Power Distribution Network in PCB Assembly: Ensuring Stable Power Delivery
In modern electronics, the Power Distribution Network (PDN) within a PCB assembly serves as the circulatory system of your board—ensuring that every component receives the right amount of clean, stable power. Whether it’s a smart lock, automotive controller, or medical device, without a reliable PDN, your circuit may suffer voltage dips, performance instability, and even system failure. Building a stable PDN is not just a good design practice—it’s an absolute necessity in high-speed, high-reliability electronic systems.
Designing Robust Power Distribution Networks in PCB Assembly
A well-engineered PDN begins at the heart of your PCB assembly: the power source and its interface with the board. What follows is a strategic distribution of power through well-laid-out copper planes, power rails, vias, and decoupling networks that deliver power to each integrated circuit and passive component, often with millivolt-level precision.
To maintain performance integrity in compact, multilayer PCBs, designers use dedicated power planes with low impedance to minimize resistance and inductance. The thinner the PDN impedance, the more efficiently power is delivered during rapid current demand changes. This is particularly crucial in PCBs supporting FPGAs, high-speed transceivers, or processors with sub-nanosecond switching times.
In critical systems—especially in sectors like aerospace, telecommunications, or automotive electronics—designers go further by implementing impedance-controlled stack-ups. These may include blind/buried vias, high-Tg materials, and interleaved power-ground planes to reduce electromagnetic interference and voltage fluctuations.
Another crucial aspect is transient response. When components rapidly switch states, current demand can surge. A poor PDN responds too slowly, resulting in voltage droop and potential logic errors. The solution is a combination of proper decoupling capacitor values, proximity to ICs, and low-inductance layouts that enable fast, stable delivery of power when it's needed most.
High-density assemblies, such as those found in smart home security devices or IoT modules, require precise PDN simulation during the design phase. Tools like PI analysis software let engineers visualize how current will flow, predict noise points, and simulate the voltage ripple, allowing preemptive correction before the PCB assembly reaches manufacturing.
Key Components That Shape PDN Efficiency in PCB Assembly
An efficient PDN is not just the sum of its parts—it's the result of how those parts interact. Below are the essential elements that define PDN performance and stability.
Copper Planes and Traces
Power planes serve as broad, low-impedance highways for distributing power. Using wide copper areas instead of thin traces reduces resistive losses and minimizes IR drop. In multilayer PCBs, power and ground planes are often adjacent to form distributed capacitors, which improve signal integrity and reduce EMI.
The choice of copper thickness—commonly 1 oz or 2 oz—also affects power handling capabilities. For high-power applications, thicker copper (up to 3 oz or more) ensures reliable current distribution with lower thermal rise.
Decoupling Capacitors
Capacitors are the PDN’s local power tanks. Placed close to ICs, they smooth out voltage dips during high-speed switching. A good capacitor strategy combines multiple values:
- Small caps (e.g., 0.01μF–0.1μF): Suppress high-frequency noise.
- Mid-value caps (e.g., 1μF–10μF): Handle mid-frequency transients.
- Bulk caps (e.g., 47μF–100μF): Manage low-frequency load steps.
All must be placed with minimal loop area and short traces to reduce inductance. The effectiveness of decoupling depends not just on capacitance value, but also on ESR (Equivalent Series Resistance) and ESL (Equivalent Series Inductance).
Voltage Regulators
Voltage regulators are often used to step down supply voltages and provide stable, controlled power. Their location and thermal management are key in PDN performance. Linear regulators may introduce less noise but are less efficient, while switching regulators are efficient but need careful filtering. In complex PCB assembly, multiple voltage rails must be generated from a single source. Careful sequencing and isolation between regulators prevent cross-interference and voltage instability.
Vias and Interlayer Connections
When power or ground must move between layers, vias are used. However, they add inductance and can constrain current flow if undersized. Multiple vias in parallel or via stitching is a common technique to reduce total inductance and maintain PDN integrity. A well-designed via strategy is especially important in high-current zones or BGA package breakouts, where inadequate current-carrying paths can bottleneck power flow.
Best Practices for Power Delivery in PCB Assembly for Critical Applications
For PCB assembly projects where reliability is non-negotiable, such as medical diagnostics, industrial automation, or EV control units, adhering to PDN best practices is the only path to long-term stability.
Implement a Distributed Capacitance Strategy
Instead of clustering capacitors in a single area, distribute them across the board and near every critical IC. This avoids long paths between power source and load, reducing the effective impedance seen by fast-switching circuits. Using multiple capacitor values across various layers widens the resonance bandwidth, ensuring suppression over a full spectrum of frequencies.
