How to Meet ISO 13485 PCBA Requirements for Medical Devices?
Meeting ISO 13485 PCBA requirements for medical devices involves implementing a robust quality management system, ensuring traceability throughout the manufacturing process, and adhering to strict documentation practices. Manufacturers must focus on risk management, design controls, and validation of processes. Rigorous supplier management, contamination control, and thorough testing procedures are essential. Continuous monitoring, analysis, and improvement of the PCBA process are crucial to maintain compliance. By prioritizing these aspects, medical device manufacturers can successfully meet ISO 13485 standards for their medical device PCBA production.
Understanding ISO 13485 and Its Importance in Medical Device PCBA
ISO 13485 is a crucial standard for medical device manufacturers, particularly those involved in medical device PCBA (Printed Circuit Board Assembly). This internationally recognized standard sets the bar for quality management systems in the medical device industry, ensuring that products meet regulatory requirements and customer expectations.
The Scope of ISO 13485 in Medical Device Manufacturing
ISO 13485 covers various aspects of medical device production, including design, development, production, installation, and servicing. For medical device PCBA, this standard is particularly relevant as it addresses the intricate process of assembling electronic components onto printed circuit boards for use in medical devices. The standard emphasizes the importance of maintaining consistency, traceability, and quality throughout the PCBA process.
Key Benefits of ISO 13485 Compliance for Medical Device PCBA
Adhering to ISO 13485 offers numerous advantages for manufacturers engaged in medical device PCBA:
- Enhanced product safety and reliability
- Improved risk management practices
- Increased customer confidence and satisfaction
- Streamlined regulatory compliance processes
- Better documentation and traceability
- Continuous improvement of quality management systems
By implementing ISO 13485 standards, PCBA manufacturers can ensure their medical devices meet the highest quality and safety standards, ultimately contributing to better patient outcomes and reduced liability risks.
Essential Steps to Achieve ISO 13485 Compliance in Medical Device PCBA
Achieving ISO 13485 compliance for medical device PCBA requires a systematic approach and attention to detail. Here are the essential steps manufacturers should follow:
Establishing a Robust Quality Management System
The foundation of ISO 13485 compliance is a well-structured quality management system (QMS). For medical device PCBA, this system should encompass all aspects of the production process, from component sourcing to final assembly and testing. Key elements include:
- Clearly defined roles and responsibilities
- Documented procedures for all critical processes
- Regular internal audits and management reviews
- Effective corrective and preventive action (CAPA) processes
- Comprehensive training programs for all personnel
Implementing Rigorous Design and Development Controls
Medical device PCBA often involves complex designs that must meet stringent performance and safety requirements. ISO 13485 mandates robust design and development controls, including:
- Thorough design planning and review processes
- Detailed design inputs and outputs documentation
- Verification and validation of design results
- Proper management of design changes and transfers
- Maintenance of design history files
Ensuring Traceability and Documentation Throughout the PCBA Process
Traceability is paramount in medical device PCBA. ISO 13485 requires manufacturers to maintain comprehensive documentation and implement systems that allow for complete traceability of components, processes, and personnel involved in production. This includes:
- Unique identification of all components and assemblies
- Detailed process records for each production batch
- Documentation of equipment calibration and maintenance
- Personnel training and qualification records
- Supplier evaluation and management documentation
Advanced Techniques for Maintaining ISO 13485 Compliance in Medical Device PCBA
Maintaining ISO 13485 compliance for medical device PCBA requires ongoing effort and the adoption of advanced techniques. Here are some strategies to ensure continued compliance and quality:
Leveraging Technology for Enhanced Quality Control
Advanced technology plays a crucial role in maintaining ISO 13485 compliance for medical device PCBA. Manufacturers can leverage various tools and techniques to enhance quality control:
- Automated Optical Inspection (AOI) systems for detecting defects
- X-ray inspection for identifying hidden solder joint issues
- In-circuit testing (ICT) for verifying component placement and functionality
- Environmental stress screening (ESS) to identify potential failures
- Statistical Process Control (SPC) for monitoring and improving processes
Implementing Continuous Improvement Processes
ISO 13485 emphasizes the importance of continuous improvement in quality management systems. For medical PCBA, this involves:
- Regular analysis of quality data and performance metrics
- Conducting root cause analyses for identified issues
- Implementing preventive actions to address potential problems
- Encouraging employee feedback and suggestions for improvement
- Staying updated with industry best practices and technological advancements
Ensuring Supplier Quality Management
The quality of medical device PCBA is heavily dependent on the components used. ISO 13485 requires robust supplier management processes, including:
- Thorough supplier evaluation and selection procedures
- Regular supplier audits and performance reviews
- Clear communication of quality requirements to suppliers
- Implementing incoming inspection procedures for received components
- Maintaining records of supplier qualifications and performance
By implementing these advanced techniques, manufacturers can not only meet ISO 13485 requirements but also exceed them, ensuring the highest quality standards for their medical device PCBA products.
