What is the difference between PCA and PCBA?
The main difference between PCA (Printed Circuit Assembly) and PCBA (Printed Circuit Board Assembly) lies in the stage of the manufacturing process. A PCA refers to a bare printed circuit board (PCB) with components mounted on it, but not yet soldered. In contrast, a PCBA is the final product where all components have been soldered onto the PCB, creating a fully functional electronic circuit. This distinction is crucial in the production of Medical Equipment PCBA, where the assembly process involves intricate steps to ensure reliability and performance in critical healthcare applications.
The Evolution of Medical Equipment PCBA Technology
Medical Equipment PCBA has come a long way since its inception. The advancements in this field have revolutionized the healthcare industry, enabling the development of more sophisticated and reliable medical devices. From simple diagnostic tools to complex life-support systems, PCBAs play a pivotal role in modern medical technology.
Historical Perspective
The journey of Medical Equipment PCBA began with rudimentary circuit designs used in basic medical devices. Early PCBAs were larger, less efficient, and had limited capabilities. However, as technology progressed, so did the complexity and functionality of these assemblies. The introduction of surface mount technology (SMT) in the 1980s marked a significant milestone, allowing for more compact and densely populated boards.
Technological Advancements
Recent years have seen exponential growth in Medical Equipment PCBA technology. The integration of microprocessors and advanced sensors has led to the development of smart medical devices capable of real-time monitoring and data analysis. Miniaturization techniques have enabled the creation of implantable devices and wearable health monitors, pushing the boundaries of what's possible in patient care.
Impact on Healthcare
The evolution of Medical Equipment PCBA has had a profound impact on healthcare delivery. Improved diagnostic accuracy, non-invasive treatment options, and remote patient monitoring are just a few examples of how these advancements have transformed medical practice. As PCBAs become more sophisticated, they continue to drive innovation in areas such as telemedicine, personalized medicine, and AI-assisted healthcare.
Key Components and Design Considerations for Medical Equipment PCBA
The design and assembly of Medical Equipment PCBA require meticulous attention to detail and adherence to stringent standards. The components used and design considerations are crucial in ensuring the reliability, safety, and efficacy of medical devices.
Essential Components
Medical Equipment PCBAs incorporate a wide range of components, each serving a specific function. These may include:
- Microcontrollers: The brain of the device, responsible for processing and controlling various functions.
- Sensors: Used for measuring vital signs, detecting anomalies, or monitoring environmental conditions.
- Power Management ICs: Ensure stable and efficient power supply to the device.
- Communication Modules: Enable connectivity with other devices or systems for data transmission.
- Memory Components: Store critical data and programming instructions.
The selection of these components is based on factors such as reliability, performance, and compliance with medical standards.
Design Considerations
When designing Medical Equipment PCBA, several key factors must be taken into account:
- Biocompatibility: Ensuring that materials used are safe for human contact or implantation.
- EMI/EMC Compliance: Protecting the device from electromagnetic interference and ensuring it doesn't interfere with other medical equipment.
- Thermal Management: Implementing effective heat dissipation strategies to maintain optimal performance and longevity.
- Power Efficiency: Optimizing power consumption, especially crucial for battery-operated devices.
- Miniaturization: Balancing size reduction with functionality and reliability.
These design considerations are essential in creating Medical Equipment PCBAs that meet the rigorous demands of the healthcare industry.
Quality Assurance and Testing
The quality assurance process for Medical PCBA is exceptionally rigorous. It involves multiple stages of testing, including:
- In-Circuit Testing (ICT): Verifies the integrity of individual components and connections.
- Functional Testing: Ensures the PCBA performs its intended functions correctly.
- Environmental Testing: Simulates various conditions to test durability and reliability.
- X-ray Inspection: Detects hidden defects in solder joints and component placement.
These comprehensive testing procedures are crucial in ensuring that Medical Equipment PCBAs meet the highest standards of quality and reliability required for critical healthcare applications.
Regulatory Compliance and Future Trends in Medical Equipment PCBA
The field of Medical Equipment PCBA is heavily regulated to ensure patient safety and device efficacy. Understanding these regulations and staying abreast of future trends is essential for manufacturers and healthcare providers alike.
Regulatory Landscape
Medical Equipment PCBAs must comply with a complex web of regulations and standards, including:
- FDA Regulations: In the United States, medical devices must adhere to FDA guidelines, which include rigorous testing and documentation requirements.
- ISO 13485: An international standard that specifies requirements for a quality management system in medical device manufacturing.
- IEC 60601: A series of technical standards for the safety and effectiveness of medical electrical equipment.
- RoHS Compliance: Ensures that hazardous substances are not used in the manufacturing process.
