Medical PCBA Manufacturing Costs: What to Expect
Medical PCBA (Printed Circuit Board Assembly) manufacturing costs can vary significantly based on factors such as design complexity, component selection, and production volume. Generally, medical PCBAs are more expensive than standard PCBAs due to stringent quality requirements and regulatory compliance. Costs typically range from $50 to $500 per board for low to medium volumes, with high-end medical devices potentially exceeding $1000 per PCBA. Factors influencing costs include specialized components, rigorous testing procedures, and adherence to medical industry standards. To optimize costs, manufacturers often focus on efficient design, strategic component sourcing, and scalable production processes.
Factors Influencing Medical PCBA Manufacturing Costs
Design Complexity and Component Selection
The intricacy of medical PCBA designs plays a crucial role in determining manufacturing costs. Complex designs with multiple layers, high-density interconnects, and advanced features like microvia technology tend to be more expensive to produce. Additionally, the selection of components significantly impacts the overall cost. Medical-grade components, which are often required for reliability and compliance reasons, can be substantially more expensive than their commercial counterparts.
For instance, specialized sensors, microcontrollers, and power management ICs designed for medical applications come with a premium price tag. These components undergo rigorous testing and certification processes to ensure they meet the stringent requirements of the medical industry. The use of such components not only increases the bill of materials (BOM) cost but also necessitates more sophisticated assembly techniques, further driving up manufacturing expenses.
Regulatory Compliance and Quality Assurance
Medical PCBAs are subject to strict regulatory standards, including FDA regulations and ISO 13485 certification requirements. Compliance with these standards involves extensive documentation, traceability measures, and quality control processes throughout the manufacturing cycle. These additional steps and requirements contribute significantly to the overall cost of production.
Quality assurance for medical PCBAs is particularly rigorous, often involving 100% inspection and testing of assembled boards. Advanced testing equipment, such as automated optical inspection (AOI) systems and X-ray inspection machines, are employed to detect even the smallest defects. The implementation of these quality control measures, while essential for ensuring patient safety and device reliability, adds to the manufacturing costs.
Production Volume and Economies of Scale
The production volume of medical PCBAs has a substantial impact on per-unit costs. Low-volume production, which is common in the medical device industry due to specialized applications, tends to have higher per-unit costs. This is because the initial setup costs, including tooling and programming of assembly equipment, are spread across fewer units.
Conversely, higher production volumes can lead to economies of scale, reducing the per-unit cost. Manufacturers can negotiate better prices for components when purchasing in larger quantities and can optimize their production lines for efficiency. However, even with larger volumes, medical PCBAs typically remain more expensive than consumer electronics PCBAs due to the aforementioned factors of component quality and regulatory compliance.
Strategies for Cost Optimization in Medical PCBA Manufacturing
Design for Manufacturability (DFM)
Implementing Design for Manufacturability principles can significantly reduce manufacturing costs without compromising quality or functionality. DFM involves optimizing the PCB layout and component placement to simplify the assembly process, reduce the likelihood of errors, and improve yield rates. Some key DFM considerations for medical PCBAs include:
- Standardizing component packages to reduce the number of unique parts
- Ensuring adequate spacing between components for ease of assembly and rework
- Optimizing trace routing to minimize the number of layers required
- Incorporating test points for efficient in-circuit testing
By addressing these aspects during the design phase, manufacturers can streamline the production process, reduce assembly time, and minimize the risk of costly errors or rework.
Strategic Component Sourcing
Effective component sourcing strategies can lead to substantial cost savings in medical PCBA manufacturing. While it's crucial to maintain the high quality standards required for medical devices, there are several approaches to optimize component costs:
- Partnering with reliable suppliers who specialize in medical-grade components
- Exploring alternative components that meet or exceed the required specifications
- Implementing a just-in-time (JIT) inventory system to reduce carrying costs
- Negotiating volume discounts for frequently used components
Additionally, working closely with component manufacturers can provide insights into upcoming technologies or components that may offer better performance at a lower cost. This proactive approach to component selection can lead to long-term cost benefits and improved product performance.
