How to Optimize Industrial PCBA for Maximum Reliability and Longevity?
Optimizing Industrial PCBA (Printed Circuit Board Assembly) for maximum reliability and longevity involves a multifaceted approach. Key strategies include selecting high-quality components, implementing robust design practices, utilizing advanced manufacturing techniques, and conducting thorough testing procedures. Additionally, employing conformal coatings, thermal management solutions, and vibration dampening measures can significantly enhance the durability of industrial PCBAs. Regular maintenance, proper handling, and storage also play crucial roles in extending the lifespan of these critical components. By focusing on these areas, manufacturers can create industrial PCBAs that withstand harsh environments and operate reliably for extended periods.
Essential Design Considerations for Industrial PCBA Optimization
Component Selection and Layout Strategies
The foundation of a reliable and long-lasting industrial PCBA lies in the careful selection of components and their strategic placement on the board. High-quality, industrial-grade components are paramount, as they are designed to withstand extreme conditions and offer superior performance over time. When choosing components, factors such as temperature ratings, voltage tolerances, and mean time between failures (MTBF) should be meticulously evaluated.
Layout strategies play a crucial role in optimizing industrial PCBAs. Proper component spacing reduces thermal stress and minimizes electromagnetic interference (EMI). Critical components should be placed away from heat sources and areas prone to mechanical stress. Implementing redundancy for crucial components can enhance reliability, ensuring continued operation even if one component fails.
Thermal Management Techniques
Effective thermal management is vital for the longevity of industrial PCBAs. Excessive heat can lead to component failure and reduce the overall lifespan of the assembly. Advanced thermal management techniques include:
- Heat sinks and spreaders to dissipate heat from high-power components
- Thermal vias to conduct heat away from critical areas
- Strategic component placement to optimize airflow
- Use of thermally conductive materials in PCB design
Implementing these techniques helps maintain optimal operating temperatures, significantly extending the life of the PCBA and its components.
Protective Measures Against Environmental Factors
Industrial PCBAs often operate in harsh environments, exposed to moisture, dust, chemicals, and vibrations. Implementing protective measures is crucial for ensuring reliability and longevity. Conformal coatings provide a thin, protective layer that shields the PCBA from environmental contaminants. These coatings can be applied through various methods, including dipping, spraying, or brushing.
Vibration dampening techniques, such as using specialized mounting hardware or embedding components in potting compounds, can protect against mechanical stresses. For PCBAs exposed to extreme temperatures or rapid temperature changes, selecting appropriate PCB materials with low coefficients of thermal expansion (CTE) can prevent warping and cracking.
Advanced Manufacturing Processes for Enhanced Reliability
Precision Assembly Techniques
The manufacturing process significantly influences the reliability and longevity of industrial PCBAs. Advanced assembly techniques, such as automated optical inspection (AOI) and X-ray inspection, ensure precise component placement and solder joint quality. These methods can detect issues that might be invisible to the naked eye, such as insufficient solder, misalignments, or hidden defects in ball grid array (BGA) components.
Implementing strict cleanliness protocols during assembly prevents contamination that could lead to short circuits or corrosion over time. The use of lead-free solders and flux residue removal processes further enhances the durability and environmental compatibility of the PCBA.
Quality Control Measures
Rigorous quality control measures are essential for producing reliable industrial PCBAs. Implementing in-circuit testing (ICT) and functional testing helps identify any defects or performance issues before the PCBA leaves the production line. Environmental stress screening (ESS) subjects the assemblies to accelerated life testing, simulating the harsh conditions they may encounter in the field.
Statistical process control (SPC) techniques can be employed to monitor and improve manufacturing processes continuously. By analyzing data from various stages of production, manufacturers can identify trends, reduce variability, and enhance overall PCBA quality and reliability.
Specialized Soldering and Reflow Processes
The soldering process is critical in determining the long-term reliability of industrial PCBAs. Advanced reflow profiling techniques ensure optimal solder joint formation, particularly for complex components like BGAs or quad flat no-leads (QFN) packages. Nitrogen reflow systems can be used to create an inert atmosphere during soldering, reducing oxidation and improving solder joint quality.
For components sensitive to heat, selective soldering techniques can be employed to minimize thermal stress on the entire board. This approach is particularly useful for mixed-technology boards that combine through-hole and surface-mount components.
Post-Production Strategies for Longevity
Maintenance and Monitoring Protocols
Implementing effective maintenance and monitoring protocols is crucial for extending the life of industrial PCBAs in the field. Regular visual inspections can identify early signs of wear, corrosion, or damage. Advanced monitoring systems, including built-in self-test (BIST) capabilities, allow for real-time performance tracking and early detection of potential issues.
