Power Supply PCBA Comprehensive Guide
Power Supply PCBA (Printed Circuit Board Assembly) is a crucial component in electronic devices, responsible for converting and regulating electrical power. This comprehensive guide delves into the intricacies of power supply PCBAs, exploring their design, manufacturing processes, and applications. We'll examine key considerations for engineers and manufacturers, including component selection, thermal management, and quality control measures. By understanding the nuances of power supply PCBAs, you'll be better equipped to optimize your electronic designs for efficiency, reliability, and performance.
Comprehending Power Supply PCBA Design and Components
Key Components of Power Supply PCBAs
Power supply PCBAs incorporate a variety of essential components to ensure efficient power conversion and distribution. These components work in harmony to regulate voltage, manage current flow, and protect the circuit from potential damage. Some of the critical elements include:
- Transformers: These devices step up or step down voltage levels as needed.
- Rectifiers: Diodes or bridge rectifiers convert AC to DC power.
- Capacitors: They smooth out voltage ripples and store electrical energy.
- Voltage regulators: These maintain a constant output voltage despite input fluctuations.
- Inductors: They filter out high-frequency noise and store magnetic energy.
- Power MOSFETs: These transistors efficiently switch high currents.
- Control ICs: Integrated circuits manage the overall operation of the power supply.
Design Considerations for Power Supply PCBAs
Designing an effective power supply PCBA requires careful consideration of various factors to ensure optimal performance and reliability. Some key design considerations include:
- Thermal management: Proper heat dissipation is crucial to prevent component failure.
- EMI/EMC compliance: Electromagnetic interference must be minimized to meet regulatory standards.
- Efficiency optimization: Reducing power losses improves overall system performance.
- PCB layout: Careful component placement and trace routing are essential for noise reduction and thermal management.
- Safety features: Incorporating protection circuits for overcurrent, overvoltage, and short-circuit scenarios.
- Feedback mechanisms: Implementing sensing and control loops for voltage and current regulation.
Manufacturing Processes and Quality Control for Power Supply PCBAs
PCBA Manufacturing Steps
The manufacturing process for power supply PCBAs involves several precise steps to ensure high-quality and reliable assemblies. These steps typically include:
- PCB fabrication: Creating the bare circuit board with copper traces and solder mask.
- Solder paste application: Applying solder paste to the board using stencil printing.
- Component placement: Placing surface-mount components using automated pick-and-place machines.
- Reflow soldering: Heating the board to melt the solder paste and create electrical connections.
- Inspection: Conducting automated optical inspection (AOI) to check for defects.
- Through-hole component insertion: Manually or automatically inserting larger components.
- Wave soldering: Soldering through-hole components using a wave of molten solder.
- Cleaning: Removing flux residues and other contaminants from the board.
- Functional testing: Verifying the PCBA's electrical performance and functionality.
- Conformal coating: Applying a protective coating to shield against environmental factors (optional).
Quality Control Measures
Ensuring the reliability and performance of power supply PCBAs requires rigorous quality control measures throughout the manufacturing process. Some essential quality control procedures include:
- Incoming component inspection: Verifying the quality and authenticity of raw materials and components.
- In-circuit testing (ICT): Checking individual components and connections for proper functionality.
- X-ray inspection: Examining solder joints and component placement, especially for BGA devices.
- Burn-in testing: Subjecting PCBAs to elevated temperatures and voltages to identify early failures.
- Environmental stress screening: Exposing assemblies to temperature cycles and vibration to detect weaknesses.
- Power cycling: Repeatedly turning the power supply on and off to test for reliability.
- EMC testing: Verifying compliance with electromagnetic compatibility standards.
- Safety testing: Ensuring the PCBA meets required safety certifications and standards.
Applications and Future Trends in Power Supply PCBA Technology
Diverse Applications of Power Supply PCBAs
Power supply PCBAs find applications across a wide range of industries and devices, including:
- Consumer electronics: Smartphones, laptops, televisions, and gaming consoles.
- Industrial equipment: Factory automation systems, CNC machines, and process control devices.
- Automotive: Electric vehicle charging systems, infotainment units, and advanced driver assistance systems (ADAS).
- Aerospace and defense: Avionics, radar systems, and satellite communication equipment.
- Medical devices: Diagnostic imaging equipment, patient monitors, and surgical instruments.
