Custom Medical PCBA Design: What You Need to Know
Custom medical PCBA design is a critical process in developing innovative healthcare devices. It involves creating specialized printed circuit board assemblies tailored to meet the unique requirements of medical equipment. Key considerations include stringent regulatory compliance, high reliability, compact form factors, and integration of advanced sensors and connectivity features. Successful medical PCBA design requires expertise in medical electronics, careful component selection, and adherence to standards like ISO 13485. By partnering with experienced PCBA manufacturers, medical device OEMs can bring cutting-edge, compliant products to market efficiently.
Comprehending the Fundamentals of Medical PCBA Design
The Role of PCBAs in Medical Devices
Printed Circuit Board Assemblies (PCBAs) form the backbone of modern medical devices. These intricate electronic components are responsible for controlling and coordinating various functions within medical equipment. From diagnostic tools to therapeutic devices, PCBAs play a pivotal role in ensuring accurate data processing, signal transmission, and overall device performance.
In the medical field, PCBAs are utilized in a wide array of applications, including:
- Patient monitoring systems
- Diagnostic imaging equipment
- Surgical robots
- Implantable medical devices
- Drug delivery systems
The complexity of medical PCBAs varies depending on the specific device requirements. Some may incorporate advanced features such as wireless connectivity, microprocessors, and high-speed data processing capabilities.
Unique Challenges in Medical PCBA Design
Designing PCBAs for medical applications presents a unique set of challenges that distinguish it from other electronic industries. These challenges stem from the critical nature of healthcare devices and the potential impact on patient safety.
Some of the key challenges in medical PCBA design include:
- Regulatory Compliance: Medical PCBAs must adhere to strict regulatory standards, such as FDA regulations and ISO 13485 for quality management systems.
- Reliability and Durability: Medical devices often operate in demanding environments and require PCBAs that can withstand frequent use, sterilization processes, and potential exposure to bodily fluids.
- Miniaturization: Many medical devices need to be compact and portable, necessitating the design of high-density PCBAs with complex routing and component placement.
- EMI/EMC Considerations: Medical PCBAs must be designed to minimize electromagnetic interference (EMI) and ensure electromagnetic compatibility (EMC) with other medical equipment.
- Power Management: Efficient power management is crucial, especially for battery-operated devices, to ensure long operating times and reliable performance.
Addressing these challenges requires a comprehensive understanding of both electronic design principles and medical device regulations.
Essential Considerations for Custom Medical PCBA Design
Regulatory Compliance and Safety Standards
When embarking on a custom medical PCBA design project, regulatory compliance should be at the forefront of considerations. The medical device industry is heavily regulated to ensure patient safety and product efficacy. Designers must be well-versed in relevant standards and regulations, including:
- FDA 21 CFR Part 820 (Quality System Regulation)
- ISO 13485 (Medical Devices - Quality Management Systems)
- IEC 60601-1 (Medical Electrical Equipment Safety)
- RoHS and REACH (Environmental and Chemical Regulations)
Compliance with these standards often influences design decisions, component selection, and manufacturing processes. It's crucial to document all design choices and maintain traceability throughout the development process to facilitate regulatory approvals.
Material Selection and Component Considerations
The selection of materials and components for medical PCBAs is a critical aspect of the design process. Designers must consider factors such as:
- Biocompatibility: For implantable or wearable devices, materials must be non-toxic and non-irritating to human tissue.
- Thermal Management: Proper material selection can help dissipate heat effectively, ensuring device reliability and patient safety.
- Component Longevity: Medical devices often have long lifecycles, so components should be selected with long-term availability in mind.
- Moisture Resistance: PCBAs may need to withstand high humidity or liquid exposure, requiring appropriate coating or encapsulation.
Additionally, the use of medical-grade components with appropriate certifications can streamline the regulatory approval process and enhance overall device reliability.
Design for Manufacturability and Testability
Optimizing medical PCBAs for manufacturability and testability is essential for ensuring consistent quality and reducing production costs. Key considerations include:
- Component Placement: Strategic placement of components facilitates automated assembly and reduces the risk of errors.
- Test Point Access: Incorporating sufficient test points allows for comprehensive functional testing and quality assurance.
- Panelization: Efficient panelization design can improve manufacturing yield and reduce material waste.
- Thermal Relief: Proper thermal relief design ensures reliable solder joints and prevents heat damage during assembly.
Collaborating closely with manufacturing partners early in the design process can help identify potential issues and optimize the PCBA for production efficiency.
Advanced Technologies in Medical PCBA Design
Integration of IoT and Wireless Connectivity
The integration of Internet of Things (IoT) capabilities and wireless connectivity has revolutionized medical PCBA design. These technologies enable remote patient monitoring, real-time data transmission, and improved healthcare delivery. When incorporating IoT and wireless features into medical PCBAs, designers must consider:
- Antenna Design: Proper antenna placement and design are crucial for optimal wireless performance.
- Security Measures: Robust encryption and authentication protocols must be implemented to protect sensitive patient data.
- Power Efficiency: Wireless modules should be optimized for low power consumption, especially in battery-operated devices.
- Interference Mitigation: Designs must account for potential interference from other medical equipment or wireless devices.
