What are the key factors to consider in manufacturing PCBs for energy applications?
Manufacturing PCBs for energy applications requires careful consideration of several key factors to ensure optimal performance and reliability. These include material selection for high-temperature resistance and low dielectric loss, robust copper thickness for high current-carrying capacity, and appropriate thermal management strategies. Additionally, proper impedance control, EMI shielding, and adherence to safety standards are crucial. The PCB assembly process must also account for specialized components and unique design requirements specific to power and energy systems, ensuring longevity and efficiency in demanding environments.
Material Selection and Copper Thickness for Energy PCBs
High-Temperature Resistant Materials
When manufacturing PCBs for energy applications, selecting the right materials is paramount. Energy systems often operate in high-temperature environments, necessitating the use of substrates that can withstand thermal stress. Materials like polyimide and high-Tg (glass transition temperature) FR-4 are popular choices for their excellent thermal stability. These materials maintain their mechanical and electrical properties even under extreme heat, ensuring the longevity and reliability of the PCB assembly.
Low Dielectric Loss Materials
Energy applications frequently involve high-frequency operations, making low dielectric loss a critical factor. Materials with low dissipation factors minimize signal loss and heat generation, thereby improving overall system efficiency. Advanced laminates offer superior performance in this regard, making them ideal for power conversion and distribution circuits.
Copper Thickness and Current-Carrying Capacity
Energy PCBs often need to handle high currents, making copper thickness a crucial consideration. Standard 1 oz (35 µm) copper may be insufficient for many power applications. Instead, designers often opt for 2 oz (70 µm) or even 3 oz (105 µm) copper layers to increase current-carrying capacity and reduce heat generation. The PCB assembly process must be adapted to accommodate these thicker copper layers, ensuring proper etching and impedance control.
Thermal Management and Safety Considerations
Heat Dissipation Techniques
Effective thermal management is essential in energy PCBs to prevent overheating and ensure long-term reliability. Various techniques can be employed during the PCB assembly process to enhance heat dissipation:
1. Thermal vias: Arrays of vias filled with thermally conductive material help transfer heat from the surface to inner layers or the opposite side of the board.
2. Copper planes: Large copper areas act as heat spreaders, distributing heat more evenly across the board.
3. Component placement: Strategic positioning of heat-generating components to optimize airflow and heat distribution.
EMI Shielding
Energy systems often generate significant electromagnetic interference (EMI), which can affect both the PCB's performance and nearby electronics. Implementing effective EMI shielding during the PCB assembly process is crucial. This may involve:
1. Ground planes: Properly designed ground planes help contain electromagnetic fields.
2. Component shielding: Using shielded components or adding local shielding cans to sensitive areas.
3. Board-level shielding: Applying conductive coatings or incorporating shielding layers within the PCB stack-up.
Safety Standards Compliance
Energy PCBs must adhere to strict safety standards to ensure reliable and safe operation. This includes compliance with regulations such as UL 94 for flammability, IPC-6012 for qualification and performance of rigid PCBs, and industry-specific standards like those for automotive (ISO 26262) or renewable energy systems. The PCB assembly process should incorporate these requirements from the design phase through manufacturing and testing.
Specialized Components and Design Considerations
High-Power Components
Energy PCBs often incorporate specialized high-power components such as power MOSFETs, IGBTs, and large capacitors. These components require careful consideration during PCB assembly:
1. Footprint design: Ensuring adequate pad sizes and thermal relief for proper soldering and heat dissipation.
2. Mechanical stress: Accounting for the weight and potential vibration of large components to prevent solder joint fatigue.
3. Clearance and creepage: Maintaining proper spacing to prevent arcing and ensure electrical safety.
Impedance Control
While not always as critical as in high-speed digital applications, impedance control remains important in energy PCBs, particularly for control and sensing circuits. Proper impedance matching helps minimize signal reflections and ensures efficient power transfer. During PCB assembly, techniques such as controlled trace widths, reference plane design, and precise stackup management are employed to achieve the desired impedance characteristics.
Reliability Enhancement
Energy applications often demand extended operational lifetimes under harsh conditions. To enhance reliability, several strategies can be implemented during PCB assembly:
1. Conformal coating: Applying protective coatings to shield against moisture, dust, and chemical contaminants.
2. Stress relief: Incorporating design features like teardrop pads to reduce stress on solder joints.
3. Redundancy: Implementing redundant circuits or components for critical functions to improve fault tolerance.
Conclusion
Manufacturing PCBs for energy applications presents unique challenges that require careful consideration of materials, thermal management, safety standards, and specialized design techniques. By addressing these key factors during the PCB assembly process, manufacturers can produce robust, efficient, and reliable boards capable of meeting the demanding requirements of power and energy systems. As the energy sector continues to evolve, staying abreast of the latest PCB manufacturing technologies and best practices will be crucial for delivering high-performance solutions in this critical field.
