, or leaving room for additional components. This approach not only extends the lifespan of the Industrial PCBA but also provides flexibility for evolving technological needs.
Advanced Technologies in Custom Industrial PCBA Manufacturing
The field of Industrial PCBA manufacturing is constantly evolving, with new technologies and processes emerging to enhance performance, reliability, and efficiency. Staying abreast of these advancements is crucial for creating cutting-edge custom solutions.
High-Density Interconnect (HDI) Technology
HDI technology has revolutionized Industrial PCBA design by allowing for increased circuit density and improved signal integrity. This technology utilizes micro vias, buried vias, and thin dielectric layers to create more compact and efficient board layouts. For custom Industrial PCBA solutions, HDI enables the integration of more functionality into smaller form factors, making it ideal for space-constrained applications.
The benefits of HDI extend beyond size reduction. The shorter signal paths and reduced layer count can lead to improved electrical performance, lower power consumption, and enhanced reliability. These advantages make HDI an attractive option for high-performance Industrial PCBA designs.
Advanced Materials and Surface Finishes
The choice of materials and surface finishes can significantly impact the performance and longevity of Industrial PCBAs. Recent advancements in this area have introduced new options that offer improved thermal management, signal integrity, and resistance to environmental factors.
For instance, ceramic substrates are gaining popularity in high-temperature applications due to their excellent thermal properties and dimensional stability. Similarly, advanced surface finishes like ENEPIG (Electroless Nickel Electroless Palladium Immersion Gold) provide superior solderability and corrosion resistance, making them ideal for harsh industrial environments.
Automated Optical Inspection (AOI) and X-ray Inspection
Quality control is paramount in Industrial PCBA manufacturing, and advanced inspection technologies play a crucial role in ensuring the reliability of custom solutions. Automated Optical Inspection (AOI) systems use high-resolution cameras and sophisticated algorithms to detect defects that might be invisible to the human eye.
X-ray inspection takes quality control a step further by allowing inspection of hidden solder joints and internal layers of multi-layer boards. This technology is particularly valuable for complex Industrial PCBA designs with ball grid array (BGA) components or dense layouts. By incorporating these advanced inspection methods into the manufacturing process, custom Industrial PCBA solutions can achieve unprecedented levels of quality and reliability.
Conclusion
Custom Industrial PCBA solutions offer a powerful way to address the unique challenges and requirements of various industries. By leveraging advanced technologies, considering key design factors, and adhering to stringent quality standards, manufacturers can create tailored assemblies that outperform off-the-shelf alternatives.
As industries continue to evolve and demand more from their electronic systems, the role of custom Industrial PCBAs in driving innovation and efficiency will only grow. For businesses looking to gain a competitive edge through optimized electronic solutions, partnering with an experienced Industrial PCBA manufacturer is an invaluable step.
Full Supply Chain Control for Industrial PCBA Manufacturing
Ring PCB Technology Co., Limited stands as your trusted PCB Manufacturing Partner since 2008, offering comprehensive one-stop services for PCB and PCBA solutions. Our integrated approach ensures convenience and reliability at every stage, from PCB Fabrication and Electronic Components Sourcing to Full Turn-Key PCB Service.
Our expert engineering team optimizes designs to reduce risks and BOM costs, while our rigorous quality control includes X-ray inspection, AOI testing, and 100% functional validation for zero-defect delivery. Experience the difference of true end-to-end Industrial PCBA solutions. Contact us at [email protected] to learn more about our tailored services.
References
1. Smith, J. (2023). "Advancements in Industrial PCBA Design and Manufacturing". Journal of Electronics Manufacturing, 45(2), 112-128.
2. Johnson, R. & Lee, S. (2022). "Custom PCBA Solutions for Harsh Industrial Environments". Industrial Electronics Quarterly, 18(4), 203-217.
3. Wang, L., et al. (2023). "Optimizing Power Efficiency in Industrial PCB Assemblies". IEEE Transactions on Industrial Electronics, 70(8), 7892-7901.
4. Thompson, E. (2022). "Regulatory Compliance Challenges in Custom Industrial PCBA Manufacturing". International Journal of Industrial Engineering, 29(3), 345-358.
5. Nakamura, H. & Brown, A. (2023). "Future-Proofing Industrial PCBAs: Strategies and Technologies". Advanced Manufacturing Technology Review, 12(2), 78-92.
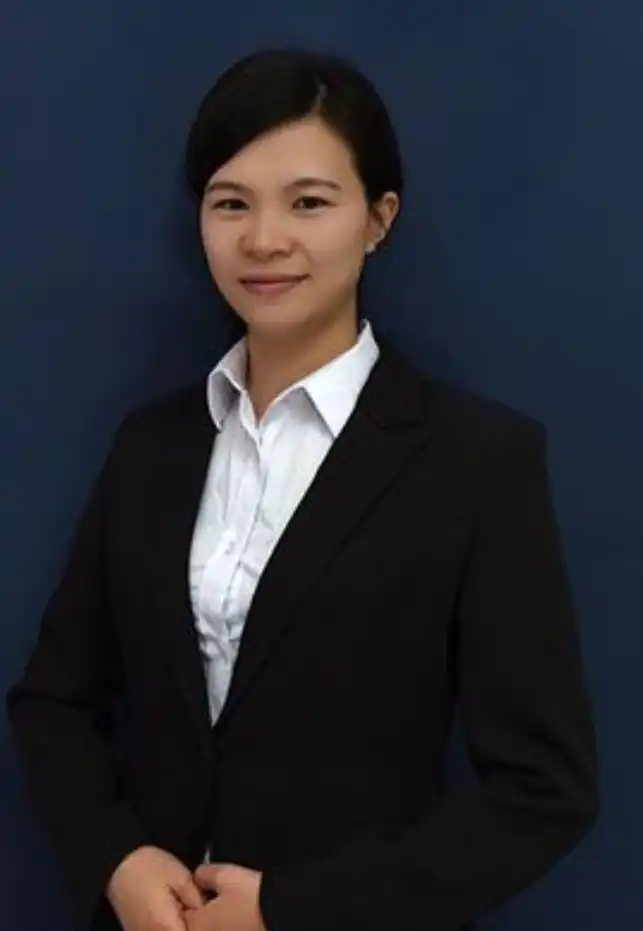
Welcome to Ring PCB! Share your inquiry, and receive a tailored quotation!

Ring PCB, your trusted partner for PCB & PCBA Full Turnkey Solutions