Is PCB assembly hard?
PCB assembly, while complex, is not inherently hard for those with the right knowledge, equipment, and experience. It involves intricate processes like component placement, soldering, and testing, which can be challenging for beginners. However, with proper training, advanced machinery, and quality control measures, PCB assembly becomes a manageable and precise operation. The difficulty level varies depending on the complexity of the design, component density, and required precision. For hobbyists or small-scale producers, it may present a steeper learning curve, but for professional manufacturers with automated systems, PCB assembly is a streamlined, efficient process.
The Intricacies of PCB Assembly Process
Component Preparation and Placement
The PCB assembly process begins with meticulous component preparation. This involves sorting, organizing, and often pre-forming leads of through-hole components. Surface-mount technology (SMT) has revolutionized this step, allowing for smaller, more densely packed boards. However, the challenge lies in the precise placement of these miniature components.
Modern assembly lines utilize pick-and-place machines, which can accurately position components at high speeds. These machines use computer vision and robotic arms to place components as small as 0201 (0.6 mm × 0.3 mm) or even 01005 (0.4 mm × 0.2 mm) with remarkable accuracy. The difficulty here is not in the placement itself, but in programming and maintaining these sophisticated machines to ensure consistent performance.
Soldering Techniques and Challenges
Soldering is a crucial step in PCB assembly, forming electrical connections and mechanically securing components to the board. Various soldering methods are employed, each with its own set of challenges:
- Reflow Soldering: Used for SMT components, this method requires precise control of temperature profiles to avoid component damage or poor solder joints.
- Wave Soldering: Typically used for through-hole components, this process can be tricky when dealing with mixed-technology boards.
- Selective Soldering: Useful for boards with a mix of SMT and through-hole components, but requires careful programming to avoid thermal damage.
The difficulty in soldering lies in managing heat distribution, preventing solder bridges, and ensuring consistent solder joint quality across thousands of connections. Factors like board warpage, component tolerances, and solder paste chemistry all play crucial roles in the success of this step.
Quality Control and Testing
The final phase of PCB assembly involves rigorous quality control and testing. This step is critical in ensuring the functionality and reliability of the assembled PCB. Common inspection and testing methods include:
- Automated Optical Inspection (AOI): Uses high-resolution cameras to detect defects like misaligned components or solder bridges.
- X-ray Inspection: Particularly useful for inspecting hidden solder joints in ball grid array (BGA) components.
- In-Circuit Testing (ICT): Checks for shorts, opens, and component values.
- Functional Testing: Verifies the overall functionality of the assembled PCB.
The challenge here is in developing comprehensive test protocols that can quickly and accurately identify defects without false positives. As PCB designs become more complex, with higher component densities and multi-layer structures, the testing process becomes increasingly sophisticated and crucial.
Factors Influencing PCB Assembly Complexity
Board Design and Component Density
The complexity of PCB assembly is heavily influenced by the board's design and component density. High-density interconnect (HDI) boards, with their fine traces and microvias, require extreme precision in component placement and soldering. As the number of components per unit area increases, so does the difficulty of assembly.
Multi-layer boards present additional challenges, as they require careful alignment of layers and management of thermal dissipation during assembly. The trend towards miniaturization in electronics continually pushes the boundaries of what's possible in PCB assembly, necessitating ever-more sophisticated assembly techniques.
Component Types and Technologies
The variety of component types used in modern PCBs adds another layer of complexity to the assembly process. Some challenging components include:
- Ball Grid Array (BGA) components: Require precise placement and often need X-ray inspection to verify solder joint quality.
- Quad Flat No-leads (QFN) packages: Challenging to solder due to their lack of visible leads.
- Fine-pitch components: Demand extremely accurate placement to avoid shorts between adjacent pins.
- Flexible and rigid-flex PCBs: Require special handling and assembly techniques to maintain flexibility.
Each component type may require different soldering profiles, placement techniques, and inspection methods, adding to the overall complexity of the assembly process.
Environmental and Regulatory Considerations
PCB assembly is not just about putting components on a board; it's also about meeting various environmental and regulatory standards. These considerations can significantly impact the difficulty of the assembly process:
- RoHS Compliance: Requires lead-free solders, which have higher melting points and can be more challenging to work with.
- Electrostatic Discharge (ESD) Protection: Necessitates special handling procedures and equipment throughout the assembly process.
- Thermal Management: Increasingly important in high-power applications, requiring careful consideration of component placement and heat dissipation.
- Conformal Coating: Often used for protection against moisture and contaminants, adding an extra step to the assembly process.
Adhering to these standards while maintaining high-quality assembly outcomes requires specialized knowledge and often additional process steps, increasing the overall complexity of PCB assembly.
