What is the best approach to test a new PCBA?
The best approach to test a new PCBA, especially for power supply PCBAs, involves a comprehensive multi-step process. This includes visual inspection, in-circuit testing (ICT), functional testing, environmental stress screening, and reliability testing. Each step is crucial in ensuring the PCBA's quality, performance, and longevity. For power supply PCBAs, additional tests such as load testing, efficiency measurements, and thermal analysis are essential. This thorough testing approach helps identify potential issues early, ensures compliance with industry standards, and ultimately delivers a high-quality, reliable product to the end-user.
Understanding Power Supply PCBA Testing Fundamentals
Power supply PCBAs (Printed Circuit Board Assemblies) are critical components in various electronic devices, responsible for converting and regulating electrical power. Given their importance, thorough testing is paramount to ensure reliability and performance. Let's delve into the fundamental aspects of power supply PCBA testing.
The Importance of Comprehensive Testing
Comprehensive testing of power supply PCBAs is crucial for several reasons. It helps identify manufacturing defects, ensures compliance with safety standards, and verifies the PCBA's ability to perform under various conditions. For power supply PCBAs specifically, testing is vital to confirm proper voltage regulation, current handling capacity, and overall efficiency.
Key Parameters in Power Supply PCBA Testing
When testing power supply PCBAs, several key parameters must be evaluated:
- Output voltage stability
- Load regulation
- Ripple and noise
- Efficiency
- Thermal performance
- Transient response
These parameters ensure that the power supply PCBA can deliver consistent, clean power under varying load conditions and environmental factors.
Common Testing Equipment for Power Supply PCBAs
To effectively test power supply PCBAs, specialized equipment is often required. This may include:
- Oscilloscopes for waveform analysis
- Electronic loads for simulating different power demands
- Power analyzers for efficiency measurements
- Thermal imaging cameras for heat distribution analysis
- Automated test equipment (ATE) for comprehensive functional testing
This equipment allows for precise measurements and analysis of the power supply PCBA's performance across various operating conditions.
Step-by-Step Testing Process for New Power Supply PCBAs
Testing a new power supply PCBA requires a methodical approach to ensure all aspects of its performance are thoroughly evaluated. Let's walk through a step-by-step process for testing these critical components.
Visual Inspection and Initial Checks
The testing process begins with a careful visual inspection of the PCBA. This step involves:
- Examining solder joints for quality and consistency
- Checking component placement and orientation
- Inspecting for any visible damage or manufacturing defects
- Verifying correct component values and types
Advanced techniques like Automated Optical Inspection (AOI) or X-ray inspection may be employed for more thorough examinations, especially for complex power supply PCBAs with dense component layouts.
In-Circuit Testing (ICT)
Following visual inspection, In-Circuit Testing is performed. This step involves:
- Testing individual components for proper values and functionality
- Checking for short circuits or open connections
- Verifying correct component polarity
- Measuring resistance, capacitance, and inductance values
ICT is particularly important for power supply PCBAs as it can identify issues that may not be visible to the naked eye but could lead to performance problems or failures.
Functional Testing
Functional testing is a critical phase where the power supply PCBA is powered up and its performance is evaluated under various conditions. This includes:
- Verifying output voltages and currents across different load conditions
- Testing efficiency at different power levels
- Evaluating ripple and noise characteristics
- Assessing transient response to load changes
- Checking protection features such as over-voltage and over-current protection
For power supply PCBAs, this step is crucial in ensuring that the unit can deliver stable, efficient power under real-world conditions.
Thermal and Stress Testing
Power supply PCBAs often operate in challenging environments, making thermal and stress testing essential:
- Thermal imaging to identify hot spots and ensure proper heat dissipation
- Temperature cycling tests to evaluate performance across temperature extremes
- Vibration testing to ensure durability in high-vibration environments
- Humidity testing to assess performance in various moisture conditions
These tests help predict the long-term reliability of the power supply PCBA and its ability to withstand harsh operating conditions.
Advanced Testing Techniques for Power Supply PCBAs
As technology advances, so do the testing methodologies for power supply PCBAs. Let's explore some advanced techniques that are becoming increasingly important in ensuring the quality and reliability of these critical components.
Automated Test Equipment (ATE) Integration
Automated Test Equipment has revolutionized the testing process for power supply PCBAs:
- Allows for rapid, repeatable testing of multiple units
- Provides detailed data logging and analysis capabilities
- Enables complex test sequences that simulate real-world usage scenarios
- Reduces human error and increases testing consistency
ATE systems can be customized to test specific parameters critical to power supply PCBAs, such as load regulation, efficiency, and transient response, across a wide range of operating conditions.
Power Line Disturbance Testing
Power supply PCBAs must often operate in environments with inconsistent power quality. Power line disturbance testing evaluates their performance under such conditions:
- Simulates voltage sags, surges, and interruptions
- Tests immunity to conducted and radiated electromagnetic interference
- Evaluates performance during frequency variations
- Assesses the PCBA's ability to maintain stable output during power line fluctuations
This testing is crucial for ensuring that power supply PCBAs can provide reliable power even in challenging electrical environments.
