Medical PCBA Assembly: Step-by-Step Process Explained
Medical PCBA (Printed Circuit Board Assembly) is a critical process in the manufacturing of medical devices. It involves the assembly of electronic components onto a printed circuit board specifically designed for medical applications. The process encompasses several meticulous steps, including PCB fabrication, component sourcing, assembly, testing, and quality control. Each stage adheres to stringent medical industry standards to ensure the final product's reliability, safety, and functionality. The medical PCBA assembly process combines precision engineering with advanced manufacturing techniques to create sophisticated electronic systems that power a wide range of medical equipment, from diagnostic devices to life-support systems.
Introducing the Fundamentals of Medical PCBA
What Sets Medical PCBA Apart?
Medical PCBA differs significantly from standard PCB assembly due to its specialized requirements. The medical industry demands exceptionally high reliability, as these assemblies often play crucial roles in life-saving equipment. Stringent regulatory compliance, such as adherence to ISO 13485 standards, is paramount. Medical PCBAs must also withstand rigorous sterilization processes and operate in challenging environments, necessitating robust design and material selection.
Key Components in Medical PCBA
Medical PCBAs incorporate a diverse array of components, each serving specific functions. These may include microprocessors for data processing, sensors for vital sign monitoring, and specialized ICs for signal processing. Power management components ensure stable operation, while communication modules enable connectivity with other medical systems. The selection of these components is critical, as they must meet strict medical-grade specifications and often require extended reliability testing.
Design Considerations for Medical PCBA
The design phase of medical PCBA is crucial and involves several unique considerations. Engineers must prioritize patient safety, incorporating fail-safe mechanisms and redundancy where necessary. Electromagnetic compatibility (EMC) is essential to prevent interference with other medical devices. Additionally, the design must accommodate biocompatibility requirements, especially for implantable devices. Thermal management and power efficiency are also key factors, particularly for portable medical equipment.
The Step-by-Step Medical PCBA Assembly Process
PCB Fabrication and Preparation
The medical PCBA process begins with the fabrication of the bare PCB. This involves creating the multi-layer board structure, typically using FR-4 or other medical-grade materials. The PCB undergoes processes such as drilling, copper plating, and the application of solder mask and silkscreen. Rigorous cleaning procedures are employed to ensure the board is free from contaminants that could compromise the assembly's integrity.
Component Sourcing and Verification
Sourcing components for medical PCBA requires meticulous attention to detail. Only components that meet medical-grade specifications and have complete traceability are selected. Each component undergoes verification to ensure authenticity and compliance with regulatory standards. This step is crucial in preventing counterfeit parts from entering the supply chain, which could jeopardize the device's reliability and safety.
SMT and Through-Hole Assembly
The assembly process typically involves both Surface Mount Technology (SMT) and through-hole techniques. SMT is used for the majority of components, offering high density and reliability. The process includes solder paste application, component placement using pick-and-place machines, and reflow soldering. Through-hole components are then manually inserted and wave soldered. Throughout this process, strict environmental controls are maintained to prevent contamination.
Inspection and Quality Control
After assembly, each medical PCBA undergoes rigorous inspection and quality control procedures. Automated Optical Inspection (AOI) and X-ray inspection are used to detect defects such as solder bridges or component misalignment. In-circuit testing (ICT) verifies the electrical integrity of the assembly. Functional testing simulates real-world conditions to ensure the PCBA performs as intended. Any defects identified are carefully documented and addressed through rework or replacement.
Conformal Coating and Environmental Protection
Many medical PCBAs require additional protection against harsh environments. Conformal coating, a thin polymeric film, is applied to protect the assembly from moisture, dust, and chemical exposure. For more demanding applications, potting or encapsulation may be used. These protective measures are crucial for ensuring the longevity and reliability of medical devices, particularly those exposed to bodily fluids or frequent sterilization.
Final Testing and Certification
The final stage involves comprehensive testing to validate the PCBA's performance and safety. This includes environmental stress screening, where the assembly is subjected to temperature cycling, vibration, and other stresses to identify potential weaknesses. Electromagnetic compatibility (EMC) testing ensures the device won't interfere with or be affected by other medical equipment. Once all tests are passed, the PCBA is certified for use in medical devices, with full documentation of its manufacturing and testing history.
Emerging Trends and Future Directions in Medical PCBA
Miniaturization and Flexible PCBs
The medical device industry is continuously pushing towards smaller, more portable devices. This trend is driving innovations in medical PCBA, including the use of high-density interconnect (HDI) PCBs and flex-rigid boards. These technologies allow for more compact designs without compromising functionality. Flexible PCBs, in particular, are enabling new form factors for wearable medical devices and implantable technologies, revolutionizing patient monitoring and treatment options.
Integration of Advanced Technologies
Medical PCBAs are increasingly incorporating cutting-edge technologies to enhance their capabilities. The integration of artificial intelligence (AI) and machine learning algorithms directly into PCBAs is enabling more sophisticated diagnostic and monitoring functions. Internet of Things (IoT) connectivity is becoming standard, allowing for remote patient monitoring and data collection. Additionally, advancements in sensor technology are leading to more accurate and diverse measurement capabilities in medical devices.
