UL/cUL Certified PCBA vs. Non-Certified: What’s the Real Difference?
When it comes to Industrial PCBA (Printed Circuit Board Assembly), the distinction between UL/cUL certified and non-certified products is crucial. UL/cUL certification ensures that PCBAs meet rigorous safety standards, undergo extensive testing, and comply with North American regulations. Certified PCBAs offer enhanced reliability, reduced liability risks, and easier market access. Non-certified PCBAs may be less expensive initially but can lead to potential safety hazards, regulatory issues, and higher long-term costs. Ultimately, the choice between certified and non-certified PCBAs depends on the specific application, regulatory requirements, and risk tolerance of the end-user.
The UL/cUL Certification for Industrial PCBA
What is UL/cUL Certification?
UL (Underwriters Laboratories) and cUL (Canadian UL) certifications are widely recognized marks of safety and quality in North America. For Industrial PCBA manufacturers, obtaining these certifications demonstrates a commitment to producing high-quality, safe products that meet stringent standards. The certification process involves rigorous testing, documentation review, and ongoing compliance checks to ensure that PCBAs meet specific safety requirements.
The Certification Process for Industrial PCBA
Obtaining UL/cUL certification for Industrial PCBA is a comprehensive process that involves several steps:
1. Initial application and documentation submission
2. Product sample testing
3. Manufacturing facility inspection
4. Compliance evaluation
5. Certification issuance
6. Ongoing compliance monitoring
This rigorous process ensures that certified Industrial PCBAs meet the highest standards of safety and quality. Manufacturers must demonstrate consistent adherence to these standards through regular audits and inspections to maintain their certification status.
Key Standards and Requirements
UL/cUL certification for Industrial PCBA encompasses various standards, including:
- UL 796 - Printed-Wiring Boards
- UL 94 - Flammability of Plastic Materials
- UL 746E - Polymeric Materials - Industrial Laminates, Filament Wound Tubing, Vulcanized Fibre, and Materials Used in Printed-Wiring Boards
- UL 508A - Industrial Control Panels
These standards address crucial aspects such as material selection, design considerations, manufacturing processes, and safety requirements specific to Industrial PCBA applications.
Benefits of UL/cUL Certified Industrial PCBA
Enhanced Safety and Reliability
UL/cUL certified Industrial PCBAs undergo extensive testing and evaluation, resulting in products that are inherently safer and more reliable. This certification ensures that the PCBAs can withstand various environmental conditions, electrical stresses, and operational demands without compromising safety or performance. For industries such as automotive, aerospace, and medical devices, where reliability is paramount, certified PCBAs provide an additional layer of assurance.
Regulatory Compliance and Market Access
Many industries and regions require UL/cUL certification for Industrial PCBAs used in their products. By choosing certified assemblies, manufacturers can more easily comply with regulatory requirements and gain access to lucrative markets. This is particularly important for companies looking to expand their presence in North America, where UL/cUL certification is often mandatory for certain product categories.
Reduced Liability and Insurance Costs
Using UL/cUL certified Industrial PCBAs can significantly reduce liability risks for manufacturers and end-users. In the event of product-related incidents or failures, having certified components demonstrates due diligence and adherence to recognized safety standards. This can potentially lower insurance premiums and provide stronger legal protection in case of litigation.
Customer Trust and Brand Reputation
The UL/cUL mark on Industrial PCBAs serves as a symbol of quality and safety, enhancing customer trust and brand reputation. Many customers, especially in B2B scenarios, specifically seek out products with certified components due to their perceived reliability and compliance with industry standards. This can lead to increased sales, customer loyalty, and a competitive edge in the market.
Considerations for Non-Certified Industrial PCBA
Cost Implications
Non-certified Industrial PCBAs often come with a lower upfront cost, which can be attractive for budget-conscious projects or applications where certification is not mandatory. However, it's crucial to consider the potential long-term costs associated with using non-certified components, such as:
- Higher failure rates and replacement costs
- Potential redesign and recertification expenses if certification becomes necessary
- Increased liability and insurance costs
- Lost business opportunities in markets requiring certified components
Manufacturers must carefully weigh these factors against the initial cost savings when deciding between certified and non-certified Industrial PCBAs.
