Industrial Control PCB Manufacturing and Assembly
Industrial Control PCB Assembly and Manufacturing is a basic process in the creation of electronic frameworks that oversee and control mechanical forms. This specialized field combines accuracy in designing with advanced manufacturing methods to deliver solid, high-performance printed circuit boards (PCBs) tailored for mechanical applications. These PCBs act as the backbone for control systems in factories, power plants, and other industrial environments, connecting different parts to enable automated operations, data collection, and process monitoring. The gathering process includes fastidious component arrangement, soldering, and quality control measures to guarantee strength and usefulness in cruel mechanical situations.
The Fundamentals of Industrial Control PCB Design
Industrial control PCB design is a complex process that requires careful consideration of various factors to ensure optimal performance and reliability. Let's delve into some key aspects of designing PCBs for industrial control applications:
Component Selection and Layout
Choosing the right components is pivotal in industrial control PCB assembly. Engineers must select components that can withstand unforgiving natural conditions, including extraordinary temperatures, vibrations, and electromagnetic impedances. The format of these components on the PCB is similarly vital, as it influences flag judgment, warm administration, and general framework execution.
When designing the PCB layout, engineers must consider:
- Signal path optimization to minimize interference and maintain signal integrity
- Proper grounding and power distribution to ensure stable operation
- Thermal management to prevent overheating of critical components
- Component spacing to facilitate assembly and maintenance
Material Selection
The choice of PCB materials plays a significant role in the board's performance and durability. For industrial control applications, materials must be selected based on their electrical properties, thermal characteristics, and mechanical strength. Common materials used in industrial PCBs include:
- FR-4: A flame-retardant fiberglass-reinforced epoxy laminate, known for its excellent electrical insulation properties
- Polyimide: Offers high temperature resistance and flexibility, suitable for applications with extreme operating conditions
- PTFE (Teflon): Provides low dielectric constant and loss tangent, ideal for high-frequency applications
Regulatory Compliance
Industrial control PCBs must adhere to various industry standards and regulations to ensure safety and reliability. Some key standards include:
- IPC standards for PCB design and manufacturing
- UL certification for safety compliance
- RoHS and REACH regulations for environmental compliance
- ISO 9001 for quality management systems
Ensuring compliance with these standards is essential for the successful deployment of industrial control systems in various sectors.
Advanced Manufacturing Techniques in Industrial PCB Assembly
The assembly of industrial control PCBs requires advanced manufacturing techniques to achieve the necessary precision and reliability. Let's explore some of the key processes involved in modern PCB assembly:
Surface Mount Technology (SMT)
Surface Mount Technology has revolutionized PCB assembly, allowing for higher component density and improved performance. The SMT process involves:
- Solder paste application using stencil printing
- Precise component placement using pick-and-place machines
- Reflow soldering to create permanent connections
- SMT offers several advantages for industrial control PCBs, including:
- Reduced board size and weight
- Improved electrical performance due to shorter connection paths
- Enhanced reliability and resistance to mechanical stress
Through-Hole Technology
While SMT is prevalent, through-hole technology still plays a crucial role in industrial PCB assembly, especially for components that require stronger mechanical connections or have high power requirements. The through-hole assembly process involves:
- Drilling holes in the PCB
- Inserting component leads through the holes
- Soldering the leads on the opposite side of the board
- Through-hole technology is often used for:
- Large connectors and sockets
- High-power components that require better heat dissipation
- Components subject to mechanical stress
Automated Optical Inspection (AOI) and X-ray Inspection
Quality control is paramount in industrial control PCB assembly. Advanced inspection techniques ensure that every board meets the required specifications:
- AOI systems use high-resolution cameras and sophisticated algorithms to detect defects such as missing components, incorrect placements, and solder joint issues
- X-ray inspection allows for the examination of hidden solder joints, especially in ball grid array (BGA) components
These inspection methods help identify and rectify issues early in the manufacturing process, reducing the risk of field failures and improving overall product reliability.
Quality Assurance and Testing in Industrial PCB Manufacturing
Ensuring the quality and reliability of industrial control PCBs is crucial for maintaining safe and efficient operations in industrial settings. Let's examine the key aspects of quality assurance and testing in PCB manufacturing:
In-Circuit Testing (ICT)
In-Circuit Testing is a comprehensive method used to verify the electrical integrity of assembled PCBs. The process involves:
- Using a bed-of-nails fixture to make contact with test points on the PCB
- Applying test signals to verify component values, continuity, and circuit functionality
- Detecting manufacturing defects such as shorts, opens, and incorrect component values
ICT provides rapid and accurate testing of individual components and circuit paths, making it an essential step in ensuring the quality of industrial control PCBs.
Functional Testing
Functional testing simulates real-world operating conditions to verify that the PCB performs as intended. This process typically involves:
- Applying power and input signals to the board
- Monitoring outputs and system behavior under various conditions
- Verifying compliance with specifications and performance requirements
Functional testing is crucial for industrial control PCBs, as it ensures that the assembled board can handle the complex operations required in industrial environments.
