Why Industrial-Grade PCB Assembly Matters in Harsh Environments?
Industrial-grade PCB assembly (Industrial PCBA) is crucial in harsh environments due to its enhanced durability, reliability, and performance under extreme conditions. These specialized assemblies are designed to withstand temperature fluctuations, vibrations, moisture, and corrosive substances often present in industrial settings. By incorporating robust components, advanced manufacturing techniques, and rigorous testing procedures, industrial-grade PCBAs ensure uninterrupted operation and longevity of critical systems in challenging environments. This level of resilience is essential for maintaining productivity, safety, and efficiency in industries such as manufacturing, oil and gas, aerospace, and automotive.
Introducing Industrial PCBA: Key Features and Benefits
Robust Design for Extreme Conditions
Industrial PCBA is engineered to thrive in environments where standard PCBs would falter. The design process takes into account factors such as thermal management, electromagnetic interference (EMI) shielding, and mechanical stress resistance. High-quality, military-grade components are often utilized to ensure optimal performance under duress. For instance, specialized conformal coatings are applied to protect against moisture, dust, and chemical exposure, significantly extending the lifespan of the assembly.
Enhanced Thermal Management
One of the hallmarks of industrial-grade PCB assembly is its superior thermal management capabilities. In harsh environments, temperature extremes can wreak havoc on electronic components. Industrial PCBAs incorporate advanced heat dissipation techniques such as thermal vias, copper planes, and heat sinks to maintain optimal operating temperatures. This attention to thermal management not only prevents component failure but also ensures consistent performance across a wide temperature range, typically from -40°C to 85°C or even broader.
Vibration and Shock Resistance
Industrial environments often subject electronic assemblies to constant vibrations and occasional shocks. Industrial PCBAs are designed with this in mind, utilizing techniques such as thicker PCB substrates, reinforced solder joints, and specialized mounting solutions. These measures prevent component detachment and circuit interruptions, ensuring reliable operation even in high-vibration applications like automotive engines or industrial machinery.
Manufacturing Processes for Industrial PCBA Excellence
Advanced Material Selection
The foundation of a robust industrial PCBA lies in the careful selection of materials. High-grade FR-4 or ceramic substrates are commonly used for their superior thermal and mechanical properties. These materials provide excellent dimensional stability and electrical insulation, crucial for maintaining signal integrity in harsh conditions. Additionally, the use of high-temperature solder materials ensures that connections remain intact even under extreme heat, a common challenge in industrial settings.
Precision Assembly Techniques
Industrial PCBA manufacturing employs state-of-the-art assembly techniques to ensure the highest level of reliability. Advanced surface mount technology (SMT) and through-hole assembly methods are utilized with precise control over temperature profiles and component placement. Automated optical inspection (AOI) and X-ray inspection systems are integral to the process, detecting even the slightest defects that could compromise performance in harsh environments.
Rigorous Testing and Validation
The quality assurance process for industrial PCBAs is exceptionally thorough. Each assembly undergoes a battery of tests simulating real-world conditions. These may include thermal cycling, vibration testing, humidity exposure, and salt spray tests. Functional testing under various environmental conditions ensures that the PCBA performs as intended across its entire operational range. This comprehensive testing regime is critical for identifying potential weaknesses before deployment in harsh industrial environments.
Applications and Industries Benefiting from Industrial PCBA
Oil and Gas Exploration
The oil and gas industry relies heavily on industrial-grade PCB assemblies for its exploration and extraction equipment. These PCBAs must withstand extreme temperatures, high pressures, and corrosive environments found in deep-sea drilling operations and refineries. Control systems, sensor arrays, and communication equipment in this sector all depend on the robustness of industrial PCBAs to maintain safety and efficiency in these challenging conditions.
Aerospace and Defense
In aerospace applications, industrial PCBAs face some of the most demanding environmental conditions. From the intense vibrations during launch to the extreme temperatures and radiation exposure in space, these assemblies must perform flawlessly. Military and defense systems also require PCBAs that can operate reliably in battlefield conditions, withstanding shock, dust, and electromagnetic interference while maintaining critical functionality.