Overcoming PCB Assembly Challenges
Advanced Manufacturing Technologies
To address the increasing complexity of PCB assembly, manufacturers are turning to advanced technologies:
- 3D Solder Paste Inspection (SPI): Ensures correct solder paste deposition before component placement.
- Automated X-ray Inspection (AXI): Provides non-destructive inspection of hidden solder joints.
- Laser-guided component placement: Improves accuracy for ultra-fine-pitch components.
- Artificial Intelligence in AOI systems: Enhances defect detection and reduces false positives.
These technologies not only improve the precision and reliability of PCB assembly but also help in managing the complexity of modern board designs.
Design for Manufacturing (DFM) Principles
Implementing DFM principles is crucial in simplifying PCB assembly. This approach involves:
- Optimizing component placement for efficient assembly
- Designing adequate spacing between components to facilitate automated placement and soldering
- Considering thermal management in the initial design phase
- Standardizing component packages where possible to streamline the assembly process
By incorporating DFM principles early in the design process, many potential assembly difficulties can be mitigated or eliminated entirely.
Continuous Training and Process Improvement
The dynamic nature of PCB technology necessitates ongoing training and process improvement:
- Regular operator training on new equipment and techniques
- Implementing statistical process control to identify and address issues proactively
- Engaging in industry forums and collaborations to stay abreast of best practices
- Continuous refinement of assembly processes based on data analysis and feedback
By fostering a culture of continuous improvement, PCB assembly facilities can better adapt to new challenges and maintain high-quality standards.
Conclusion
While PCB assembly presents numerous challenges, it is not insurmountably difficult with the right approach, tools, and expertise. The complexity of modern PCB designs, coupled with stringent quality and regulatory requirements, does make assembly a sophisticated process. However, through the application of advanced technologies, adherence to DFM principles, and a commitment to continuous improvement, these challenges can be effectively managed. For those looking to navigate the intricacies of PCB assembly, partnering with experienced manufacturers can significantly ease the process.
Professional guidance & smart factory ensure smooth PCBA | Ring PCB
Ring PCB Technology Co., Limited, your trusted PCB Manufacturing Partner since 2008, offers comprehensive one-stop PCB and PCBA services. With 17 years of excellence, we deliver innovative, reliable, and cost-effective solutions for electronics, automotive, aerospace, medical, and telecommunications industries. Our state-of-the-art Shenzhen factory, equipped with advanced SMT lines and testing equipment, ensures high-quality, customized PCBA solutions. From multi-layer designs to high-power supply PCBAs, we provide tailored services to meet your exact requirements. Partner with Ring PCB for unparalleled expertise in PCB assembly.
Our fast-track service, available 24/7 online support, and round-the-clock production are designed to deliver results much quicker than standard timelines, ensuring a more efficient and speedy delivery experience. If you're seeking expert guidance in PCB assembly, feel free to reach out to us at [email protected] for professional assistance tailored to your specific needs
References
1. Prasad, R. P. (2013). Surface Mount Technology: Principles and Practice. Springer Science & Business Media.
2. Coombs, C. F. (2008). Printed Circuits Handbook. McGraw-Hill Education.
3. Judd, M., & Brindley, K. (2012). Soldering in Electronics Assembly. Newnes.
4. Schroeder, C., Giesler, J., & Sissons, B. (2014). Advances in Electronic Assembly Materials and Processes. IPC APEX EXPO Proceedings.
5. Lee, N. C. (2002). Reflow Soldering Processes and Troubleshooting: SMT, BGA, CSP, and Flip Chip Technologies. Newnes.
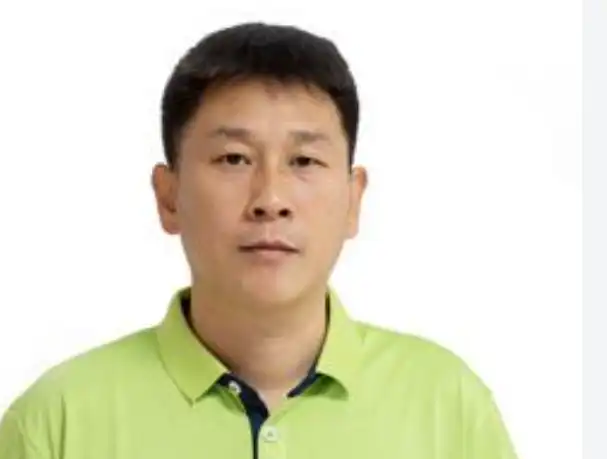
Welcome to Ring PCB! Share your inquiry, and receive a tailored quotation!

Ring PCB, your trusted partner for PCB & PCBA Full Turnkey Solutions