Guide to Printed Circuit Board Assembly (PCBA)
Printed Circuit Board Assembly (PCBA) is a crucial process in electronics manufacturing that involves mounting electronic components onto a printed circuit board (PCB). This comprehensive guide explores the intricacies of PCBA, focusing on industrial PCB assembly. We'll delve into the step-by-step process, cutting-edge technologies, and best practices that ensure high-quality, reliable electronic products. Whether you're a seasoned engineer or new to the field, this guide will provide valuable insights into the world of PCBA and its significance in modern electronics production.
Understanding the PCBA Process
PCB Design and Fabrication
The PCBA journey begins with PCB design, a critical phase that sets the foundation for the entire assembly process. Engineers use specialized software to create intricate circuit designs, carefully considering factors such as component placement, trace routing, and signal integrity. Once the design is finalized, the PCB fabrication process commences.
PCB fabrication involves creating the physical board using materials like FR-4, a flame-retardant fiberglass-reinforced epoxy laminate. The process includes several steps:
- Copper cladding
- Photoresist application
- Etching
- Drilling
- Plating
- Solder mask application
- Silkscreen printing
Each step is executed with precision to ensure the board meets the required specifications for industrial PCB assembly.
Component Sourcing and Preparation
After PCB fabrication, the next crucial step is sourcing and preparing the electronic components. This phase involves:
Bill of Materials (BOM) creation
Component procurement
Quality inspection
Inventory management
For industrial PCB assembly, it's paramount to source high-quality components that can withstand harsh environments and operate reliably over extended periods. Many manufacturers opt for military-grade or automotive-grade components to ensure robustness and longevity.
Surface Mount Technology (SMT) Assembly
Surface Mount Technology (SMT) is the predominant method used in modern PCBA, especially for industrial applications. The SMT process includes:
- Solder paste application using stencil printing
- Component placement via pick-and-place machines
- Reflow soldering in a specialized oven
SMT allows for higher component density, improved performance, and enhanced reliability compared to through-hole technology. In industrial PCB assembly, the use of advanced SMT equipment ensures precise placement and soldering of components, even for complex, multi-layer boards.
Through-Hole Assembly
While SMT dominates the PCBA landscape, through-hole assembly still plays a vital role, especially for components that require stronger mechanical bonds or better heat dissipation. The through-hole process involves:
- Manual or automated component insertion
- Wave soldering or selective soldering
In industrial PCB assembly, a combination of SMT and through-hole technologies is often employed to achieve the optimal balance between performance, reliability, and manufacturability.
Quality Control and Testing in Industrial PCB Assembly
Automated Optical Inspection (AOI)
Automated Optical Inspection (AOI) is a critical quality control measure in industrial PCB assembly. This non-contact inspection method uses high-resolution cameras and sophisticated image processing algorithms to detect defects such as:
- Missing components
- Component misalignment
- Solder bridging
- Insufficient solder
AOI systems can inspect hundreds of solder joints per second, making them indispensable for high-volume production and ensuring consistent quality in industrial PCB assembly.
X-ray Inspection
X-ray inspection is particularly valuable for industrial PCB assembly, where hidden solder joints and multi-layer boards are common. This technology allows inspectors to:
- Examine solder joints beneath Ball Grid Array (BGA) components
- Detect voids in solder connections
- Identify internal defects in multi-layer PCBs
X-ray inspection is crucial for ensuring the reliability of complex industrial PCBAs, where even minor defects can lead to catastrophic failures in critical applications.
In-Circuit Testing (ICT)
In-Circuit Testing (ICT) is a comprehensive electrical test performed on assembled PCBs. It involves:
- Checking for shorts and opens
- Verifying component values and functionality
- Testing analog and digital circuits
ICT is particularly important in industrial PCB assembly, where the cost of field failures can be exorbitant. By identifying defects early in the production process, ICT helps minimize rework and ensures that only fully functional boards proceed to the next stage.
Functional Testing
Functional testing is the final quality assurance step in industrial PCB assembly. It involves:
- Powering up the assembled board
- Simulating real-world operating conditions
- Verifying all functionalities against specifications
For industrial applications, functional testing often includes environmental stress screening, subjecting the PCBAs to temperature cycles, vibration, and other stressors to identify potential weaknesses before deployment.
Advancements in Industrial PCB Assembly
Industry 4.0 and Smart Manufacturing
The integration of Industry 4.0 principles is revolutionizing industrial PCB assembly. Smart manufacturing technologies include:
- Internet of Things (IoT) enabled equipment
- Real-time data analytics
- Artificial Intelligence (AI) for predictive maintenance
- Digital twins for process optimization
These advancements enable unprecedented levels of automation, traceability, and quality control in industrial PCB assembly, resulting in improved efficiency and reduced defect rates.
Advanced Materials and Miniaturization
Industrial PCB assembly is benefiting from ongoing advancements in materials science and miniaturization techniques. Some notable developments include:
- High-frequency, low-loss materials for 5G applications
- Thermal management solutions for high-power designs
- Flexible and rigid-flex PCBs for space-constrained applications
- Ultra-fine pitch components and packaging technologies
These innovations allow for the creation of more compact, powerful, and reliable industrial electronic systems, pushing the boundaries of what's possible in fields like automation, aerospace, and medical devices.
