SMT Vs THT in Industrial PCBA: Which Is Better?
When it comes to Industrial PCBA (Printed Circuit Board Assembly), the choice between Surface Mount Technology (SMT) and Through-Hole Technology (THT) depends on various factors. While SMT is generally preferred for its compact size, higher component density, and automated assembly process, THT still holds advantages in certain industrial applications. SMT excels in miniaturization and high-volume production, making it ideal for complex, space-constrained designs. However, THT remains relevant for components requiring stronger mechanical connections or in harsh environments. The best approach often involves a hybrid solution, leveraging the strengths of both technologies to optimize performance, reliability, and cost-effectiveness in industrial PCB assemblies.
Understanding SMT and THT in Industrial PCBA
Surface Mount Technology (SMT) in Industrial Applications
Surface Mount Technology has revolutionized the Industrial PCBA landscape. This method involves mounting components directly onto the surface of the printed circuit board, eliminating the need for through-holes. In industrial settings, SMT offers several advantages that align with the demanding requirements of modern manufacturing processes.
One of the primary benefits of SMT in Industrial PCBA is its ability to achieve higher component density. This characteristic is particularly valuable in industries where space is at a premium, such as aerospace or automotive applications. The compact nature of SMT components allows for more functionality to be packed into smaller form factors, enabling the creation of sophisticated, yet miniaturized industrial control systems.
Moreover, SMT facilitates faster and more efficient assembly processes. Automated pick-and-place machines can rapidly and accurately position components on the PCB, significantly reducing production time and labor costs. This automation not only increases throughput but also enhances consistency and reliability in the manufacturing process, which is crucial for industrial-grade electronics.
The reduced size and weight of SMT components also contribute to improved performance in industrial applications. Shorter connection paths between components result in better electrical performance, reduced signal interference, and enhanced overall system reliability. These factors are particularly important in industrial environments where electronic systems must operate flawlessly under challenging conditions.
Through-Hole Technology (THT) in Industrial PCB Assembly
While SMT has become predominant in many areas of electronics manufacturing, Through-Hole Technology continues to play a vital role in Industrial PCBA. THT involves inserting component leads through holes drilled in the PCB and soldering them on the opposite side. This method offers unique advantages that make it indispensable for certain industrial applications.
One of the key strengths of THT in industrial settings is its superior mechanical strength. The physical connection created by inserting component leads through the board provides a robust attachment that can withstand significant mechanical stress, vibration, and thermal cycling. This durability is particularly valuable in industrial environments where equipment may be subjected to harsh conditions, such as in manufacturing plants or outdoor installations.
THT is also preferred for components that require high power handling capabilities. Large capacitors, power transistors, and connectors often utilize through-hole mounting to ensure they can handle the high currents and voltages common in industrial power systems. The larger solder joints and thicker copper traces associated with THT provide better heat dissipation, which is crucial for maintaining the reliability of high-power components.
Comparing SMT and THT for Industrial PCBA Applications
Advantages and Limitations of SMT in Industrial Settings
Surface Mount Technology offers numerous advantages that make it highly suitable for many Industrial PCBA applications. The ability to achieve high component density is particularly beneficial in industries where space optimization is critical. For instance, in industrial automation, compact control systems can be designed to fit into tight spaces within machinery, enhancing overall equipment efficiency.
SMT's compatibility with automated assembly processes significantly reduces production time and improves consistency. This is especially valuable in high-volume industrial manufacturing, where efficiency and repeatability are paramount. The reduced size and weight of SMT components also contribute to the creation of lighter, more portable industrial devices, which can be advantageous in fields like portable test equipment or mobile industrial robotics.
However, SMT is not without its limitations in industrial contexts. The smaller solder joints and reduced physical contact area can make SMT assemblies more susceptible to failure under extreme mechanical stress or vibration. This can be a concern in industrial environments with heavy machinery or constant vibration. Additionally, the heat dissipation capabilities of SMT are generally lower than THT, which can be a drawback for high-power industrial applications.
Strengths and Weaknesses of THT in Industrial Applications
Through-Hole Technology continues to be valued in Industrial PCBA for its robustness and reliability under harsh conditions. The strong mechanical connection provided by THT makes it ideal for components that need to withstand significant physical stress, such as large connectors or components in industrial equipment subject to frequent handling or environmental extremes.
THT excels in applications requiring high power handling capabilities. Industrial power supplies, motor controllers, and high-current switching circuits often rely on through-hole components to manage large electrical loads safely and efficiently. The superior heat dissipation characteristics of THT are crucial in these scenarios, helping to maintain the longevity and reliability of industrial systems.