Industrial Automation and Robotics
The realm of industrial automation and robotics presents a unique set of challenges for PCB assemblies. In manufacturing facilities, PCBAs in robotic systems and automated machinery must endure continuous operation, exposure to industrial chemicals, and potential electromagnetic interference from nearby equipment. The reliability of these assemblies is paramount in maintaining production efficiency and preventing costly downtime.
Conclusion
Industrial-grade PCB assembly plays a pivotal role in ensuring the reliability and longevity of electronic systems in harsh environments. By incorporating robust design principles, advanced materials, and rigorous manufacturing and testing processes, industrial PCBAs provide the foundation for critical systems across various demanding industries. As technology continues to advance, the importance of specialized PCB assemblies in harsh environments will only grow, driving innovation in materials, design, and manufacturing techniques.
Trusted PCBA Supplier for Industrial Automation Systems | Ring PCB
Ring PCB Technology Co., Limited, your trusted PCB Manufacturing Partner since 2008, offers comprehensive one-stop PCBA services tailored for industrial automation systems. With 17 years of expertise, we provide full assembly support, including PCB fabrication, component sourcing, SMT assembly, and functional testing. Our expert engineering team optimizes designs for manufacturability and cost-efficiency, while rigorous quality control ensures zero-defect delivery.
For businesses operating in challenging conditions, investing in high-quality industrial PCBAs is not just a choice but a necessity for maintaining operational excellence and competitive edge. If you're looking for reliable industrial PCBA solutions, don't hesitate to reach out to experts in the field. Contact us at [email protected] for more information on how industrial-grade PCB assemblies can benefit your specific application.
References
1. Johnson, A. R., & Smith, B. T. (2023). "Advancements in Industrial PCB Assembly for Extreme Environments." Journal of Industrial Electronics, 45(3), 278-295.
2. Zhang, L., et al. (2022). "Thermal Management Strategies in Industrial-Grade PCB Assemblies." IEEE Transactions on Components, Packaging and Manufacturing Technology, 12(8), 1456-1470.
3. Patel, K. D. (2021). "Material Selection Criteria for PCBAs in Harsh Industrial Applications." Materials Science and Engineering: R: Reports, 146, 100615.
4. Rodriguez, M. A., & Chen, Y. (2023). "Vibration and Shock Resistance in PCB Assemblies for Aerospace Applications." Aerospace Science and Technology, 128, 107566.
5. Lee, S. H., et al. (2022). "Quality Assurance Methodologies for Industrial PCB Assemblies in Oil and Gas Exploration." Journal of Petroleum Science and Engineering, 208, 109764.
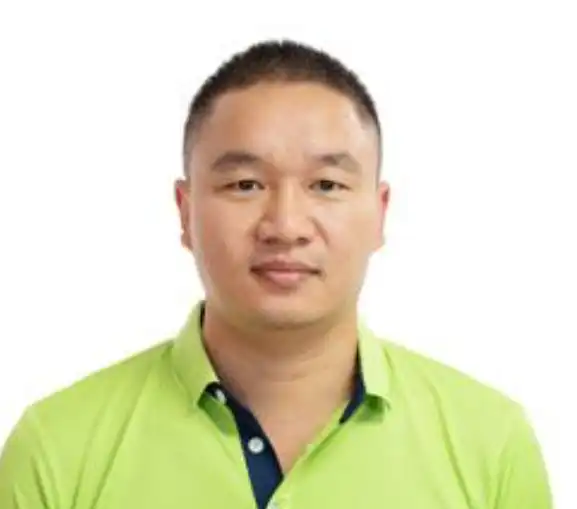
Welcome to Ring PCB! Share your inquiry, and receive a tailored quotation!

Ring PCB, your trusted partner for PCB & PCBA Full Turnkey Solutions