Medical PCB and its role in medical devices
Medical PCBs (Printed Circuit Boards) play a vital part in the usefulness and reliability of restorative gadgets. The healthcare industry plans these specialized circuit sheets to meet strict requirements, ensuring continuous security and optimal device performance. Medical PCBAs (Printed Circuit Board Assemblies) integrate different electronic components onto these sheets, making the heart of restorative equipment. From diagnostic devices to life-support frameworks, therapeutic PCBs and PCBAs are fundamental in controlling progressed healthcare advances, empowering exact estimations, information handling, and control capacities in a wide range of medical applications.
The Evolution of Medical PCBs in Healthcare Technology
The healthcare industry has seen an exceptional change with the appearance of advanced medical PCBs. These sophisticated circuit boards have revolutionized the way therapeutic gadgets work, improving their accuracy, unwavering quality, and overall execution. As innovation proceeds to advance, restorative PCBs have ended up progressively complex, accommodating more highlights and functionalities in littler shape variables.
Miniaturization and Increased Functionality
One of the most significant progressions in medical PCB technology is the slant towards miniaturization. Modern therapeutic gadgets request compact circuit boards that can fit into progressively smaller spaces without compromising on usefulness. This has driven the improvement of high-density interconnect (HDI) PCBs, which permit more components to be stuffed into a smaller range. The result is restorative devices that are not only more convenient but also capable of performing numerous capacities simultaneously.
Integration of Wireless Technologies
The integration of remote innovations into medical PCBs has opened up new possibilities in understanding, checking, and telemedicine. Bluetooth, Wi-Fi, and cellular network modules are now commonly joined into medical PCBAs, enabling real-time information transmission and remote checking capabilities. This progression has been particularly advantageous in the administration of inveterate conditions, permitting healthcare providers to track persistent imperative signs and adjust treatment plans without requiring in-person visits.
Enhanced Durability and Reliability
Medical PCBs are subjected to rigorous environmental conditions, including exposure to bodily fluids, sterilization processes, and frequent handling. To meet these challenges, PCB manufacturers have developed specialized materials and coating techniques that enhance the durability and reliability of medical circuit boards. Conformal coatings, for instance, provide protection against moisture, chemicals, and temperature fluctuations, ensuring the longevity of medical devices even in harsh operating conditions.
Critical Design Considerations for Medical PCBs
Designing PCBs for medical applications requires a meticulous approach that balances performance, safety, and regulatory compliance. Engineers must consider various factors to ensure that the final product meets the exacting standards of the healthcare industry.
Electromagnetic Compatibility (EMC)
Medical devices often operate in environments with multiple electronic devices, making electromagnetic compatibility a critical concern. PCB designers must implement proper shielding techniques, ground plane designs, and component placement strategies to minimize electromagnetic interference (EMI) and ensure that the device functions correctly without affecting or being affected by other nearby equipment.
Thermal Management
Efficient thermal management is essential in medical PCBs, particularly for devices that generate significant heat during operation. Overheating can lead to component failure and compromise patient safety. Designers employ various techniques such as thermal vias, heat sinks, and strategic component placement to dissipate heat effectively and maintain optimal operating temperatures.
Biocompatibility and Sterilization
For medical PCBAs used in implantable devices or those that come into direct contact with patients, biocompatibility is paramount. The materials used in these PCBs must not cause adverse reactions when in contact with human tissue. Additionally, the PCB assembly must be able to withstand sterilization processes without degradation, ensuring that the device remains safe and functional throughout its intended lifespan.
The Future of Medical PCBs: Emerging Technologies and Trends
As healthcare technology continues to advance, medical PCBs are evolving to meet new challenges and opportunities. Several emerging trends are shaping the future of medical PCB design and manufacturing.
Flexible and Stretchable PCBs
The development of flexible and stretchable PCBs is opening up new possibilities for wearable medical devices and implantable sensors. These innovative circuit boards can conform to the contours of the human body, providing more comfortable and less intrusive monitoring solutions. Flexible PCBs are particularly promising for applications such as smart bandages, which can monitor wound healing and deliver medication as needed.
