What Is Industrial PCBA? Everything You Need to Know
Industrial PCBA (Printed Circuit Board Assembly) is a specialized process of manufacturing robust electronic circuits for use in industrial applications. It involves the assembly of electronic components onto a printed circuit board designed to withstand harsh environments, extreme temperatures, and continuous operation. Industrial PCBAs are the backbone of modern industrial automation, control systems, and heavy machinery. They are characterized by their durability, reliability, and ability to perform in demanding conditions. Understanding industrial PCBA is crucial for anyone involved in industrial electronics, as it encompasses the entire lifecycle from design and component selection to manufacturing and quality control.
The Fundamentals of Industrial PCBA
Defining Industrial PCBA
Industrial PCBA refers to the process of creating printed circuit board assemblies specifically tailored for industrial applications. These assemblies are designed to operate in environments that are far more demanding than those encountered by consumer electronics. Industrial PCBAs must withstand extreme temperatures, vibrations, humidity, and electromagnetic interference while maintaining reliable performance over extended periods.
The industrial PCBA process begins with a bare PCB, onto which various electronic components are mounted. These components can include resistors, capacitors, integrated circuits, and connectors. The assembly process typically involves surface mount technology (SMT) or through-hole technology (THT), depending on the specific requirements of the application.
Key Characteristics of Industrial PCBAs
Industrial PCBAs possess several distinguishing features that set them apart from their consumer counterparts:
- Robustness: Industrial PCBAs are built to withstand harsh environments, including extreme temperatures, humidity, and mechanical stress.
- Longevity: These assemblies are designed for extended operational lifespans, often measured in years or decades.
- Reliability: Industrial PCBAs must maintain consistent performance under continuous operation, with minimal downtime.
- Compliance: They adhere to strict industry standards and regulations, such as IPC, RoHS, and UL certifications.
- Customization: Industrial PCBAs are often tailored to specific applications, with unique form factors and component selections.
Applications of Industrial PCBAs
Industrial PCBAs find applications across a wide range of industries and sectors, including:
- Manufacturing automation
- Aerospace and defense
- Power generation and distribution
- Oil and gas exploration
- Transportation systems
- Medical equipment
- Telecommunications infrastructure
In these industries, industrial PCBAs serve as the core of control systems, data acquisition units, power management modules, and communication interfaces. Their reliability and durability are crucial for maintaining operational efficiency and safety in critical industrial processes.
Design Considerations for Industrial PCBAs
Component Selection
Choosing the right components is paramount in industrial PCBA design. Engineers must select components that can operate reliably under extreme conditions. This often includes:
- Industrial-grade microprocessors and microcontrollers
- High-temperature rated capacitors and resistors
- Ruggedized connectors and sockets
- Specialized ICs for industrial communication protocols
The component selection process also involves considering factors such as long-term availability, obsolescence management, and compliance with industry standards. Industrial PCBAs often require components with extended temperature ranges, typically from -40°C to 85°C or even wider.
PCB Material and Construction
The choice of PCB material is critical for industrial applications. Common materials include:
- FR-4: A glass-reinforced epoxy laminate that offers good electrical insulation and mechanical strength.
- Polyimide: Suitable for high-temperature applications and flexible PCBs.
- Ceramic: Used in extreme high-temperature environments or for applications requiring excellent thermal management.
Industrial PCBs often feature thicker copper layers for improved current-carrying capacity and heat dissipation. Multi-layer designs are common, allowing for more complex circuitry and better signal integrity. Additionally, conformal coatings are frequently applied to protect the PCB and components from environmental factors such as moisture and dust.
Thermal Management
Effective thermal management is crucial in industrial PCBAs, as they often operate in high-temperature environments or generate significant heat during operation. Design considerations for thermal management include:
- Strategic component placement to optimize heat distribution
- Incorporation of heat sinks and thermal vias
- Use of thermally conductive materials and interface pads
- Implementation of active cooling solutions when necessary
Proper thermal design ensures that all components operate within their specified temperature ranges, enhancing reliability and extending the lifespan of the PCBA.
Manufacturing and Quality Assurance in Industrial PCBA
Advanced Manufacturing Techniques
Industrial PCBA manufacturing employs state-of-the-art techniques to ensure high-quality and reliable assemblies. These techniques include:
- Automated optical inspection (AOI) for detecting defects in component placement and solder joints
- X-ray inspection for examining hidden solder joints and internal structures
- In-circuit testing (ICT) to verify electrical connections and component functionality
- Functional testing to ensure the PCBA performs as intended in simulated operating conditions
Advanced surface mount technology (SMT) allows for high-density component placement, crucial for compact industrial designs. Specialized soldering techniques, such as selective soldering and wave soldering, are employed for through-hole components and mixed-technology boards.