Limited Market Access and Regulatory Challenges
Using non-certified Industrial PCBAs can restrict market access, particularly in regions or industries where UL/cUL certification is mandatory. This limitation can hinder a company's growth potential and ability to compete in certain sectors. Additionally, non-certified PCBAs may face challenges in meeting regulatory requirements, potentially leading to delays in product launches or even product recalls.
Quality and Reliability Concerns
While not all non-certified Industrial PCBAs are of poor quality, the lack of third-party verification and ongoing compliance checks can lead to inconsistencies in manufacturing processes and material selection. This may result in:
- Higher variability in product performance
- Increased susceptibility to environmental factors
- Reduced lifespan and reliability
- Potential safety hazards in critical applications
For applications where failure is not an option, such as in medical devices or industrial control systems, these concerns can be significant drawbacks of using non-certified PCBAs.
Balancing Cost and Risk
The decision to use non-certified Industrial PCBAs often comes down to balancing cost savings against potential risks. In some cases, such as prototyping or low-volume production for non-critical applications, the use of non-certified PCBAs may be acceptable. However, for high-volume production, safety-critical applications, or products destined for regulated markets, the benefits of UL/cUL certification typically outweigh the initial cost savings of non-certified alternatives.
Conclusion
The choice between UL/cUL certified and non-certified Industrial PCBAs is a critical decision that can significantly impact product safety, reliability, and market success. While certified PCBAs offer numerous advantages in terms of quality assurance, regulatory compliance, and risk mitigation, non-certified options may be suitable for certain applications where certification is not mandatory or cost is a primary concern.
Ultimately, manufacturers must carefully evaluate their specific requirements, target markets, and risk tolerance when making this decision. By understanding the real differences between certified and non-certified PCBAs, companies can make informed choices that align with their business goals and product specifications.
Lead-Free Industrial PCBA Factory in Shenzhen, China | Ring PCB
Ring PCB Technology Co., Limited, your trusted PCB Manufacturing Partner since 2008, offers comprehensive one-stop services for PCB and PCBA. With our self-owned factory and full supply chain control, we ensure vertical integration from raw material procurement to production and testing. Our triple quality assurance system, including AOI, impedance testing, and thermal cycling, maintains a defect rate below 0.2%. We hold global certifications such as ISO9001, IATF16949, and RoHS compliance. Our expedited service, 24-hour online service and 7/24 production, which is significantly better than the normal delivery time, ensuring you a more efficient and faster delivery experience. For innovative, reliable, and cost-effective PCB&PCBA solutions tailored to diverse industries, contact us at [email protected].
References
1. Underwriters Laboratories. (2021). "UL 796: Printed-Wiring Boards." Standard for Safety.
2. Canadian Standards Association. (2020). "C22.2 No. 0.8: Safety Functions Incorporating Electronic Technology." CSA Group.
3. Industrial Automation Magazine. (2022). "The Impact of UL Certification on Industrial Control Panels." Volume 45, Issue 3.
4. Journal of Electronics Manufacturing. (2023). "Comparative Analysis of Certified vs. Non-Certified PCBAs in High-Reliability Applications." Volume 28, Issue 2.
5. International Electrotechnical Commission. (2021). "IEC 61010-1: Safety requirements for electrical equipment for measurement, control, and laboratory use." IEC Standard.
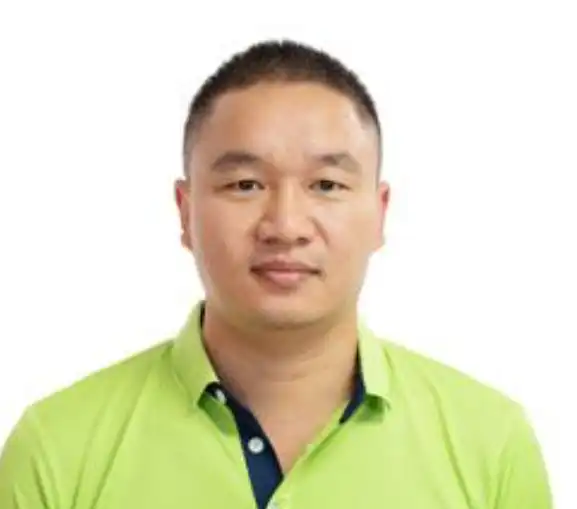
Welcome to Ring PCB! Share your inquiry, and receive a tailored quotation!

Ring PCB, your trusted partner for PCB & PCBA Full Turnkey Solutions