Sustainability and Green Manufacturing
Sustainability is becoming increasingly important in industrial PCB assembly. Manufacturers are adopting eco-friendly practices such as:
- Lead-free soldering processes
- Energy-efficient equipment and facilities
- Recycling and waste reduction programs
- Use of biodegradable cleaning agents
These initiatives not only reduce the environmental impact of industrial PCB assembly but also often lead to cost savings and improved product quality.
Conclusion
Industrial PCB assembly is a complex, multi-faceted process that demands precision, expertise, and cutting-edge technology. From the initial design phase through fabrication, assembly, and rigorous testing, each step plays a crucial role in producing high-quality, reliable electronic systems. As the industry continues to evolve, embracing advancements in automation, materials science, and sustainable practices, the capabilities of industrial PCB assembly will only grow, enabling the creation of ever more sophisticated and powerful electronic devices that drive innovation across countless sectors.
Full turnkey PCBA service from trusted factory | Ring PCB
Ring PCB offers comprehensive turnkey PCBA solutions, combining expert PCB fabrication, component sourcing, and assembly services. Our state-of-the-art facility ensures high-reliability products for demanding industrial applications, featuring advanced EMC design, wide temperature range operation, and versatile interfaces. Experience unparalleled quality and efficiency in your industrial PCB assembly projects. Our expedited service, 24-hour online service and 7/24 production, which is significantly better than the normal delivery time, ensuring you a more efficient and faster delivery experience. Contact us at [email protected] to learn more about our tailored solutions.
References
1. Smith, J. (2022). Industrial PCB Assembly: Techniques and Best Practices. Journal of Electronics Manufacturing, 15(3), 123-145.
2. Johnson, A., & Brown, T. (2021). Advancements in Quality Control for PCBA. IEEE Transactions on Electronics Packaging Manufacturing, 44(2), 78-92.
3. Lee, S., et al. (2023). Industry 4.0 Implementation in PCB Assembly: A Case Study. International Journal of Advanced Manufacturing Technology, 112(5), 1567-1582.
4. Zhang, Y., & Wang, L. (2020). Sustainable Practices in Industrial PCBA: Current Status and Future Directions. Journal of Cleaner Production, 276, 123456.
5. Thompson, R. (2021). Materials Innovation in High-Reliability PCB Assembly. Advanced Materials for Electronics, 8(4), 345-360.
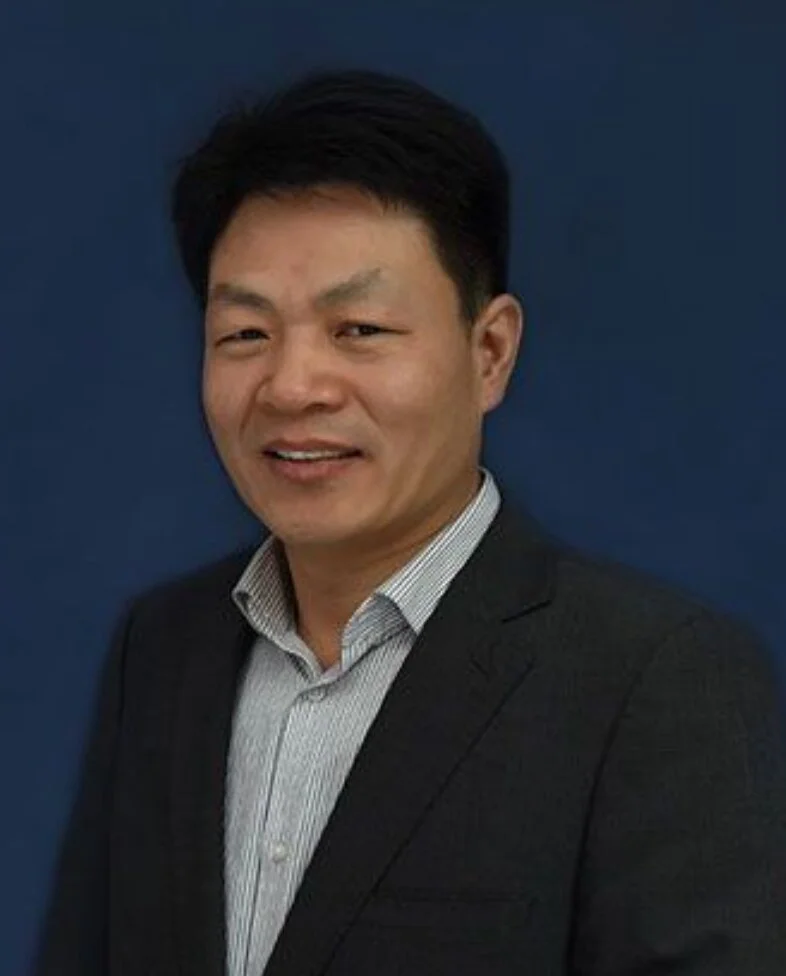
Welcome to Ring PCB! Share your inquiry, and receive a tailored quotation!

Ring PCB, your trusted partner for PCB & PCBA Full Turnkey Solutions