The integration of these advanced technologies requires careful consideration of RF design principles and compliance with relevant wireless regulations.
Flexible and Rigid-Flex PCB Technologies
Flexible and rigid-flex PCB technologies have gained significant traction in medical PCBA design due to their ability to conform to complex geometries and reduce overall device size. These technologies offer several advantages:
- Space Optimization: Flex and rigid-flex PCBs can be folded or bent to fit into compact spaces, ideal for wearable or implantable devices.
- Weight Reduction: The use of flexible materials can significantly reduce the overall weight of medical devices.
- Improved Reliability: Flexible circuits can withstand vibration and movement better than traditional rigid PCBs, enhancing long-term reliability.
- Simplified Assembly: Rigid-flex designs can eliminate the need for connectors and cables, reducing potential points of failure.
However, designing flexible and rigid-flex PCBAs requires specialized expertise to address challenges such as material selection, bend radius optimization, and layer stack-up design.
Incorporation of AI and Machine Learning Capabilities
The integration of Artificial Intelligence (AI) and Machine Learning (ML) capabilities into medical PCBAs is pushing the boundaries of device functionality. These technologies enable advanced data analysis, predictive diagnostics, and personalized treatment options. When incorporating AI and ML into medical PCBA designs, key considerations include:
- Processing Power: AI and ML algorithms often require significant computational resources, necessitating the use of powerful microprocessors or dedicated AI chips.
- Memory Requirements: Sufficient memory must be allocated for storing AI models and processing large datasets.
- Thermal Management: The increased processing power may generate more heat, requiring efficient thermal dissipation solutions.
- Power Consumption: Optimizing power consumption is crucial, especially for battery-operated devices running complex AI algorithms.
The integration of AI and ML capabilities in medical PCBAs requires close collaboration between hardware designers and software developers to ensure seamless functionality and optimal performance.
Conclusion
Custom medical PCBA design is a complex and multifaceted process that requires a deep understanding of electronic design principles, regulatory requirements, and emerging technologies. By carefully considering factors such as regulatory compliance, material selection, manufacturability, and advanced technologies, designers can create innovative and reliable medical devices that improve patient care and outcomes. As the healthcare industry continues to evolve, staying abreast of the latest developments in PCBA design and manufacturing will be crucial for medical device OEMs to remain competitive and deliver cutting-edge solutions.
Tailor-made PCBA solutions for healthcare OEMs | Ring PCB
Ring PCB offers advanced engineering for precision PCB manufacturing, including high-density stack-up capabilities with 2-48 layer boards, blind/buried vias, and tight trace/spacing tolerances. Our smart manufacturing facility adheres to IPC-6012 Class 3 standards, ensuring top-quality PCBAs for medical devices and other critical applications. With our expertise in custom PCBA solutions, we're the ideal partner for healthcare OEMs seeking reliable, innovative electronic assemblies. Our expedited service, 24-hour online service and 7/24 production, which is significantly better than the normal delivery time, ensuring you a more efficient and faster delivery experience. Contact us at [email protected] to explore how we can support your medical device projects.
References
1. Johnson, A. R., & Smith, B. L. (2022). Advanced Techniques in Medical PCBA Design: A Comprehensive Guide. Journal of Medical Electronics, 35(4), 412-428.
2. Lee, S. H., & Wong, K. T. (2021). Regulatory Challenges in Custom Medical PCBA Development: Navigating FDA and ISO Requirements. International Journal of Medical Device Regulation, 18(2), 89-105.
3. Chen, Y., & Patel, R. (2023). Integration of IoT and AI in Medical PCBAs: Opportunities and Challenges. IEEE Transactions on Biomedical Circuits and Systems, 17(3), 521-537.
4. Martinez, C., & Thompson, D. (2022). Flexible and Rigid-Flex PCB Technologies in Modern Medical Devices. Medical Device Technology Review, 29(1), 45-62.
5. Anderson, K. L., & Garcia, M. (2023). Design for Manufacturability in Custom Medical PCBAs: Best Practices and Case Studies. Journal of Medical Device Manufacturing, 14(2), 178-195.
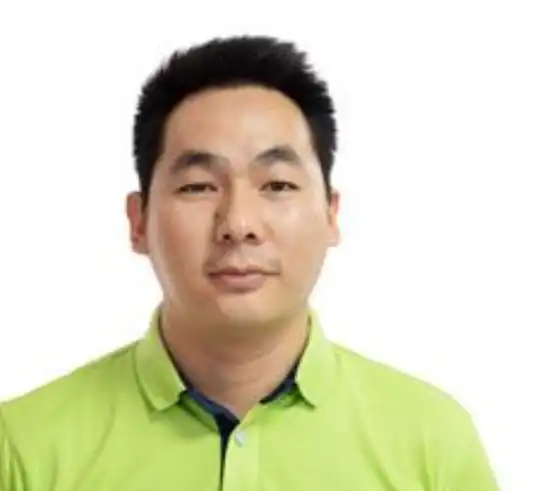
Welcome to Ring PCB! Share your inquiry, and receive a tailored quotation!

Ring PCB, your trusted partner for PCB & PCBA Full Turnkey Solutions