Conclusion
Meeting ISO 13485 requirements for medical device PCBA is a complex but essential process for manufacturers in the medical device industry. By implementing robust quality management systems, rigorous design controls, and advanced quality assurance techniques, companies can ensure their PCBAs meet the highest standards of safety and reliability. Continuous improvement and a commitment to quality are key to maintaining compliance and delivering superior medical devices.
Top Medical Device PCBA Suppliers - Ultra-Low Defect Rate | Ring PCB
Ring PCB Technology Co., Limited, your trusted PCB Manufacturing Partner since 2008, offers comprehensive one-stop PCBA services for medical equipment. Our expert team provides full assembly support, including PCB fabrication, component sourcing, SMT assembly, and functional testing. We excel in DFM/DFA optimization, reducing design risks and BOM costs. Our rigorous quality control process, featuring X-ray inspection, AOI testing, and 100% functional validation, ensures ultra-low defect rates. With 17 years of excellence in PCB&PCBA solutions, we cater to diverse industries, including medical. For expert guidance on ISO 13485 compliance and high-quality medical device PCBA manufacturing, contact Ring PCB at [email protected].
References
1. International Organization for Standardization. (2016). ISO 13485:2016 Medical devices — Quality management systems — Requirements for regulatory purposes.
2. U.S. Food and Drug Administration. (2018). Quality System (QS) Regulation/Medical Device Good Manufacturing Practices.
3. Speer, J. K. (2017). Medical Device Manufacturing: Complying with ISO 13485:2016. Quality Magazine.
4. IPC - Association Connecting Electronics Industries. (2020). IPC-A-610 Acceptability of Electronic Assemblies.
5. Theisz, V. (2016). Medical Device Regulatory Practices: An International Perspective. CRC Press.
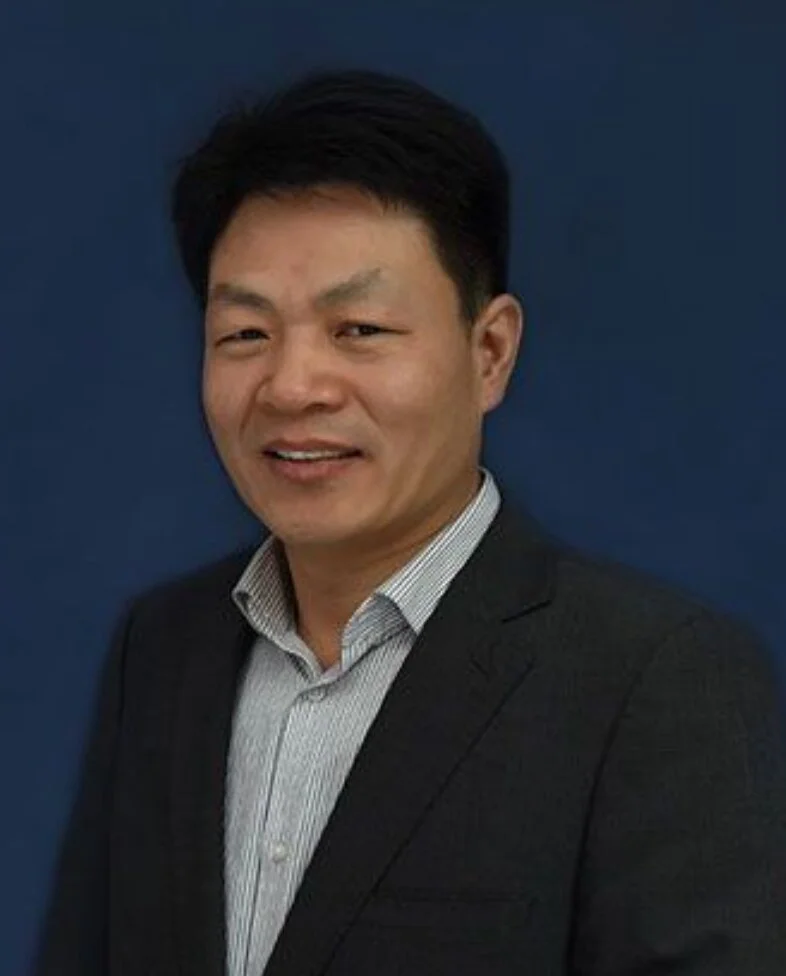
Welcome to Ring PCB! Share your inquiry, and receive a tailored quotation!

Ring PCB, your trusted partner for PCB & PCBA Full Turnkey Solutions