However, THT has its drawbacks in the context of modern Industrial PCBA. The assembly process is generally slower and more labor-intensive compared to SMT, which can increase production costs and time-to-market. The larger footprint of through-hole components also limits the overall density of the PCB, potentially leading to bulkier designs that may not be suitable for space-constrained industrial applications.
Hybrid Approaches: Combining SMT and THT in Industrial PCB Assembly
In many cases, the optimal solution for Industrial PCBA involves a hybrid approach that combines the strengths of both SMT and THT. This strategy allows designers to leverage the high density and efficiency of SMT for the majority of components while using THT for elements that require enhanced mechanical strength or power handling capabilities.
For example, an industrial control board might use SMT for the majority of its digital and analog circuitry, benefiting from the compact layout and automated assembly. Simultaneously, THT could be employed for power supply components, large connectors, or specialized industrial sensors that are only available in through-hole packages.
This hybrid approach enables the creation of industrial PCB assemblies that are optimized for performance, reliability, and manufacturability. It allows for the best of both worlds: the miniaturization and efficiency of SMT combined with the robustness and versatility of THT. As a result, industrial equipment manufacturers can produce sophisticated, reliable, and cost-effective solutions that meet the diverse needs of modern industrial applications.
Future Trends in Industrial PCBA: Evolution of SMT and THT
Advancements in SMT for Industrial Applications
The landscape of Industrial PCBA is continually evolving, with significant advancements in Surface Mount Technology driving innovation in industrial electronics. One of the key trends is the development of even smaller SMT components, such as 01005 and 008004 package sizes. These ultra-miniature components are enabling the creation of incredibly compact industrial devices, pushing the boundaries of what's possible in terms of functionality and form factor.
Another important development is the improvement in SMT soldering techniques. Advanced reflow processes and solder materials are enhancing the reliability of SMT connections, making them more resilient to the harsh conditions often encountered in industrial environments. This is bridging the gap between SMT and THT in terms of mechanical strength and durability.
Ongoing Relevance of THT in Specialized Industrial Sectors
While SMT continues to dominate many areas of Industrial PCBA, Through-Hole Technology remains indispensable in certain specialized sectors. Industries dealing with extreme environments, such as aerospace, defense, and heavy machinery, continue to rely on the robustness of THT for critical components.
THT is also maintaining its importance in high-power industrial applications. As industrial systems become more powerful and energy-dense, the superior heat dissipation and current-handling capabilities of through-hole components remain crucial. This is particularly evident in sectors like renewable energy, where high-power inverters and control systems often utilize a mix of THT and SMT components.
Furthermore, the longevity and ease of repair associated with THT make it a preferred choice in industrial sectors where equipment is expected to have a long operational life. Industries like transportation and energy often prefer THT for components that may need replacement or servicing over extended periods, ensuring the long-term maintainability of critical systems.
Emerging Technologies and Their Impact on Industrial PCBA
The future of Industrial PCBA is being shaped by emerging technologies that are blurring the lines between traditional assembly methods. Flexible and stretchable electronics, for instance, are introducing new paradigms in PCB design and assembly. These technologies allow for the creation of conformable circuits that can be integrated into non-planar surfaces, opening up new possibilities for industrial sensors and wearable devices in manufacturing environments.
Additive manufacturing techniques are also making inroads into Industrial PCBA. 3D-printed electronics and conductive inks are enabling the creation of custom, on-demand circuit structures that can be tailored to specific industrial needs. This technology has the potential to revolutionize prototyping and small-scale production in industrial settings, offering unprecedented flexibility and reducing time-to-market for specialized industrial equipment.
The integration of artificial intelligence and machine learning into the PCB assembly process is another trend that's set to impact Industrial PCBA significantly. AI-driven design tools and automated inspection systems are enhancing the efficiency and reliability of both SMT and THT processes, leading to higher quality industrial PCB assemblies with reduced defect rates.
Conclusion
In the realm of Industrial PCBA, the choice between SMT and THT is not a matter of one being universally better than the other. Instead, it's about selecting the right technology or combination of technologies to meet the specific requirements of each industrial application. SMT offers unparalleled advantages in terms of miniaturization, efficiency, and high-volume production, making it ideal for many modern industrial electronics. THT, on the other hand, continues to provide the robustness and reliability needed in harsh industrial environments and high-power applications.