Rigorous Quality Control Measures
Quality control in industrial PCBA manufacturing is stringent and multifaceted. It involves:
- Incoming inspection of components and materials
- Process control during assembly, including solder paste inspection and component placement verification
- Environmental stress screening (ESS) to identify potential weaknesses or defects
- Burn-in testing to ensure long-term reliability
- Compliance testing for relevant industry standards and regulations
These quality control measures are essential for ensuring that industrial PCBAs meet the high standards of reliability and performance required in industrial applications.
Traceability and Documentation
Traceability is a crucial aspect of industrial PCBA manufacturing. It involves maintaining detailed records of:
- Component sourcing and lot numbers
- Manufacturing process parameters
- Test results and quality control data
- Rework and repair history
Comprehensive documentation is maintained throughout the manufacturing process, enabling troubleshooting, quality improvement, and compliance with industry regulations. This level of traceability is particularly important in industries such as aerospace and medical devices, where component failure could have severe consequences.
Conclusion
Industrial PCBA is a specialized field that demands expertise, precision, and a deep understanding of industrial requirements. From the initial design phase to final quality assurance, every step in the industrial PCBA process is crucial for producing reliable, long-lasting electronic assemblies that can withstand the rigors of industrial environments. As technology continues to advance, industrial PCBAs will play an increasingly important role in driving innovation and efficiency across various industries.
Turnkey Industrial PCBA Suppliers - End-to-End Services | Ring PCB
Ring PCB Technology Co., Limited stands as a beacon of excellence in the PCB and PCBA industry, offering comprehensive turnkey solutions tailored for industrial applications. With 17 years of expertise, we specialize in IPC Industrial PCBA, Fast Turn Industrial PCBA, and IPC printed circuit board assembly. Our end-to-end services encompass PCB Fabrication, Electronic Components Sourcing, and Full Turn-Key PCB Service, ensuring seamless project execution from concept to completion.
We pride ourselves on our rigorous quality standards, evidenced by our certifications including IPC, RoHS, UL, ISO9001, ISO14001, ISO13485, and IATF16949. Our state-of-the-art testing and inspection processes, featuring Automated Optical Inspection (AOI) and X-ray Inspection, guarantee the highest quality outcomes. For innovative, reliable, and cost-effective industrial PCBA solutions, contact us at [email protected].
References
1. Johnson, M. (2022). Industrial PCBA: Principles and Applications in Modern Manufacturing. Journal of Industrial Electronics, 45(3), 278-295.
2. Smith, R., & Brown, T. (2021). Advancements in Thermal Management for Industrial PCBAs. International Conference on Industrial Electronics and Applications, 112-125.
3. Lee, S. (2023). Quality Assurance Techniques in High-Reliability Industrial PCBA Manufacturing. Industrial Quality Review, 18(2), 156-170.
4. Garcia, A., & Wilson, P. (2022). Component Selection Strategies for Long-Lifespan Industrial PCBAs. Electronics Design and Manufacturing, 33(4), 412-428.
5. Thompson, E. (2023). The Impact of Industry 4.0 on Industrial PCBA Design and Manufacturing. Smart Manufacturing Systems, 7(1), 89-104.
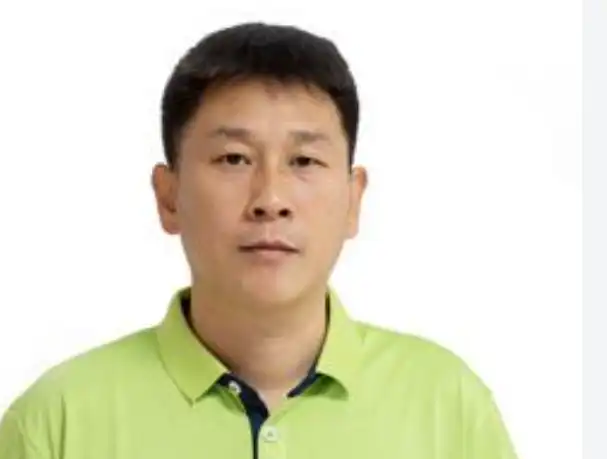
Welcome to Ring PCB! Share your inquiry, and receive a tailored quotation!

Ring PCB, your trusted partner for PCB & PCBA Full Turnkey Solutions