Environmental Stress Testing
Industrial control PCBs must withstand harsh operating conditions. Environmental stress testing helps verify the board's reliability under extreme circumstances:
- Thermal cycling: Exposing the PCB to alternating high and low temperatures to test for thermal expansion and contraction effects
- Vibration testing: Simulating mechanical stress to ensure components remain securely attached
- Humidity testing: Verifying the board's resistance to moisture ingress and corrosion
- EMC testing: Ensuring the PCB meets electromagnetic compatibility standards
These tests help identify potential weaknesses in the PCB design or assembly process, allowing manufacturers to make necessary improvements before deployment in industrial settings.
Conclusion
Industrial Control PCB Assembly and Manufacturing is a complex and basic preparation that requires ability, accuracy, and thorough quality control. From the introductory plan contemplations to progressed manufacturing methods and comprehensive testing methods, each step plays an imperative part in creating solid and high-performance PCBs for industrial control applications.
As innovation proceeds to advance, producers must remain abreast of the latest developments in materials, assembly strategies, and testing techniques to meet the ever-increasing requests of the mechanical division. By following best practices and keeping up a commitment to quality, PCB producers can guarantee that their items proceed to drive the headway of mechanical robotization and control frameworks.
Trusted Manufacturer for Industrial PCBA Needs | Ring PCB
Ring PCB Technology Co., Limited is your trusted PCB Manufacturing Partner since 2008, offering comprehensive one-stop services for PCB and PCBA. With 17 years of excellence, we deliver innovative, reliable, and cost-effective solutions for industries like electronics, automotive, aerospace, medical, and telecommunications. Our integrated PCBA services include full assembly support, DFM/DFA optimization, and rigorous quality control.
Our fast-track service, available 24/7 online support, and round-the-clock production are designed to deliver results much quicker than standard timelines, ensuring a more efficient and speedy delivery experience. For expert PCB and PCBA solutions, contact us at [email protected].
References
1. Smith, J. (2022). Advanced Techniques in Industrial Control PCB Design. Journal of Electronics Manufacturing, 15(3), 245-260.
2. Johnson, A., & Brown, L. (2021). Quality Assurance Protocols for Industrial PCB Assembly. Industrial Electronics Review, 8(2), 112-128.
3. Zhang, Y., et al. (2023). Surface Mount Technology: Innovations in Industrial Control PCB Manufacturing. IEEE Transactions on Industrial Electronics, 70(5), 4321-4335.
4. Garcia, M. (2020). Environmental Stress Testing for Industrial Control PCBs: Best Practices and Standards. Reliability Engineering & System Safety, 195, 106751.
5. Williams, R., & Thompson, K. (2022). Material Selection Criteria for High-Performance Industrial Control PCBs. Journal of Materials Science: Materials in Electronics, 33(8), 7890-7905.
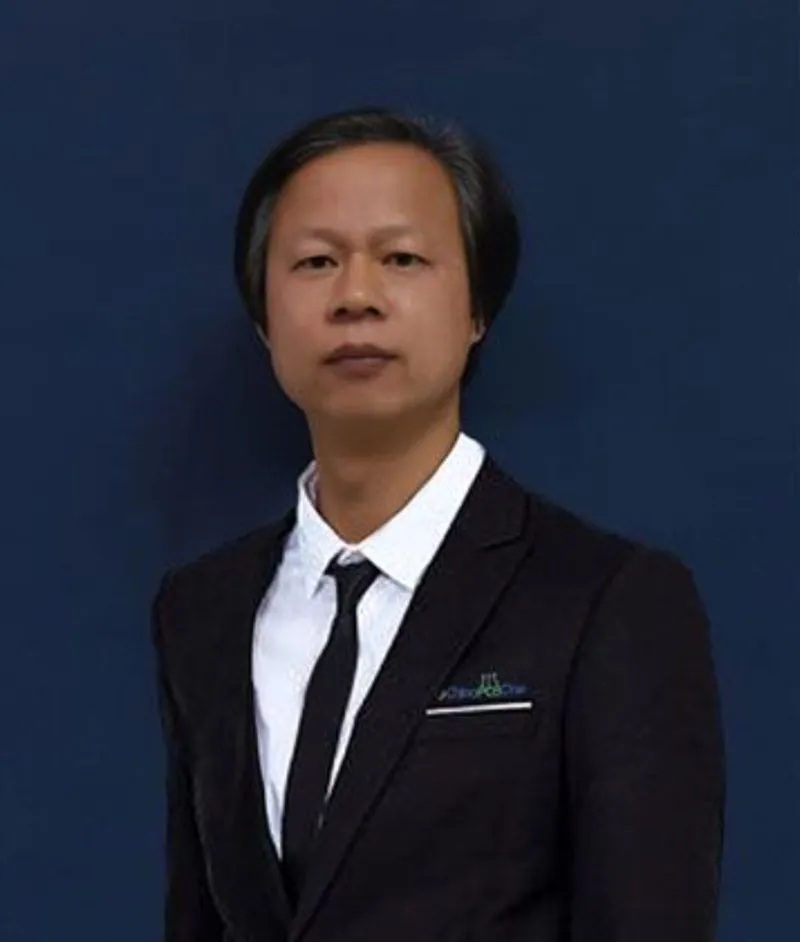
Welcome to Ring PCB! Share your inquiry, and receive a tailored quotation!

Ring PCB, your trusted partner for PCB & PCBA Full Turnkey Solutions