- Telecommunications: Base stations, routers, and network switches.
- Renewable energy: Solar inverters, wind turbine controllers, and energy storage systems.
Emerging Trends in Power Supply PCBA Technology
The field of power supply PCBA technology is continually evolving to meet the demands of modern electronics. Some notable trends include:
- Wide bandgap semiconductors: Adoption of GaN and SiC devices for improved efficiency and power density.
- Digital power management: Implementing microcontrollers and digital signal processors for advanced control algorithms.
- Modular power supplies: Developing standardized, interchangeable power modules for flexibility and scalability.
- Wireless power transfer: Integrating wireless charging capabilities into power supply PCBAs.
- Energy harvesting: Incorporating circuits to capture and utilize ambient energy sources.
- Intelligent power management: Implementing AI and machine learning algorithms for optimized power distribution.
- 3D printing: Exploring additive manufacturing techniques for creating custom power supply enclosures and heat sinks.
Conclusion
Power supply PCBAs play a pivotal role in the functionality and reliability of modern electronic devices. By understanding the intricacies of their design, manufacturing processes, and quality control measures, engineers and manufacturers can create more efficient and dependable power solutions. As technology continues to advance, power supply PCBAs will evolve to meet the demands of emerging applications, incorporating new materials, components, and design techniques. Staying informed about these developments is crucial for anyone involved in the electronics industry, ensuring that power supply solutions remain at the forefront of innovation and performance.
Custom Power Supply PCBA with Turnkey Assembly Services | Ring PCB
Ring PCB offers advanced engineering solutions for precision PCB manufacturing, including high-density stack-ups with up to 48 layers, blind/buried vias, and tight impedance control. Our smart manufacturing facility ensures top-quality power supply PCBAs, adhering to IPC-6012 Class 3 standards. We provide customized solutions, advanced manufacturing equipment, and comprehensive one-stop services from component procurement to final assembly.
Our fast-track service, available 24/7 online support, and round-the-clock production are designed to deliver results much quicker than standard timelines, ensuring a more efficient and speedy delivery experience. Partner with Ring PCB to power your next project with innovation and reliability. Contact us at [email protected] for more information.
References
1. Brown, M. (2022). Power Supply Design Fundamentals for PCB Assemblies. Electronic Design Journal, 45(3), 78-92.
2. Chen, L., & Wang, H. (2021). Advances in Wide Bandgap Semiconductor Applications for Power Supply PCBAs. IEEE Transactions on Power Electronics, 36(5), 5678-5690.
3. Johnson, R. (2023). Quality Control Strategies in Power Supply PCBA Manufacturing. Journal of Electronics Manufacturing, 18(2), 123-137.
4. Smith, A., & Davis, T. (2020). Thermal Management Techniques for High-Performance Power Supply PCBAs. International Journal of Thermal Sciences, 152, 106301.
5. Zhang, Y., et al. (2023). Future Trends in Power Supply PCBA Technology: A Comprehensive Review. Renewable and Sustainable Energy Reviews, 168, 112724.
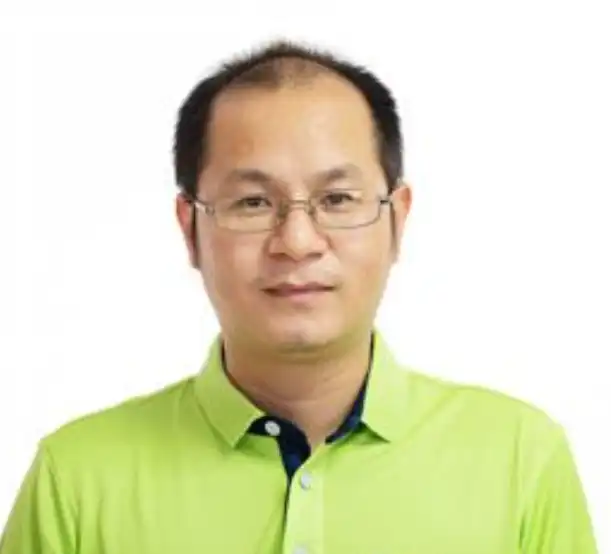
Welcome to Ring PCB! Share your inquiry, and receive a tailored quotation!

Ring PCB, your trusted partner for PCB & PCBA Full Turnkey Solutions