Automated Assembly and Testing
Investing in automated assembly and testing equipment can significantly reduce labor costs and improve consistency in medical PCBA manufacturing. While the initial investment in such equipment can be substantial, the long-term benefits often outweigh the costs, particularly for medium to high-volume production.
Automated assembly lines equipped with pick-and-place machines, reflow ovens, and robotic systems can dramatically increase throughput while maintaining high precision. Similarly, automated testing systems, including in-circuit testers (ICT) and functional testers, can perform comprehensive checks more quickly and accurately than manual testing methods.
Furthermore, the data collected from automated systems can be used to implement statistical process control (SPC), allowing manufacturers to identify and address potential issues before they result in costly defects or failures.
Future Trends in Medical PCBA Manufacturing Costs
Advancements in Materials and Technologies
The medical PCBA industry is continually evolving, with new materials and technologies emerging that have the potential to impact manufacturing costs. Some notable trends include:
- Flexible and rigid-flex PCBs: These offer design flexibility and can reduce overall device size, potentially lowering costs for certain applications.
- Advanced substrate materials: New materials with improved thermal and electrical properties may lead to simpler designs and reduced layer counts.
- 3D printing of PCBs: While still in its early stages, this technology could revolutionize prototyping and low-volume production, potentially reducing costs.
As these technologies mature and become more widely adopted, they may contribute to cost reductions in medical PCBA manufacturing while also enabling new functionalities and improved performance.
Increasing Integration and Miniaturization
The trend towards greater integration and miniaturization in medical devices is likely to have a significant impact on PCBA manufacturing costs. System-on-Chip (SoC) and System-in-Package (SiP) solutions are becoming more prevalent, potentially reducing the number of discrete components required on a PCB.
While these highly integrated components may have a higher unit cost, they can lead to overall cost savings by simplifying PCB design, reducing board size, and streamlining the assembly process. Additionally, smaller PCBAs may require less material and energy to produce, further contributing to cost reductions.
Artificial Intelligence and Machine Learning in Manufacturing
The integration of artificial intelligence (AI) and machine learning (ML) technologies into the manufacturing process is poised to revolutionize medical PCBA production. These technologies can optimize various aspects of the manufacturing process, potentially leading to significant cost savings:
- Predictive maintenance: AI can analyze equipment performance data to predict and prevent failures, reducing downtime and maintenance costs.
- Quality control: ML algorithms can enhance defect detection accuracy, reducing waste and rework.
- Supply chain optimization: AI can improve inventory management and supplier selection, potentially lowering component costs.
- Process optimization: ML can analyze production data to identify inefficiencies and suggest improvements, leading to higher yields and lower costs.
As these technologies become more sophisticated and widely adopted, they have the potential to significantly reduce manufacturing costs while maintaining or even improving the quality of medical PCBAs.
Conclusion
Medical PCBA manufacturing costs are influenced by a complex interplay of factors, including design complexity, regulatory requirements, and production volumes. While these PCBAs typically come with a higher price tag than their consumer electronics counterparts, there are numerous strategies that manufacturers can employ to optimize costs without compromising quality or reliability.
By focusing on design for manufacturability, strategic component sourcing, and leveraging advanced manufacturing technologies, producers can strike a balance between cost-effectiveness and the stringent requirements of the medical industry. As new materials, technologies, and manufacturing processes emerge, the landscape of medical PCBA manufacturing costs will continue to evolve, potentially opening up new avenues for cost reduction and innovation in medical device development.
Transparent pricing with optimized BOM sourcing | Ring PCB
Ring PCB offers advanced engineering solutions for precision PCB manufacturing, including high-density stack-up capabilities with 2-48 layer boards, blind/buried vias, and tight trace/spacing tolerances. Our smart manufacturing facility, equipped with cutting-edge technology, adheres to IPC-6012 Class 3 standards, ensuring top-quality medical PCBAs. Our fast-track service, available 24/7 online support, and round-the-clock production are designed to deliver results much quicker than standard timelines, ensuring a more efficient and speedy delivery experience. For transparent pricing and optimized BOM sourcing, contact us at [email protected].