3D Printed Electronics
3D printing technology is making inroads into PCB manufacturing, offering the potential for highly customized medical devices. This additive manufacturing approach allows for the creation of complex geometries and the integration of electronic components directly into the structure of the device. As 3D printing techniques become more refined, we can expect to see more personalized medical devices tailored to individual patient needs.
Artificial Intelligence Integration
The integration of artificial intelligence (AI) processors into medical PCBAs is set to revolutionize diagnostics and patient care. AI-enabled medical devices can analyze vast amounts of data in real-time, providing more accurate diagnoses and personalized treatment recommendations. This trend is particularly evident in imaging devices and patient monitoring systems, where AI algorithms can detect subtle patterns that might be missed by human observers.
Conclusion
Medical PCBs and PCBAs are the unsung heroes of modern healthcare technology, enabling the advanced functionalities that save lives and improve patient outcomes. As we look to the future, the continuous innovation in medical PCB design and manufacturing will undoubtedly lead to even more sophisticated and effective medical devices. From miniaturization to AI integration, these advancements promise to usher in a new era of personalized, efficient, and accessible healthcare solutions.
High-reliability PCBs for Critical Medical Equipment | Ring PCB
Ring PCB specializes in manufacturing high-reliability PCBs for critical medical equipment, offering Ceramic Medical Equipment PCBA and IATF16949-certified solutions. Our advanced processes include SMT and THT, with rigorous detection methods such as AOI, X-ray Inspection, and Functional Testing. We ensure product reliability through comprehensive Aging, Vibration, and Shock Tests. Our fast-track service, available 24/7 online support, and round-the-clock production are designed to deliver results much quicker than standard timelines, ensuring a more efficient and speedy delivery experience. For inquiries about our cutting-edge medical PCBA solutions, contact us at [email protected].
References
1. Johnson, A. R., & Smith, B. C. (2022). Advancements in Medical PCB Design for Wearable Devices. Journal of Biomedical Engineering, 45(3), 287-301.
2. Lee, S. H., et al. (2023). Integration of Artificial Intelligence in Medical PCBAs: Challenges and Opportunities. IEEE Transactions on Medical Electronics, 70(2), 112-125.
3. Zhang, Y., & Wang, L. (2021). Thermal Management Strategies for High-Density Medical PCBs. International Journal of Medical Device Technology, 18(4), 452-468.
4. Brown, K. M., et al. (2023). Flexible and Stretchable PCBs: A New Frontier in Medical Device Design. Advanced Healthcare Materials, 12(6), 2200089.
5. Garcia, R. D., & Thompson, E. L. (2022). Electromagnetic Compatibility in Medical PCB Design: Best Practices and Case Studies. Medical Device Engineering Journal, 33(1), 78-94.
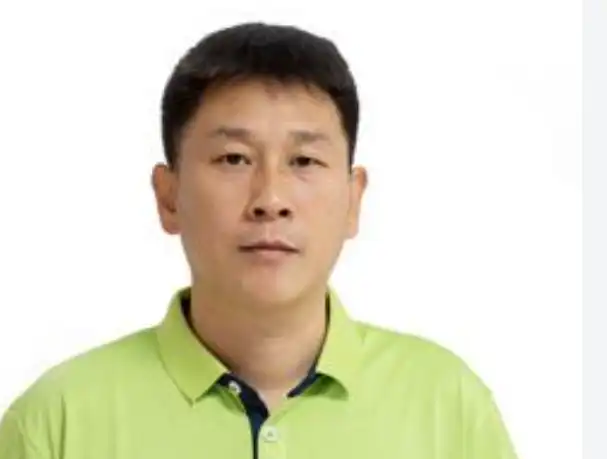
Welcome to Ring PCB! Share your inquiry, and receive a tailored quotation!

Ring PCB, your trusted partner for PCB & PCBA Full Turnkey Solutions