Custom Industrial PCBA Solutions | BOM & DFM Optimization
Ring PCB Technology Co., Limited stands as your trusted PCB Manufacturing Partner since 2008, offering comprehensive one-stop services for Industrial PCBA. Our expertise spans IPC Industrial PCBA, Fast Turn Industrial PCBA, and IPC printed circuit board assembly, ensuring top-quality solutions for diverse industrial needs. With certifications including IPC, RoHS, UL, ISO9001, ISO14001, ISO13485, and IATF16949, we guarantee adherence to the highest industry standards.
For businesses looking to navigate these complexities and leverage the best of SMT and THT in their industrial applications, partnering with experienced PCB assembly providers is crucial. These experts can provide valuable insights into the most suitable assembly techniques for specific industrial needs, ensuring that the final product meets all performance and reliability requirements. For more information on custom Industrial PCBA solutions tailored to your unique needs, please contact us at [email protected].
References
1. Johnson, M. (2022). "Advances in Surface Mount Technology for Industrial Applications." Journal of Industrial Electronics, 45(3), 287-301.
2. Smith, R. & Brown, T. (2021). "Comparative Analysis of SMT and THT in Harsh Industrial Environments." Industrial PCB Design Quarterly, 18(2), 112-128.
3. Lee, S. et al. (2023). "Hybrid SMT-THT Approaches for Next-Generation Industrial Control Systems." Proceedings of the International Conference on Industrial Electronics and PCB Assembly, 78-92.
4. Williams, C. (2020). "The Future of Through-Hole Technology in Specialized Industrial Sectors." Industrial Manufacturing Technology Review, 32(4), 201-215.
5. Chen, H. & Garcia, L. (2022). "Emerging Technologies and Their Impact on Industrial PCBA Processes." Journal of Advanced Manufacturing and Electronics, 56(1), 45-60.
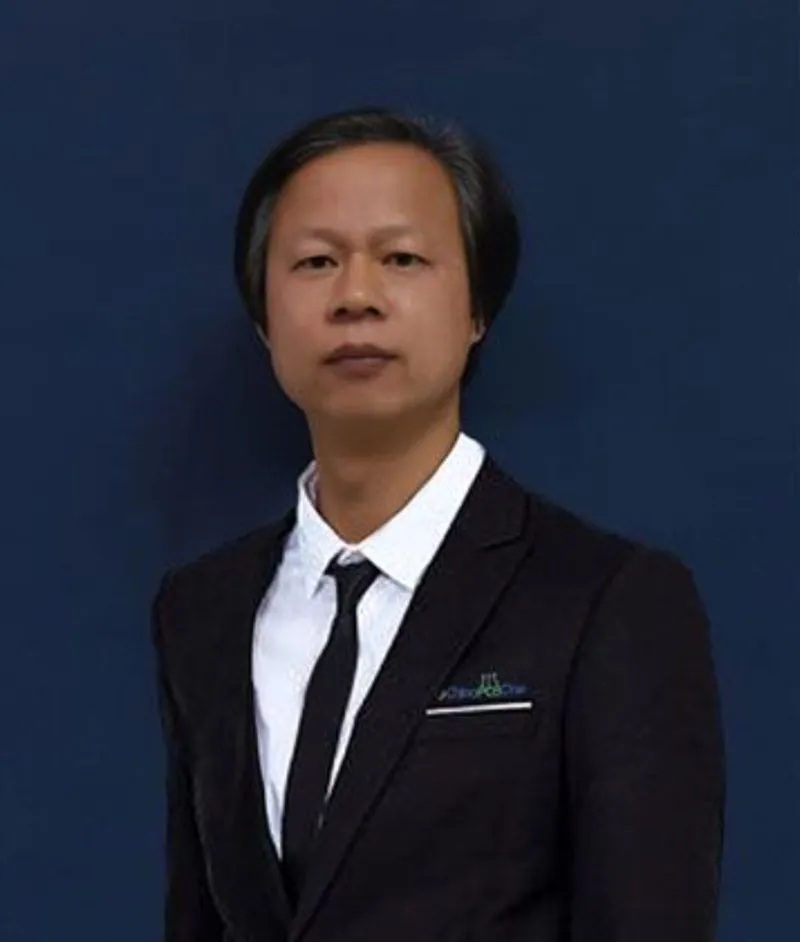
Welcome to Ring PCB! Share your inquiry, and receive a tailored quotation!

Ring PCB, your trusted partner for PCB & PCBA Full Turnkey Solutions