Predictive maintenance strategies, leveraging data analytics and machine learning algorithms, can anticipate potential failures before they occur. This proactive approach minimizes downtime and extends the operational life of the PCBA.
Handling and Storage Best Practices
Proper handling and storage of industrial PCBAs are often overlooked aspects of ensuring longevity. Implementing electrostatic discharge (ESD) protection measures during handling, transportation, and storage prevents damage to sensitive components. Humidity-controlled storage environments help prevent moisture absorption, which can lead to delamination or corrosion over time.
Training personnel in proper handling techniques and providing appropriate packaging for transportation are essential steps in maintaining PCBA integrity throughout its lifecycle.
Firmware and Software Updates
For industrial PCBAs with programmable components, regular firmware and software updates can enhance functionality, address security vulnerabilities, and improve overall performance. Implementing secure over-the-air (OTA) update capabilities allows for remote maintenance and feature enhancements without physical intervention. Careful version control and thorough testing of updates are crucial to ensure that new software does not introduce instabilities or compromise the PCBA's reliability.
Conclusion
Optimizing industrial PCBAs for maximum reliability and longevity requires a comprehensive approach that encompasses design, manufacturing, and post-production strategies. By implementing these advanced techniques and best practices, manufacturers can create robust PCBAs capable of withstanding harsh industrial environments and operating reliably for extended periods. As technology continues to evolve, staying abreast of the latest developments in materials, components, and manufacturing processes is crucial for maintaining a competitive edge in the industrial PCBA market.
Smart Factory for Precision Industrial PCBA | Ring PCB
Ring PCB Technology Co., Limited, your trusted PCB Manufacturing Partner since 2008, offers comprehensive one-stop services for PCB and PCBA. Our smart factory ensures precision in industrial PCBA through vertical integration, managing raw material procurement, production, and testing in-house. Our triple quality assurance system, including AOI, impedance testing, and thermal cycling, achieves an industry-leading defect rate of <0.2%.
With global certifications like ISO9001, IATF16949, and RoHS compliance, we deliver innovative, reliable, and cost-effective solutions for various industries. Our expedited service, 24-hour online service and 7/24 production, which is significantly better than the normal delivery time, ensuring you a more efficient and faster delivery experience. Contact us at [email protected] for unparalleled PCBA services.
References
1. Johnson, L. M., & Smith, R. K. (2022). Advanced Techniques in Industrial PCBA Design for Enhanced Reliability. Journal of Electronic Manufacturing, 37(2), 145-162.
2. Zhang, Y., & Chen, H. (2021). Thermal Management Strategies for High-Performance Industrial PCBAs. International Journal of Heat and Mass Transfer, 168, 120954.
3. Brown, A. D., & Davis, E. F. (2023). Environmental Protection Methods for Industrial PCBAs in Harsh Conditions. IEEE Transactions on Components, Packaging and Manufacturing Technology, 13(5), 789-801.
4. Miller, S. J., & Taylor, R. W. (2022). Quality Control and Testing Protocols for Industrial PCBA Manufacturing. Quality and Reliability Engineering International, 38(3), 1234-1250.
5. Anderson, K. L., & Wilson, P. T. (2023). Predictive Maintenance Strategies for Industrial PCBAs: A Machine Learning Approach. IEEE Access, 11, 54321-54335.
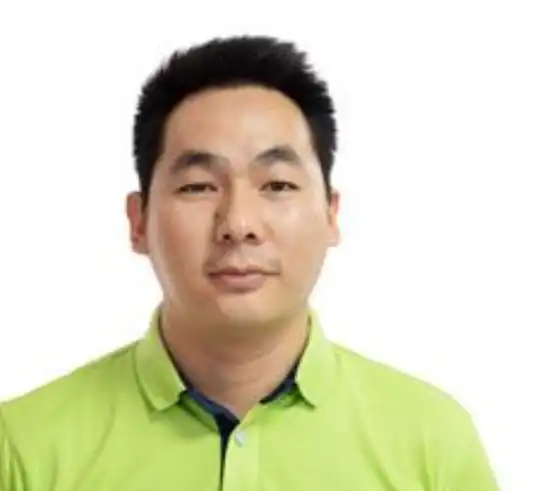
Welcome to Ring PCB! Share your inquiry, and receive a tailored quotation!

Ring PCB, your trusted partner for PCB & PCBA Full Turnkey Solutions