Robust Stack-Up for Power & Energy PCBs | Ring PCB
Ring PCB Technology Co., Limited offers comprehensive one-stop PCB and PCBA services tailored for power and energy applications. With 17 years of expertise, we deliver innovative, reliable, and cost-effective solutions. Our integrated PCBA services include full assembly support, DFM/DFA optimization, and rigorous quality control, ensuring zero-defect delivery. Trust Ring PCB for your energy PCB needs. Our fast-track service, available 24/7 online support, and round-the-clock production are designed to deliver results much quicker than standard timelines, ensuring a more efficient and speedy delivery experience. Contact us at [email protected] to learn more about our tailored solutions.
References
1. Johnson, M. (2022). Advanced PCB Design Techniques for Power Electronics Applications. IEEE Transactions on Power Electronics, 37(4), 4122-4135.
2. Smith, A., & Brown, B. (2021). Thermal Management Strategies in High-Power PCB Design. Journal of Electronic Packaging, 143(2), 020901.
3. Lee, C., & Park, J. (2023). EMI Shielding Methods for Energy-Efficient PCB Assemblies. IEEE Electromagnetic Compatibility Magazine, 12(1), 78-85.
4. Wilson, R. (2022). Material Selection Criteria for PCBs in Renewable Energy Systems. Renewable and Sustainable Energy Reviews, 162, 112410.
5. Chen, H., & Wang, L. (2021). Reliability Enhancement Techniques for PCBs in Harsh Environment Applications. Microelectronics Reliability, 120, 114104.
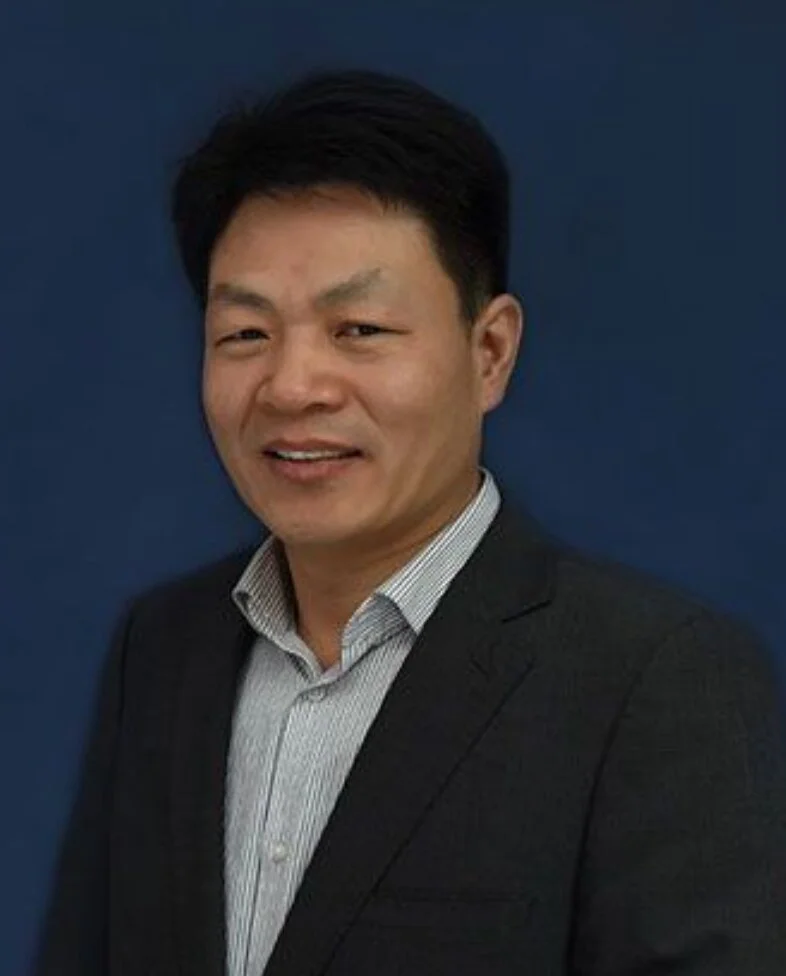
Welcome to Ring PCB! Share your inquiry, and receive a tailored quotation!

Ring PCB, your trusted partner for PCB & PCBA Full Turnkey Solutions