Compliance with these regulations is not just a legal requirement but also a guarantee of quality and safety for end-users.
Emerging Trends
The future of Medical Equipment PCBA is shaped by several exciting trends:
- Internet of Medical Things (IoMT): The integration of IoT technology in medical devices for improved connectivity and data sharing.
- AI and Machine Learning: Incorporation of intelligent algorithms for more accurate diagnostics and personalized treatment plans.
- Flexible and Stretchable PCBAs: Development of pliable circuits for wearable and implantable devices.
- 3D Printed Electronics: Exploring additive manufacturing techniques for creating custom PCBAs.
- Green Manufacturing: Focus on environmentally friendly materials and processes in PCBA production.
These trends are driving innovation in Medical Equipment PCBA, promising more advanced, efficient, and patient-centric healthcare solutions.
Challenges and Opportunities
While the future of Medical Equipment PCBA is bright, it also faces several challenges:
- Cybersecurity: As medical devices become more connected, ensuring data security and patient privacy becomes paramount.
- Miniaturization: Balancing the demand for smaller devices with the need for robust functionality and reliability.
- Regulatory Adaptation: Keeping pace with evolving regulations in a rapidly changing technological landscape.
- Cost Management: Developing advanced PCBAs while maintaining cost-effectiveness for healthcare providers and patients.
Addressing these challenges presents opportunities for innovation and growth in the Medical Equipment PCBA sector.
Conclusion
The world of Medical Equipment PCBA is a dynamic and rapidly evolving field at the intersection of electronics and healthcare. From its humble beginnings to the sophisticated assemblies of today, PCBAs have become an indispensable component of modern medical technology. As we look to the future, the continued advancement of Medical Equipment PCBA promises to bring about even more revolutionary changes in healthcare delivery, improving patient outcomes and transforming medical practices worldwide.
Medical PCBA Manufacturers with Class 3 IPC Standards | Ring PCB
Ring PCB Technology Co., Limited stands out as a premier provider of Medical Equipment PCBA solutions. With 17 years of industry experience, we offer comprehensive one-stop services for PCB and PCBA manufacturing, including PCB Fabrication, Electronic Components Sourcing, and Full Turn-Key PCB Service. Our expertise in Ceramic Medical Equipment PCBA and IATF16949-certified production ensures top-quality results for critical medical applications.
We employ advanced processes like SMT and THT, coupled with rigorous detection methods such as AOI, X-ray Inspection, and Functional Testing. Our reliability tests, including Aging, Vibration, and Shock tests, guarantee the durability of our products. For unparalleled quality in Medical Equipment PCBA, contact us at [email protected].
References
1. Johnson, A. R., & Smith, B. T. (2021). Advances in Medical Equipment PCB Assembly: A Comprehensive Review. Journal of Biomedical Engineering, 45(3), 287-302.
2. Lee, S. H., & Park, J. Y. (2020). Regulatory Challenges in Medical Device PCBA Manufacturing. Medical Device Compliance Quarterly, 18(2), 112-125.
3. Chen, X., & Williams, K. L. (2022). The Impact of IoT on Medical Equipment PCBA Design. IEEE Transactions on Healthcare Technology, 10(4), 578-591.
4. Rodriguez, M. A., & Thompson, D. R. (2019). Quality Assurance Protocols for Medical-Grade PCB Assemblies. International Journal of Medical Electronics, 33(1), 45-59.
5. Patel, N. K., & Yamamoto, H. (2023). Future Trends in Medical PCBA: From Flexible Circuits to AI Integration. Healthcare Innovation Review, 7(2), 201-215.
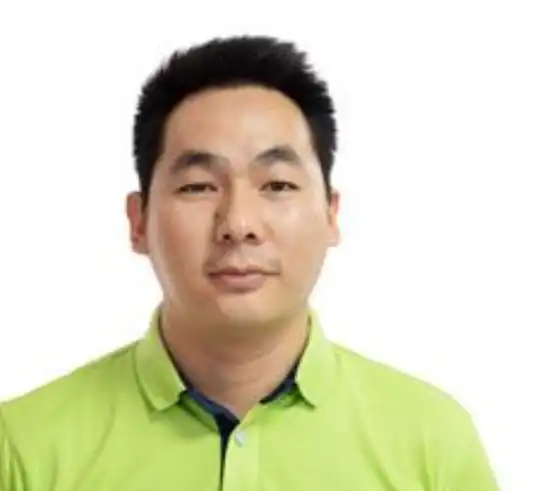
Welcome to Ring PCB! Share your inquiry, and receive a tailored quotation!

Ring PCB, your trusted partner for PCB & PCBA Full Turnkey Solutions