Analyze the PDN Before Manufacturing
Using PDN simulation software allows engineers to analyze power flow, impedance mismatches, voltage ripple, and decoupling effectiveness before a single board is manufactured. These tools are now standard practice in complex designs and can reveal performance bottlenecks invisible in a traditional layout inspection.
Use Controlled Stack-Up and Dielectric Materials
Selecting the right dielectric constant, layer spacing, and copper weight determines how well the PDN performs. In high-speed PCBs, tight impedance control and thermal stability matter as much as raw power delivery. Materials like FR-4 may suffice for general use, but high-speed or high-frequency boards benefit from low-loss laminates.
Prioritize Thermal Management
Heat can compromise voltage regulation and damage components. Proper heat spreading, use of thermal vias, and copper pours under high-power devices ensure that PDN elements operate within spec. PDN thermal performance must be modeled, especially in densely packed or enclosed designs.
Leverage Manufacturing Expertise
Even the best PDN design can fail if the manufacturer lacks the precision to build it accurately. Selecting a PCB assembly partner with vertical integration, advanced fabrication equipment, and strict QA processes is essential for PDN success.
Conclusion
Power stability is the silent force behind every successful PCB assembly. A robust Power Distribution Network ensures every signal is supported by reliable, noise-free power, from smart lock circuits to advanced medical systems. From copper planes to capacitors, from simulation to soldering, every decision affects your system’s ability to function under real-world conditions. At Ring PCB, our commitment to power integrity is matched only by our engineering precision and manufacturing reliability.
Trusted Power Distribution PCB Manufacturer for Reliable Supply Chains | Ring PCB
At Ring PCB Technology Co., Limited, we’ve been delivering end-to-end PCB assembly solutions since 2008. Our self-owned factory integrates everything from raw material procurement to final testing, ensuring vertical control and consistency. With expertise in 2–48 layer boards, ±7% impedance control, and 3/3 mil HDI capabilities, we cater to industries that demand precision—medical, automotive, telecom, and more.
Certified under ISO9001 and IATF16949, we build every board to Class 3 standards. Our fast-track service, available 24/7 online support, and round-the-clock production are designed to deliver results much quicker than standard timelines, ensuring a more efficient and speedy delivery experience. Reach out today at [email protected] for reliable, scalable PCB solutions.
References
1. Brooks, L. & Adam, C. PCB Currents: How They Flow, How They React. An insightful look into current behavior across multilayer PCBs.
2. Johnson, H. & Graham, M. High-Speed Digital Design: A Handbook of Black Magic. Includes extensive guidance on PDN challenges and capacitor placement.
3. Bogatin, E. Signal and Power Integrity—Simplified. A go-to resource for designing stable and low-noise power systems in PCBs.
4. Deutsch, A. Power Distribution Design for High-Speed Digital Systems. A technical analysis of PDN design considerations from a systems engineering perspective.
5. Lee, J. Practical Power Integrity: Using SPICE and Mathcad for PDN Simulation. Offers real-world techniques for modeling and simulating PDN stability.
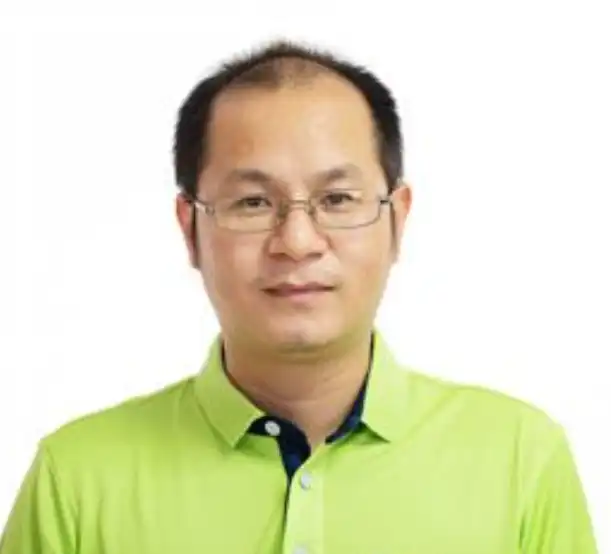
Welcome to Ring PCB! Share your inquiry, and receive a tailored quotation!

Ring PCB, your trusted partner for PCB & PCBA Full Turnkey Solutions