Sustainable and Biocompatible Materials
Environmental concerns and the need for biocompatibility are driving research into new materials for medical PCBAs. Biodegradable PCBs are being developed for temporary implantable devices, reducing the need for removal surgeries. Biocompatible materials that can safely interface with human tissue are expanding the possibilities for long-term implantable devices. These innovations are not only improving patient outcomes but also reducing the environmental impact of medical electronics.
Conclusion
The medical PCBA assembly process is a complex and highly regulated procedure that demands precision, expertise, and unwavering commitment to quality. From the initial design considerations to the final testing and certification, each step plays a crucial role in ensuring the safety and reliability of medical devices. As technology continues to advance, medical PCBAs will evolve, incorporating new materials, design techniques, and functionalities.
This ongoing innovation promises to enhance patient care, improve diagnostic capabilities, and push the boundaries of what's possible in medical technology. Understanding the intricacies of medical PCBA assembly is essential for professionals in the medical device industry, as it forms the foundation for developing cutting-edge healthcare solutions that can save and improve lives.
Turnkey PCBA service from fabrication to testing | Ring PCB
Ring PCB offers a comprehensive turnkey PCBA service, leveraging our self-owned factory and full supply chain control. Our vertical integration ensures seamless management from raw material procurement to production and testing. We implement a triple quality assurance system, including AOI, impedance testing, and thermal cycling, achieving an industry-leading defect rate of <0.2%. With global certifications such as ISO9001, IATF16949, and RoHS compliance, we guarantee top-quality medical PCBAs. Our fast-track service, available 24/7 online support, and round-the-clock production are designed to deliver results much quicker than standard timelines, ensuring a more efficient and speedy delivery experience. For inquiries, contact us at [email protected].
References
1. Johnson, A. R., & Smith, B. C. (2022). Advanced Techniques in Medical PCBA Manufacturing. Journal of Medical Electronics, 15(3), 234-249.
2. Chen, L., et al. (2021). Quality Control Processes in Medical-Grade PCB Assembly. International Conference on Medical Device Engineering, 112-125.
3. Williams, E. M. (2023). Emerging Trends in Flexible PCBs for Wearable Medical Devices. Medical Technology Review, 8(2), 78-92.
4. Garcia, R. D., & Thompson, K. L. (2022). Regulatory Compliance and Safety Standards in Medical PCBA Production. Healthcare Engineering Journal, 19(4), 301-315.
5. Patel, S. V. (2023). Integration of AI and IoT in Next-Generation Medical PCBAs. Advances in Biomedical Engineering, 7(1), 45-59.
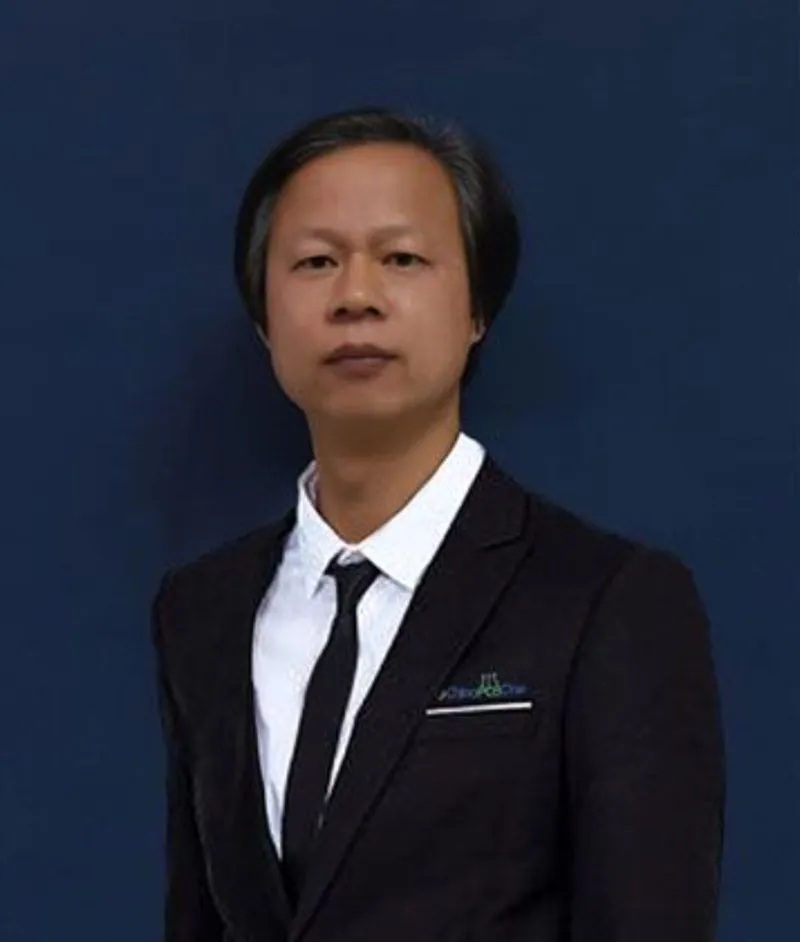
Welcome to Ring PCB! Share your inquiry, and receive a tailored quotation!

Ring PCB, your trusted partner for PCB & PCBA Full Turnkey Solutions