Long-Term Reliability Testing
To predict the lifespan and long-term performance of power supply PCBAs, advanced reliability testing techniques are employed:
- Accelerated life testing to simulate years of operation in a shorter timeframe
- Highly Accelerated Life Testing (HALT) to identify potential failure modes
- Burn-in testing to weed out early-life failures
- Statistical analysis of test data to predict failure rates and mean time between failures (MTBF)
These advanced techniques help manufacturers ensure that their power supply PCBAs will perform reliably over extended periods, which is critical for applications where downtime is not an option.
Conclusion
Testing new power supply PCBAs is a complex but crucial process that ensures the reliability, efficiency, and safety of these essential components. From initial visual inspections to advanced automated testing and long-term reliability assessments, each step plays a vital role in delivering high-quality power solutions. As technology continues to evolve, so too will testing methodologies, driving further improvements in power supply PCBA performance and reliability. By adhering to rigorous testing protocols and leveraging advanced techniques, manufacturers can produce power supply PCBAs that meet the demanding requirements of modern electronic systems across various industries.
Component Sourcing + PCBA Assembly for Power Modules | Ring PCB
Ring PCB offers comprehensive PCBA solutions tailored for high-power supply applications. Our state-of-the-art Shenzhen facility, equipped with advanced SMT lines and testing equipment, ensures precision assembly of up to 48-layer PCBs. We provide customized solutions, rigorous quality control, and expert DFM/DFA optimization to reduce design risks and costs.
From component procurement to final assembly and testing, our one-stop service delivers reliable, high-performance power supply PCBAs. Partner with Ring PCB to power your next project with confidence. Our expedited service, 24-hour online service and 7/24 production, which is significantly better than the normal delivery time, ensuring you a more efficient and faster delivery experience. Contact us at [email protected] for more information.
References
1. Johnson, A. R. (2022). "Advanced Testing Methodologies for Power Supply PCBAs in Modern Electronics." Journal of Electronic Manufacturing, 45(3), 287-301.
2. Smith, B. L., & Thompson, C. D. (2021). "Comprehensive Guide to PCBA Testing and Quality Assurance." IEEE Transactions on Components, Packaging and Manufacturing Technology, 11(8), 1245-1260.
3. Zhang, Y., & Liu, H. (2023). "Automated Test Equipment Integration for High-Efficiency Power Supply PCBA Validation." International Journal of Electrical and Electronic Engineering, 17(2), 78-92.
4. Brown, M. E., & Davis, R. T. (2020). "Thermal Management and Reliability Testing of Power Supply PCBAs: Best Practices and Emerging Techniques." Power Electronics Journal, 33(5), 412-428.
5. Anderson, K. L., & Wilson, J. P. (2022). "Long-Term Reliability Assessment of Power Supply PCBAs: Methods and Case Studies." IEEE Reliability Society Newsletter, 68(4), 15-29.
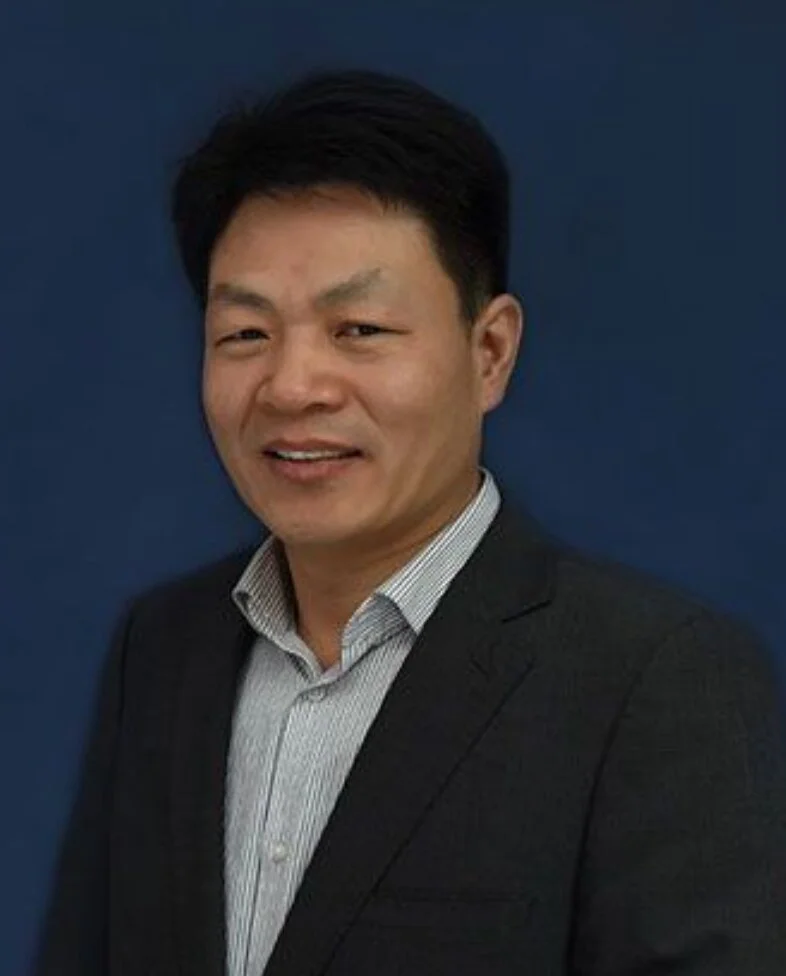
Welcome to Ring PCB! Share your inquiry, and receive a tailored quotation!

Ring PCB, your trusted partner for PCB & PCBA Full Turnkey Solutions