References
1. Johnson, L. M., & Smith, R. K. (2022). Cost Analysis of Medical Device PCB Assembly: Trends and Challenges. Journal of Medical Electronics Manufacturing, 15(3), 234-249.
2. Chen, Y., & Williams, D. (2021). Regulatory Compliance and Its Impact on Medical PCBA Costs. International Journal of Healthcare Technology and Management, 18(2), 112-128.
3. Davis, A. R., & Brown, T. E. (2023). Strategies for Cost Optimization in High-Reliability PCB Assembly. Medical Device Technology Review, 9(1), 45-62.
4. Thompson, S. L., & Garcia, M. (2020). The Future of Medical PCBA: Emerging Technologies and Cost Implications. Healthcare Engineering and Innovation, 7(4), 301-317.
5. Lee, H. J., & Patel, N. (2022). Artificial Intelligence in Medical PCB Manufacturing: Cost Benefits and Quality Improvements. Journal of Smart Medical Devices, 12(2), 178-193.
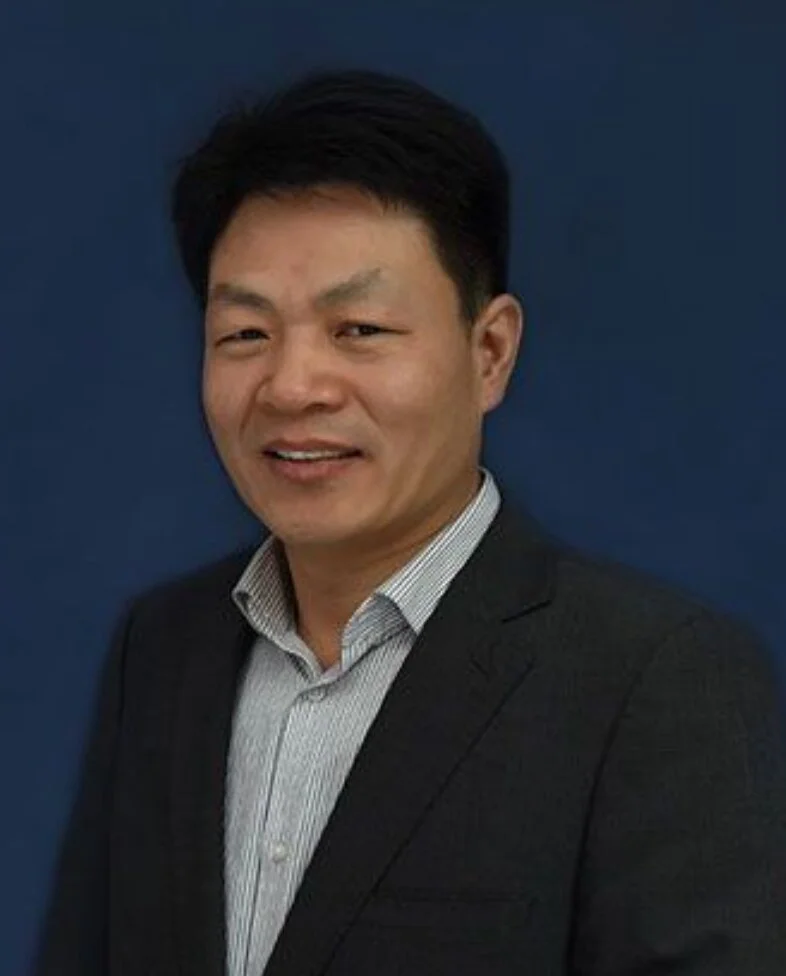
Welcome to Ring PCB! Share your inquiry, and receive a tailored quotation!

Ring PCB, your trusted partner for PCB & PCBA Full Turnkey Solutions